What is an ultrasonic level sensor, and how does it work to measure liquid or solid levels in various applications
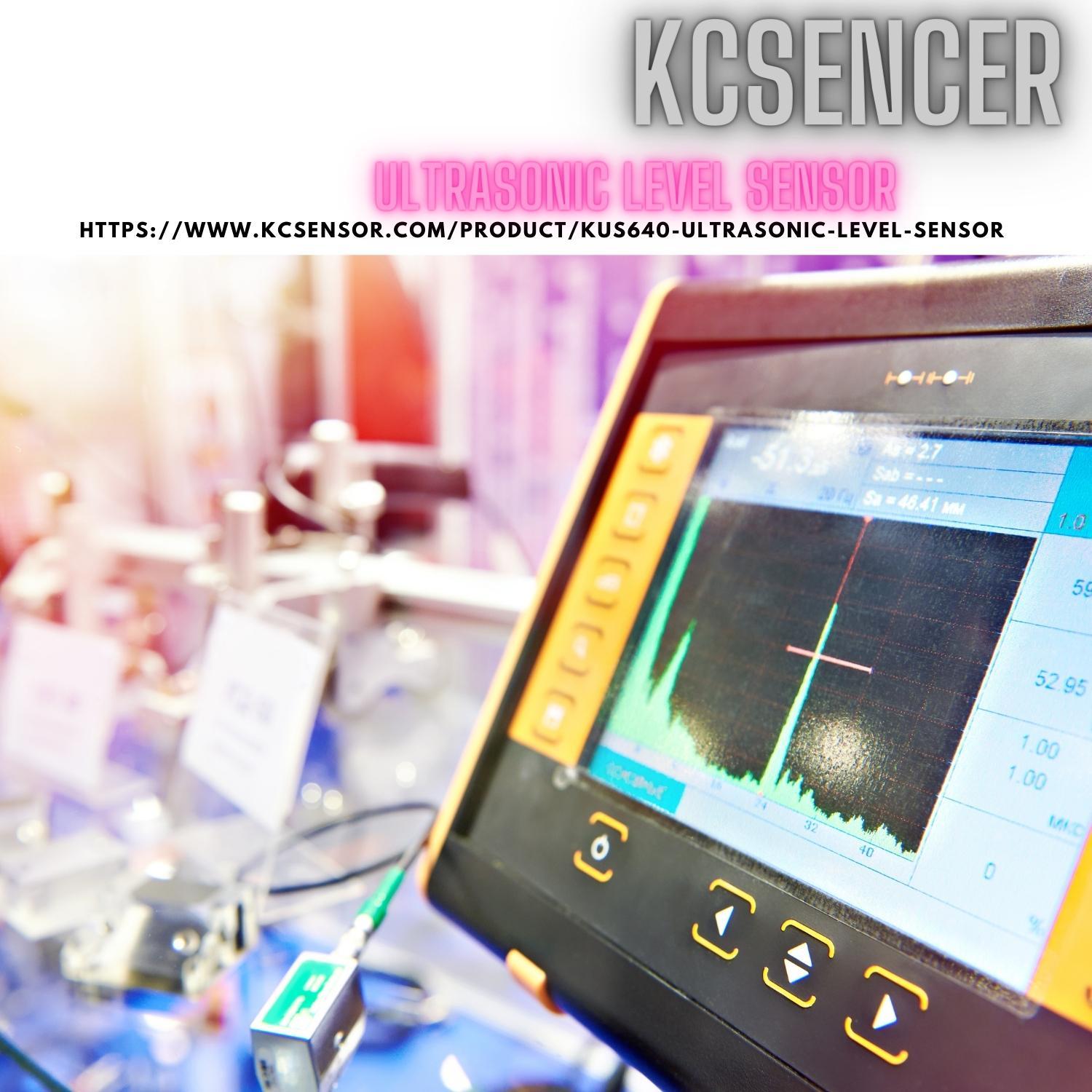
An ultrasonic level sensor is a device commonly used in industrial and commercial settings to measure the level of liquid or solid substances within a container or tank. It operates based on the principles of ultrasonic technology, which involves the emission of high-frequency sound waves and the measurement of their return time to determine the distance to an object. Here's a detailed explanation of how it works and its applications:
The ultrasonic level sensor consists of two essential components: a transducer and a control unit. The transducer is responsible for generating ultrasonic waves, typically in the range of 20 kHz to 200 kHz. These waves are emitted downward from the sensor towards the material whose level needs to be measured.
When the ultrasonic waves encounter the surface of the material (liquid or solid), they are reflected back towards the sensor. The sensor's control unit precisely measures the time it takes for the emitted waves to bounce back, known as the "time of flight." By knowing the speed of sound in the air, which is approximately 343 meters per second at room temperature, the control unit calculates the distance from the sensor to the material's surface.
The calculated distance is then used to determine the level of the material in the container or tank. This information can be displayed on a digital readout, transmitted to a control system, or used to trigger alarms or automated processes when certain level thresholds are reached.
Ultrasonic level sensors are highly versatile and find applications in a wide range of industries, including manufacturing, agriculture, wastewater treatment, and chemical processing. They are particularly useful in situations where other level measurement methods, such as float switches or capacitive sensors, may be impractical due to factors like corrosive substances, foaming liquids, or varying material densities.
In summary, ultrasonic level sensor provide an accurate and non-contact method for measuring liquid or solid levels in various industrial and commercial scenarios. Their ability to work reliably in challenging environments makes them a valuable tool for process control and monitoring applications.
For more information visit kcsencer.
- Art
- Causes
- Crafts
- Dance
- Drinks
- Film
- Fitness
- Food
- Games
- Gardening
- Health
- Home
- Literature
- Music
- Networking
- Other
- Party
- Religion
- Shopping
- Sports
- Theater
- Wellness
- IT, Cloud, Software and Technology