Grinding Is a Widely Used Process in Manufacturing Industries
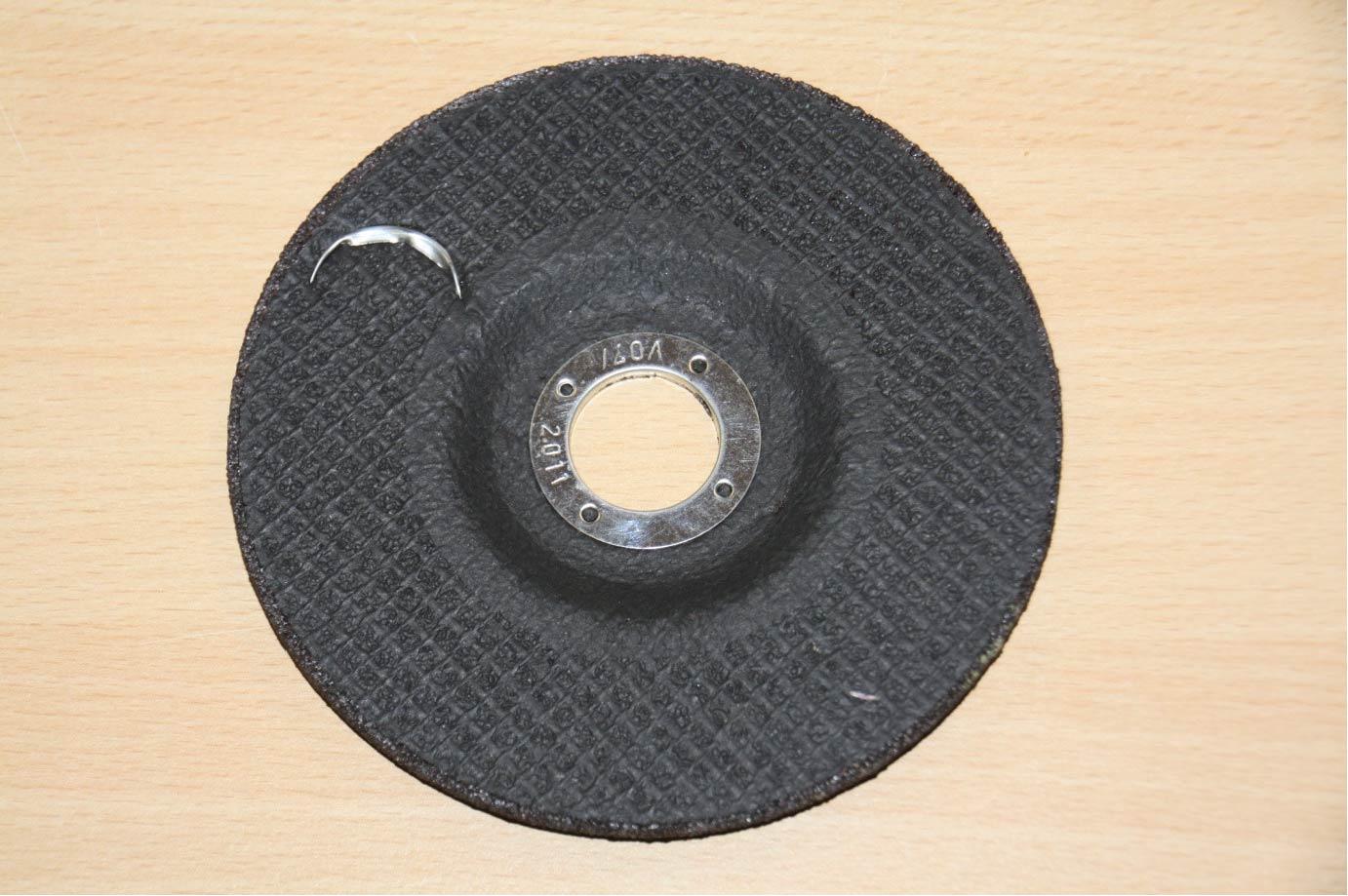
Finishing and shaping various materials, including metals, ceramics, and plastics. It involves removing small amounts of material using an abrasive wheel or belt. Although grinding is an efficient process, it can lead to defects that affect the quality of the finished product.
Grinding defects can occur due to several reasons, including improper machine settings, worn-out abrasive tools, and incorrect grinding techniques. The most common grinding defects include:
- Burn marks: These are dark or discolored spots on the surface of the workpiece caused by excessive heat generated during grinding. Burn marks can weaken the material and make it more prone to cracking or failure.
- Chatter marks: These are periodic surface imperfections that result from the vibration of the grinding machine or the workpiece. Chatter marks can affect the dimensional accuracy of the workpiece and cause it to fail prematurely.
- Wheel loading: This defect occurs when the abrasive particles become clogged with material, reducing the effectiveness of the grinding wheel. Wheel loading can lead to poor surface finish and premature wear of the grinding wheel.
- Edge chipping: This defect occurs when the edges of the workpiece become damaged or chipped during grinding. Edge chipping can compromise the strength and durability of the workpiece.
To prevent grinding defects, it is essential to use the correct grinding techniques, maintain the grinding machine properly, and use high-quality abrasive tools. Grinding operators should also monitor the process closely and make adjustments as necessary to ensure the quality of the finished product.
In conclusion, grinding defects can have a significant impact on the quality and performance of manufactured products. By understanding the common grinding defects and taking steps to prevent them, manufacturers can ensure that their products meet the desired specifications and are free from defects.
- Art
- Causes
- Crafts
- Dance
- Drinks
- Film
- Fitness
- Food
- Games
- Gardening
- Health
- Home
- Literature
- Music
- Networking
- Other
- Party
- Religion
- Shopping
- Sports
- Theater
- Wellness
- IT, Cloud, Software and Technology