Causes of wire feeding issues in welding as stated by welding electrodes manufacturers
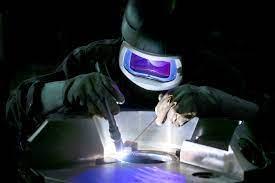
Poor wire feeding is one of the most frequent problems cited by Welding Electrodes Manufacturers as something they deal with on a regular basis. Inefficient wire feeding can result in more downtime, wasted consumables, and a reduction in the overall quality of the weld. Wire feeding problems can result from a wide range of factors. There are numerous additional problems that could be the culprit, despite the fact that welders frequently believe the filler metal is the issue.
Major reasons for wire feeding problems
Discover some of the most typical reasons for wire feeding problems in welding by reading the information below.
Tension on Wire
Improper wire tension is one of the most frequent causes of wire feeding problems. Too much strain can stretch the wire and cause wire feeding issues, bird nests, and other problems. The wire may bunch up and block the gun, though, if the tension is too low, causing the wire to become slack. Throughout the welding process, it is crucial to make sure the wire tension is set correctly in accordance with the manufacturer's instructions.
Wire Quality
Welding Electrodes Manufacturers in India should realize that the procedure of wire feeding can also be impacted by the quality of the welding wire. Poor-quality wire is more likely to develop bends, twists, and other abnormalities that can result in it getting stuck in the gun. Also, if the wire is stored in a wet area, rust or corrosion on the wire may cause problems with feeding. These issues can be avoided by using high-quality wire and maintaining it properly.
Movable rollers
Drive rollers are in charge of feeding the wire through the welding gun, and they are essential for a steady and smooth wire feed. The wire may slip or become distorted, resulting in feeding problems if the driving rollers are worn, filthy, or misaligned. Drive rollers should be cleaned, maintained, and replaced on a regular basis to help avoid these issues.
Contact Tip
The Welding Electrodes Suppliers gun's contact tip, which comes into close contact with the wire to provide a dependable and consistent wire feed, is an essential component. The wire may stick or become distorted, which might affect feeding, if the contact tip is worn, filthy, or broken. Contact tips can help prevent these issues by being cleaned and replaced on a regular basis.
Welding Conditions
Finally, the wire feeding procedure can be impacted by welding factors like voltage, amperage, and wire speed. If these settings are made improperly, the wire feed may become irregular and cause feeding problems. It is crucial to check that the welding parameters are properly established for the unique welding application and to keep an eye on them as the welding process progresses.
In conclusion,Welding Electrodes Manufacturers know a number of reasons, such as insufficient wire tension, poor wire quality, drive rollers, contact tips, and welding conditions, might result in wire feeding problems. These issues can be avoided with regular maintenance and monitoring of these components, which will also guarantee a steady and dependable wire feed for high-quality welding. This will ensure that Welding Electrodes Suppliers in India will be more productive and will have a good amount of safety for themselves as well.
- Art
- Causes
- Crafts
- Dance
- Drinks
- Film
- Fitness
- Food
- Games
- Gardening
- Health
- Home
- Literature
- Music
- Networking
- Other
- Party
- Religion
- Shopping
- Sports
- Theater
- Wellness
- IT, Cloud, Software and Technology