Different HPDE bottle testing parameters that you must know
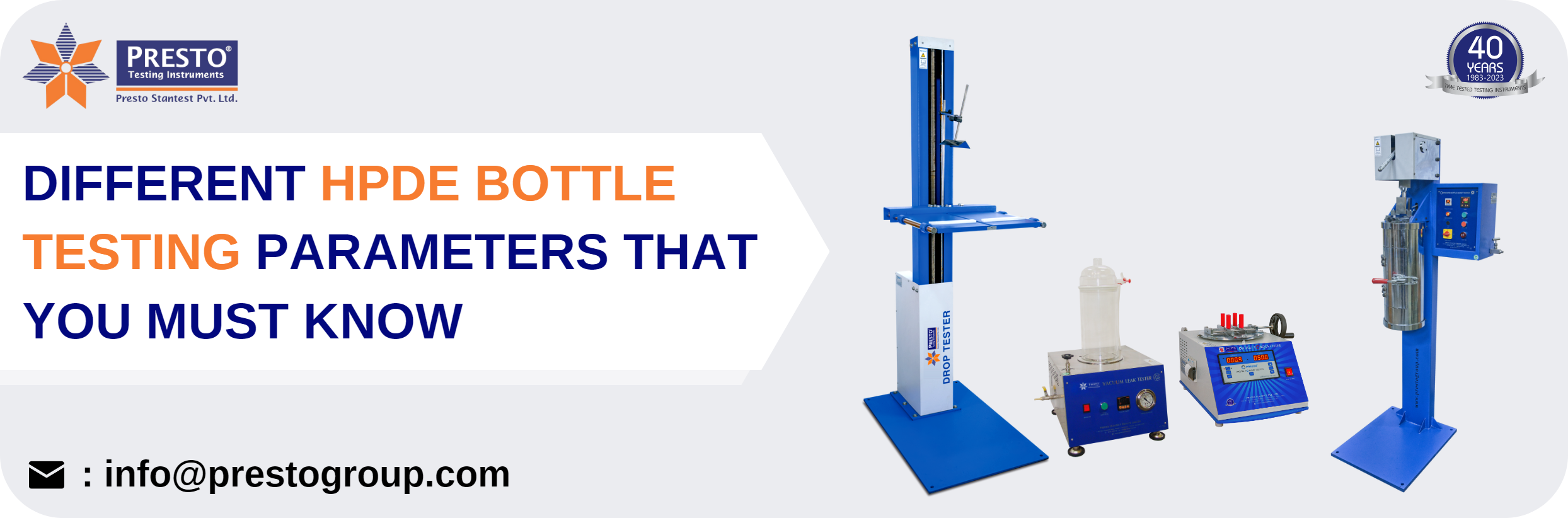
Testing HDPE (High-Density Polyethylene) bottles is crucial to ensure their quality, performance, and suitability for specific applications. Testing helps to verify that HDPE bottles meet the required quality standards and specifications. It ensures that the bottles are manufactured using the appropriate materials, processes, and controls, resulting in consistent and reliable products. Thus, if you are searching for the best HDPE bottle testing instruments, then you can go with Presto Quality Testing Instruments.
Our bottle testing equipment has been designed as per industry standards that make it easy for the manufacturers to conduct quality tests on these products. Whenever you are going to test these bottles, then there are different bottle testing parameters that one must take care of to ensure quality products will be delivered to the customers.
In this blog, we are going to provide you with information about HDPE bottle testing parameters and the importance of testing these products accurately. So, let us get started!
Importance of quality and safety in HDPE bottle manufacturing
HDPE (High-Density Polyethylene) bottles are widely used in various industries due to their excellent durability, and cost-effectiveness. However, it is crucial to ensure that these bottles meet stringent quality and safety standards to avoid any potential risks to the end users. Poorly manufactured HDPE bottles can lead to issues such as leakage, contamination, and compromised integrity, which can ultimately impact the reputation and bottom line of the manufacturers.
To mitigate these risks, manufacturers must prioritize quality and safety in the manufacturing process by implementing thorough testing parameters. These testing parameters not only help identify any potential flaws in the bottles but also ensure that the bottles can withstand the rigors of storage, transportation, and usage. By adhering to these parameters, manufacturers can deliver high-quality HDPE bottles that meet regulatory requirements and provide a reliable packaging solution for their customers.
Thus, it is important for bottle manufacturers to test their manufactured products accurately and ensure quality testing. Out of so many lab testing instruments available in the market, you can easily use these top 3 HDPE testing instruments and ensure accurate quality results.
Now, let us discuss different quality parameters that you must test using HDPE lab testing instruments.
Different quality parameters that you must test for HDPE Bottles
To ensure the quality and safety of HDPE bottles, several testing parameters must be considered. These parameters help evaluate different aspects of the bottles, including their physical strength, and integrity. Let's explore some of the most common HDPE bottle testing parameters in detail.
-
Burst strength testing for HDPE bottles
A bursting strength tester is a crucial parameter that assesses the ability of HDPE bottles to withstand internal pressure. This test involves subjecting the bottles to increasing pressure until they burst. By measuring the burst strength, manufacturers can determine the maximum pressure the bottles can withstand without rupturing. This parameter is particularly important for HDPE bottles used in industries such as pharmaceuticals and chemicals, where the contents may exert significant internal pressure.
During the burst strength testing, the bottles are gradually pressurized until they fail. The pressure at which the bottles burst is recorded and used as a benchmark for evaluating their strength. burst testing machine testing parameter helps ensure that HDPE bottles can safely contain their contents without any risk of leakage or rupture, providing peace of mind to both manufacturers and end-users. Presto digital bottle burst tester is the quality testing instrument to test the bursting strength of HDPE bottles.
-
Leak testing for HDPE bottles
Leak testing is another critical parameter for evaluating the quality and safety of HDPE bottles. This test aims to identify any potential leaks or weak spots in the bottle's structure that could lead to leakage or contamination. Leakage from HDPE bottles can have serious consequences, especially in industries such as pharmaceuticals and food and beverages, where product integrity is of utmost importance.
By conducting leak testing, manufacturers can ensure that their HDPE bottles are free from any leaks or weak spots, guaranteeing the integrity and safety of the products they contain. To conduct leak tests for HDPE bottles, you can easily make use of a Presto vacuum leak tester.
-
Drop testing for HDPE bottles
Drop testing is an essential parameter for evaluating the impact resistance of HDPE bottles by drop impact tester. This test simulates real-world scenarios in which bottles may be accidentally dropped during handling or transportation. By subjecting the bottles to controlled drops from specified heights, manufacturers can assess their ability to withstand impact without rupturing or compromising their integrity.
During drop test, the bottles are dropped onto different surfaces, to simulate various impact conditions. The bottles are then inspected for any visible damage, including cracks, fractures, or deformations. Bypassing the drop testing parameter, HDPE bottles demonstrate their ability to withstand accidental drops and ensure the safety of their contents. Presto drop strength tester is widely used in the bottle industry to test the drop strength of HDPE bottles accurately.
-
Torque testing of HDPE bottles
Torque testing is an important parameter for HDPE bottle testing because it assesses the integrity of the bottle closure (such as caps or lids) and ensures that it can provide an effective seal.
Torque testing helps determine the appropriate tightness or closure torque required to create a reliable seal between the HDPE bottle and its closure by a torque tester. It ensures that the closure is tightened sufficiently to prevent leaks, thereby preserving the integrity and safety of the packaged contents. Insufficient torque may lead to leaks or premature opening of the bottle, while excessive torque can damage the bottle or make it difficult for users to open. Thus, with the use of Presto torque meter manufacturers can easily determine the closing and opening torque value of PET bottles and ensure that quality materials will be delivered to the customers.
If you need more information about our different bottle testing instruments, then you can give us a call at +91-9210903903 or email us at info@prestogroup.com. Our team of technical experts will consult you regarding all your needs and queries.
Content Source Link - Different HPDE bottle testing parameters that you must know
- Art
- Causes
- Crafts
- Dance
- Drinks
- Film
- Fitness
- Food
- Spiele
- Gardening
- Health
- Startseite
- Literature
- Music
- Networking
- Andere
- Party
- Religion
- Shopping
- Sports
- Theater
- Wellness
- IT, Cloud, Software and Technology