Unveiling the Secrets of Successful Injection Molding with Cutting-Edge Materials
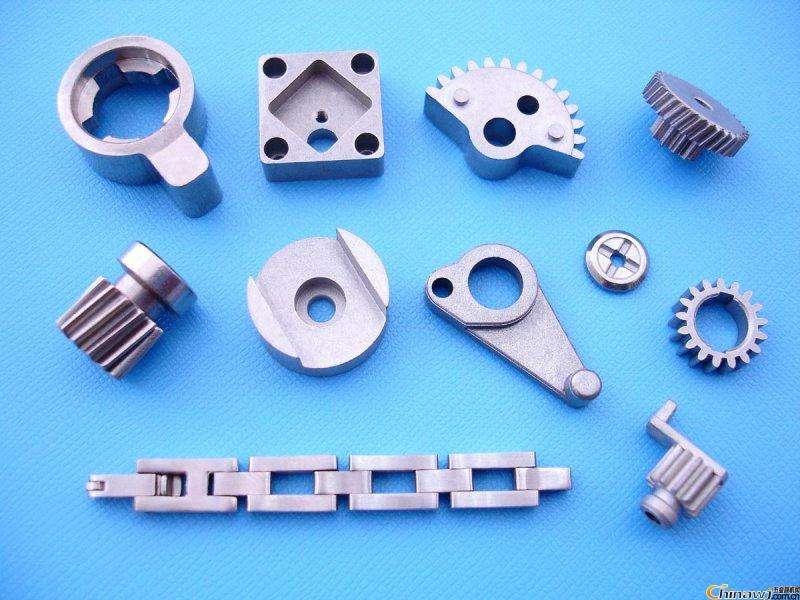
Injection molding is one of the most popular manufacturing processes used today for mass production of plastic parts. In this process, plastic material in granular or pellet form is melted and injected into a mold cavity where it cools and hardens to the shape of the cavity. The materials used for injection molding play a crucial role in determining properties of the final molded part. This article discusses various common materials used for injection molding along with their key properties and applications.
Thermoplastics
Thermoplastics make up the majority of materials used for injection molding due to their ability to repeatedly melt and solidify without any substantial change in properties. Some of the commonly used thermoplastics are:
Polypropylene (PP): PP is a durable, stiff material resistant to chemicals and moisture. It is lightweight, low cost and recyclable. Its applications include automotive components, consumer products, packaging and medical devices.
Polystyrene (PS): PS has a smooth surface finish and clarity ideal for packaging applications like food containers, lids and clamshell cartons. General purpose grades are also used for toys, appliances and medical devices.
Acrylonitrile Butadiene Styrene (ABS): ABS combines the strength of acrylonitrile and butadiene with the resilience of styrene. It provides impact resistance even at low temperatures. Popular uses include housings for appliances, telephones, automotive interior and exterior parts.
Polyethylene (PE): PE comes in high density grade for containers and low density grade for films. It is highly corrosion resistant and provides an effective barrier against moisture, gas and odors making it suitable for packaging of food and non-food items.
Polycarbonate (PC): With high impact strength and optical transparency, PC finds application in lenses, protective shields, medical devices and electrical components requiring flame resistance.
Nylon: Nylons like Nylon 6 and Nylon 6,6 have self-lubricating properties making them suitable for mechanical parts requiring low friction. They are resistant to oils, grease and detergents. Common uses include gears, pulleys, bushings and other automotive and industrial components.
Engineering Thermoplastics
Engineering thermoplastics have enhanced mechanical, thermal and chemical resistant properties compared to general purpose polymers. Some engineering materials molded include:
Polyphenylene Sulfide (PPS): PPS has high heat resistance, flame resistance and corrosion resistance. It is used for electrical/electronic components, sensors and connectors requiring high temperature stability.
Polyetherimide (PEI): PEI exhibits high strength, rigidity and melting point enabling applications in electrical switches, connectors and plugs where mechanical and thermal performance is essential.
Polyetheretherketone (PEEK): PEEK stands up to extreme conditions with chemical inertness and high temperature resistance. Consequently, it finds application in semiconductor manufacturing equipment, medical devices like implants and valves.
Fluoropolymers: Varieties like PTFE and PFA provide non-stick, low friction and extremely chemical resistant surfaces for components in semiconductor manufacturing, food processing and chemical processing equipment.
Liquid Silicone Rubber (LSR): LSR offers biocompatibility, flexibility and transparency after curing. Medical devices like syringe seals, artificial implants and breast implants take advantage of these properties.
Materials continue to play a key role in pushing Injection Molding Materials further into miniaturized electronic components, medical devices, automotive applications like electric vehicles and space applications. New grades tailored to specific applications and environmental sustainability continue to emerge. With advancements in both materials and processing technologies, injection molding will likely remain an indispensable manufacturing process for mass producing high quality plastic parts.
The Different Types of Thermoplastics
As discussed earlier, thermoplastics make up a major share of injection molding materials due to their moldability and recyclability. Within thermoplastics, there are different material types classified based on their chemical composition and resulting properties.
- Olefin plastics derived from petroleum include polypropylene (PP) and polyethylene (PE) commonly used for packaging, automotive, and consumer products.
- Styrenics include polystyrene (PS) and acrylonitrile butadiene styrene (ABS) valued for clarity and impact resistance in applications like food packaging and electronics housings.
- Polyamides or nylons have self-lubricating characteristic ideal for low friction mechanical parts. Nylon 6 and Nylon 6,6 are popular engineering grades.
- Polycarbonate (PC) and polymethyl methacrylate (PMMA) termed engineering thermoplastics deliver high strength and heat resistance for automotive and electronics.
- High performance plastics like polyphenylene sulfide (PPS) and polyetheretherketone (PEEK) withstand extreme conditions in industries like semiconductor fabrication.
Thus material selection depends on the specific property requirements of the end-use application to deliver optimized performance from injection molded parts.
Engineering Advancements in Materials
Materials science continues advancing injection molding capabilities into new applications. Some key developments include:
- Long fiber reinforced thermoplastics (LFT) and long fiber thermoplastic composites (LFT-C) with 30-40% long fiber content deliver high strength to weight ratio for structural automotive under-the-hood components.
- Transparent amorphous resins like polymethyl methacrylate (PMMA) and polycarbonate (PC) enable headlight lenses, instrument panels and laptop housings requiring optical clarity.
- Specialty elastomers and Liquid Silicone Rubber (LSR) provide flexibility, biocompatibility and transparency for medical components like breast implants and insulin pumps.
- Flame retardant materials protect electrical equipment from overheating. Certifications like UL 94 restrict use of halogenated compounds leading to development of halogen-free alternatives.
- Recyclable plastics using post-consumer recycled content reduce environmental footprint without compromising on mechanical properties.
Continued material innovations will see injection molding finding applications in more challenging environments like aircraft interiors, offshore foundations and space structures in future.
Injection molding continues to evolve driven by innovations in polymer materials science. New material grades extend the process capability into miniaturized electronics, biomedical and high strength structural applications.
For more insights, Read- https://www.marketwebjournal.com/injection-molding-materials-growth-market-size-share-analysis/
Get more insights on this topic: https://masstamilan.tv/business-spend-management-software-enabling-organizations-to-gain-operational-efficiencies/
- Art
- Causes
- Crafts
- Dance
- Drinks
- Film
- Fitness
- Food
- Giochi
- Gardening
- Health
- Home
- Literature
- Music
- Networking
- Altre informazioni
- Party
- Religion
- Shopping
- Sports
- Theater
- Wellness
- IT, Cloud, Software and Technology