Grinding Segments Enhancing Precision and Productivity in Material Processing
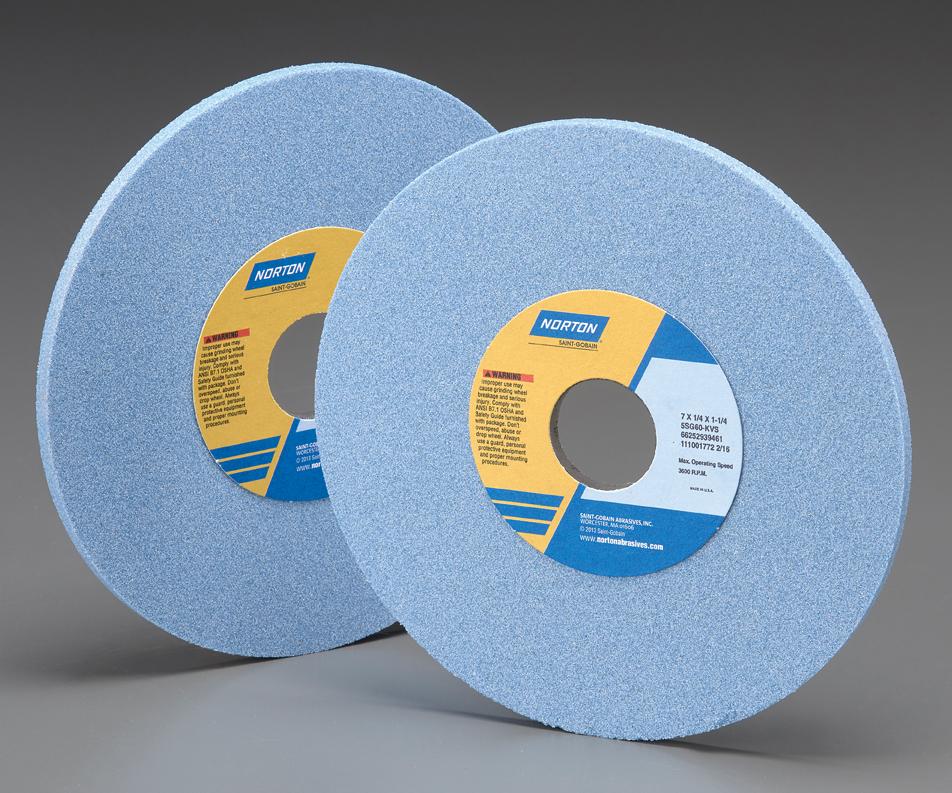
Grinding is an essential process in the manufacturing and metalworking industries, responsible for shaping and finishing various materials with precision. Among the crucial components of a grinding operation are grinding segments, which play a vital role in achieving the desired results. In this blog post, we will delve into the significance of grinding segments, their types, and the impact they have on enhancing precision and productivity in material processing.
The Role of Grinding Segments:
Grinding segments are abrasive tools used in surface grinding machines. They are composed of abrasive grains held together by a bonding material. These segments are available in various shapes and sizes, designed to be mounted on grinding wheels or grinding plates. The primary purpose of grinding segments is to remove material from the workpiece, resulting in a smoother surface finish and dimensional accuracy.
Types of Grinding Segments:
- Straight Grinding Segments: These are the most common type and are used for flat surface grinding. They efficiently remove excess material from the workpiece, leaving a uniform finish.
- Cup Grinding Segments: Cup-shaped segments are ideal for grinding curved surfaces or beveling edges. They offer aggressive material removal and are often used for rough grinding applications.
- Dish Grinding Segments: Dish-shaped segments are used for tool sharpening and intricate grinding tasks. Their shape allows for precise control over the material removal process.
- Cylinder Grinding Segments: Cylinder segments are well-suited for grinding internal surfaces, such as bores and pipes.
Benefits of Grinding Segments:
- Precision: Grinding segments enable precise material removal, ensuring that the workpiece meets the required specifications and tolerances. This precision is crucial in industries like aerospace and automotive, where components must adhere to strict quality standards.
- Efficiency: By using grinding segments, manufacturers can achieve higher material removal rates, leading to improved productivity. This efficiency not only reduces production time but also lowers overall costs.
- Versatility: With various shapes and sizes available, grinding segments can be tailored to suit specific applications. Whether it's removing excess material or achieving a fine finish, there's a segment for every task.
- Longevity: High-quality grinding segments are designed to withstand wear and tear, resulting in longer tool life and reduced downtime for replacements.
Conclusion:
Grinding segments are indispensable tools in material processing, offering precision, efficiency, versatility, and longevity. Manufacturers across industries rely on these abrasive components to achieve the desired surface finish and dimensional accuracy of their products. By harnessing the power of grinding segments, businesses can optimize their production processes and stay competitive in today's demanding market.
- Art
- Causes
- Crafts
- Dance
- Drinks
- Film
- Fitness
- Food
- Игры
- Gardening
- Health
- Главная
- Literature
- Music
- Networking
- Другое
- Party
- Religion
- Shopping
- Sports
- Theater
- Wellness
- IT, Cloud, Software and Technology