Piping Stress Company
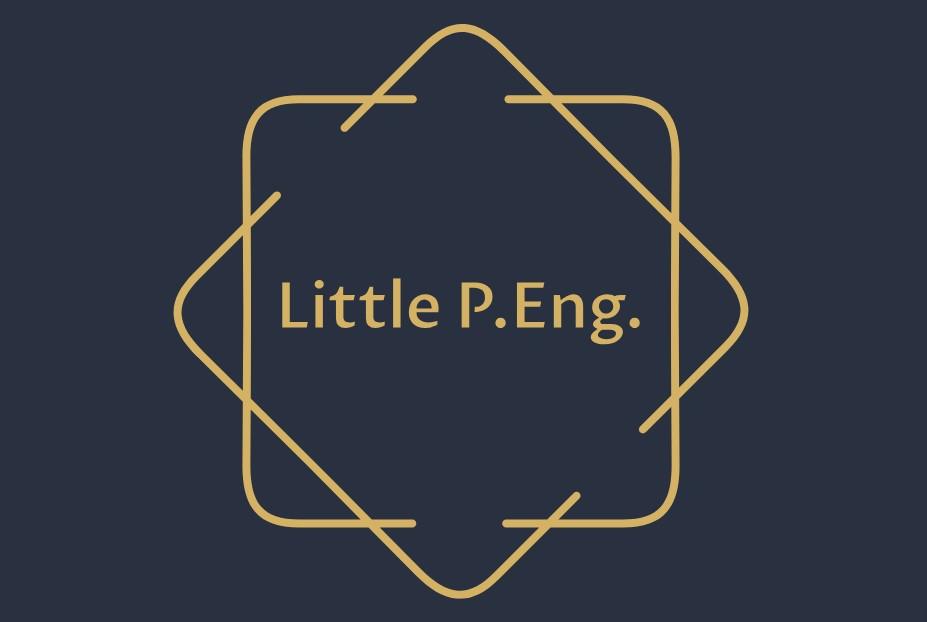
Pipe Stress Company was founded in 1975 as a piping engineering firm that has a broad range of expertise for oil and gas development projects. They provide stress analysis, vibration analysis, thermal transient analysis and nuclear class 1 analysis for upstream and downstream oil & gas processing plants including refineries, petrochemical, LNG, GTL and cogeneration power plant projects around the world. Their team of experts provides design and engineering services that includes determining support loads, conducting engineering computations, assessing nozzle loads and collaborating with other departments. They also review project documentation and advise management on engineering matters.
The firm is a member of the American Society of Mechanical Engineers and has a Professional Engineer License in Texas and Louisiana. They specialize in performing stress and vibration analysis for piping systems, designing piping support components and evaluating nozzle loads. Their team has a Bachelor’s Degree in Mechanical Engineering and extensive experience with piping, FEA and vibration analysis. They have completed thousands of standard piping stress calculations as well as special analyses for elevated temperature piping, close coupled reciprocating compressors, reformer lines, expansion joints and slug flow.
Piping Stress Company was created to solve tough technical problems. Their work has led them into new markets and industries as they tackled problems related to refining, cogeneration power, slug flow and even the space shuttle launch system. As the world moves toward cleaner energy solutions, they have expanded their research into the areas of composite repair and integrity management and even opened a full scale laboratory for testing of pipes.
They recently helped a large oil company in the Gulf of Mexico to evaluate their FPSO project for a major refinery. They performed a complete vibration study of the FPSO and found that it was not meeting its service requirements due to a poor vibration response caused by improper support design. They then provided recommendations and design changes to improve the FPSO.
All piping has a natural tendency to move and expand in response to temperature change. This expansion will exert axial (X) and lateral (Y) load on the piping. The resulting bending stresses and stress concentrations must be considered in the design of the piping system. This is done by estimating the thermal growth between anchor points and assessing how the piping supports, expansion joints, slide plates, etc. will guide the expansion and absorb the resulting stresses.
It is important to understand that each line of piping in a system has its own unique dynamics that must be considered in the overall stress analysis of the system. Oftentimes these dynamics are not fully understood when the line is connected to and reacting with equipment such as pumps, compressors and other pieces of process equipment. This is why it is crucial that engineers who perform stress analysis for these connections have a good understanding of the equipment process function and the internal equipment geometry. If the piping system is not designed correctly, catastrophic failure can occur.
- Art
- Causes
- Crafts
- Dance
- Drinks
- Film
- Fitness
- Food
- الألعاب
- Gardening
- Health
- الرئيسية
- Literature
- Music
- Networking
- أخرى
- Party
- Religion
- Shopping
- Sports
- Theater
- Wellness
- IT, Cloud, Software and Technology