Machine Condition Monitoring Market Is Estimated To Witness High Growth Owing To Rising Need For Preventive Maintenance
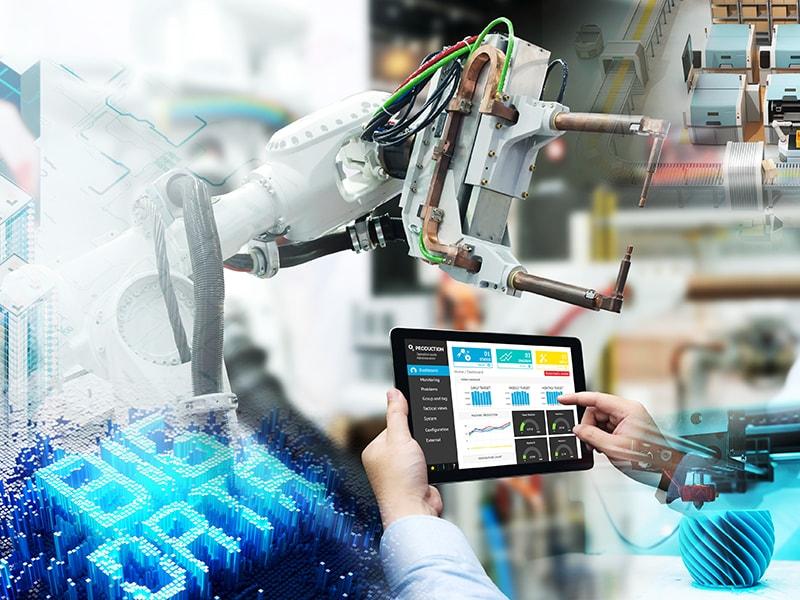
The machine condition monitoring market is estimated to be valued at US$ 3965.6 Mn in 2023 and is expected to exhibit a CAGR of 9.1% over the forecast period 2023 to 2030, as highlighted in a new report published by Coherent Market Insights.
Market Overview:
Machine condition monitoring is the process of monitoring the condition of machines in real time to detect and diagnose faults. It helps predict potential problems and enable maintenance before breakdowns or failures occur. The main products used for machine condition monitoring are vibration monitoring, thermography, lubricating oil analysis, corrosion monitoring, ultrasound emission and motor current signature analysis. These products monitor various parameters like temperature, vibration levels, lubricant condition, corrosion levels and acoustic emissions to detect anomalies in machines.
Market Dynamics:
The machine condition monitoring market is primarily driven by the growing need for predictive maintenance to avoid unplanned downtime and increase equipment lifespan. Predictive maintenance helps detect potential machine or component failures at an early stage using condition monitoring devices. This allows maintenance to be scheduled at a convenient time to avoid costly unplanned breakdowns. For example, vibration monitoring helps detect imbalance, misalignment or bearing issues in rotating equipment like pumps, motors and fans before they lead to failures. Similarly, thermography identifies hot spots in electrical panels or on machine surfaces indicating loose connections or component overheating.
Further, rising industrial automation and growing emphasis on reducing operational costs is also fueling the adoption of machine condition monitoring solutions. Automated condition monitoring allows round the clock monitoring of machines without needing continuous human supervision. This helps minimize downtime and maintenance costs in the long run.
SWOT Analysis
Strength: Machine condition monitoring helps reduce unexpected downtime and maintenance costs which increases productivity. It provides real-time equipment performance data to take preventive measures. Remote monitoring capabilities allow addressing issues from any location.
Weakness: High initial investment and additional costs associated with installation and integration can be prohibitive for small organizations. Data security is also a concern as sensitive equipment details are monitored online.
Opportunity: Growing adoption of IIoT and Industry 4.0 offers huge growth potential for machine condition monitoring technologies. Predictive maintenance using machine learning and AI further improves performance and optimization.
Threats: Adoption of open-source solutions and custom-built monitors pose pricing pressure on established vendors. Macroeconomic slowdowns can reduce capital expenditure on condition monitoring systems.
Key Takeaways
The Global Machine Condition Monitoring Market Size is expected to witness high growth, exhibiting CAGR of 9.1% over the forecast period, due to increasing demand for predictive maintenance of industrial assets.
The North American region dominates the market currently due to presence of large manufacturing sector. Asia Pacific is projected to be the fastest growing region owing to industrial expansion and growing infrastructure development.
Key players operating in the machine condition monitoring market are Meggitt Sensing Systems, SKF AB, Parker Kittiwake, Rockwell Automation Inc., Thermo Fisher Scientific Inc., GE Bently Nevada, Perkin Elmer Inc., Emerson Electric Co., Gastops Ltd, Nippon Avionics Co. Ltd, AMETEK Spectro Scientific, FLIR Systems Inc. and Fluke Corporation.
Get more insights on this topic: https://www.zupyak.com/p/3941145/t/online-ecommerce-is-fastest-growing-segment-fueling-the-growth-of-the-machine-condition-monitoring-market
- Art
- Causes
- Crafts
- Dance
- Drinks
- Film
- Fitness
- Food
- Spellen
- Gardening
- Health
- Home
- Literature
- Music
- Networking
- Other
- Party
- Religion
- Shopping
- Sports
- Theater
- Wellness
- IT, Cloud, Software and Technology