Engineering Plastics: An Essential Part of Modern Technology
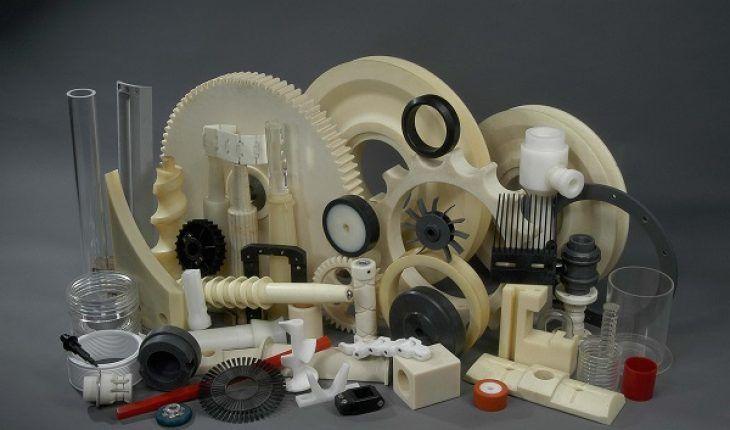
Plastics have revolutionized the way we live and have become an integral part of our daily lives. From household items to automobiles to medical devices, plastics play a vital role everywhere. When it comes to highly engineered and sophisticated applications, common plastics like PVC or styrene don't provide the necessary properties. This is where engineering plastics come into the picture. Engineering plastics have specially tailored material properties that make them ideal for advanced applications. Let's take a closer look at these specialty plastics.
What are Engineering Plastics?
Engineering plastics, also known as technical plastics, are a class of plastics that exhibit superior mechanical and thermal properties compared to commodity plastics like polyethylene and PVC. They derive their properties through engineering at the molecular level by manipulating characteristics like density, crystalline structure, temperature resistance, and strength. Some key types of engineering plastics include polyamides (nylons), polycarbonates, polyacetals, fluoropolymers, polysulfones, and liquid crystal polymers among others.
Mechanical Properties
High strength, stiffness, and dimensional stability are the hallmarks of Engineering Plastics. This allows them to withstand heavy loads, impact, vibration and harsh operating conditions. For example, nylon has a high tensile strength and can substitute metal parts in many applications. Polycarbonate has 4 times more impact strength than glass hence finds use in riot shields and safety glasses. The stiffness of engineering plastics eliminates the need for additional reinforcement unlike common plastics.
Thermal Properties
Thermal management is crucial in high-performance applications. Engineering plastics excel in withstanding high and low operating temperatures. Polycarbonate has a glass transition temperature of 147°C making it suitable for under-hood automobile components. PEEK resists temperatures as high as 260°C allowing its use in down-hole oil & gas extraction components. PTFE or Teflon is stable up to 260°C and finds application in non-stick cookware.
Electrical Properties
With their inherent resistance to electrical conductivity, many engineering plastics double up as electrical insulators. Polyamides and polyesters have low surface resistivity making them candidates for electrical components. Liquid crystal polymers are also semi-conductive, replacing metals in some circuit boards. Polyetherimide has a very high dielectric strength, utilized in switchgears & electrical motors.
Chemical Resistance
From fuels to solvents to acids, engineering plastics are highly inert and non-reactive toward aggressive chemicals. Nylon resists gasoline, alkalis, and diluted acids used in pipe fittings. PEEK withstands corrosion by most industrial chemicals, employed for pipes, valves and pumps. PTFE is non-reactive toward nearly all chemicals, ideal for chemical storage and transport.
Applications in Various Industries
Automotive
In automotive, engineering plastics replace metals in under-hood components where heat resistance is paramount. Polyamides form timing belt covers, intake manifolds, oil/air filters. Polycarbonate serves windows, headlamp lenses. ABS is used in fender parts, seat components. The materials withstand engine temperatures upto 120°C.
Electrical & Electronics
Properties like high insulation, withstands heat aging, gain & loss rigidity with temperature variation makes engineering plastics ideal for electrical components. Polyamides, PBT, PPS form housings, connectors & switches. LCP is used in antennas, circuit boards, PC/ABS in laptops and power tools.
Aerospace
Engineering Plastics like PEEK, PEK perform at cryogenic & high temperature applications and maintain dimensional stability at varying pressures. Commonly used in seals, bearings bushings, brackets in aircraft interiors & engine parts like fuel nozzles.
Medical
Biocompatibility & durability makes engineering plastics a premium choice for medical devices. PEEK implants compensate high joint loading. Polycarbonate forms protective eyewear. Nylon tubing & connectors transfer fluids in medical equipment, hospitals.
With continuously evolving material properties, engineering plastics are enabling new technological possibilities across industries. Sustainable production methods will further cement their role as a green alternative to metals & conventional plastics. Their versatile adaptability keeps engineering plastics at the forefront of innovation in product design & advanced applications for the future.
Get more insights on this topic:
https://www.newsstatix.com/engineering-plastics-the-future-materials-for-advanced-applications/
- Art
- Causes
- Crafts
- Dance
- Drinks
- Film
- Fitness
- Food
- Giochi
- Gardening
- Health
- Home
- Literature
- Music
- Networking
- Altre informazioni
- Party
- Religion
- Shopping
- Sports
- Theater
- Wellness
- IT, Cloud, Software and Technology