Due to its versatility of operation and high productivity, Cone Crushers are ideally suited for a range of applications in various industries:
Construction Industry
Cone crushers are widely used for crushing natural stones like granite, trap rock, limestone for making aggregates for construction works. The uniformly cubical shaped aggregates improve the quality of concrete.
Mining Industry
For crushing hard and abrasive minerals like iron ore, copper ore, gold ore etc. Cone crushers excel in secondary and tertiary crushing stages at mining sites. Their capacities meet commercial scale production requirements.
Aggregate Production
For manufacturing artificially cubical shaped aggregates from hard rocks like basalt, granite, traps used in road construction, ballast manufacturing units depend on cone crushers.
Industrial Manufacturing
For intermediate and fine size reduction of abrasive materials like bauxite, coal, slag etc. used in cement, ceramic and glass industries. Cone crushers produce consistent fine aggregates.
Key Advantages
Cone Crushers offer several advantages over conventional jaw or impact crushers:
- More compression force leads to higher yield compared to jaw & impact crushers per unit power.
- Lubrication system and hydraulic crushing ensures less machine maintenance leading to higher uptime.
- Adjustable discharge setup lets produce custom size aggregates as per requirement.
- Wear parts such as concave, mantle can be easily replaced minimizing downtime for repairs.
- Finer and cubical shape product with less contamination from foreign materials.
- Suitable for crushing wide range of hard and abrasive materials across applications.
Factors to Consider
While selecting an appropriate Cone Crusher, factors like material type, its hardness, desired size, production volume capacity, budget play an important role. Some other important factors to consider are:
- Machine size (Cone diameter): Larger size for high production, smaller for low tonnage.
- Type of movement: Choose spring, hydraulic or compound based on need.
- Feed opening size: Affects throughput size - smaller for finer product.
- CSS (Clearance between concave-mantle): More for tougher materials, less for soft.
- Product sizes: Select models that produce within size ranges needed.
- Operating costs: Fuel, lubrication, maintenance, power consumption.
- Life cycle costs: Spare part replacement, total expenditure over years of use.
Explore more information on this topic, Please visit-
https://www.pressreleasebulletin.com/cone-crusher-size-and-share-analysis-growth-trends-and-forecasts/
Mastering Cone Crushers Understanding, Types, Applications, and Advantages
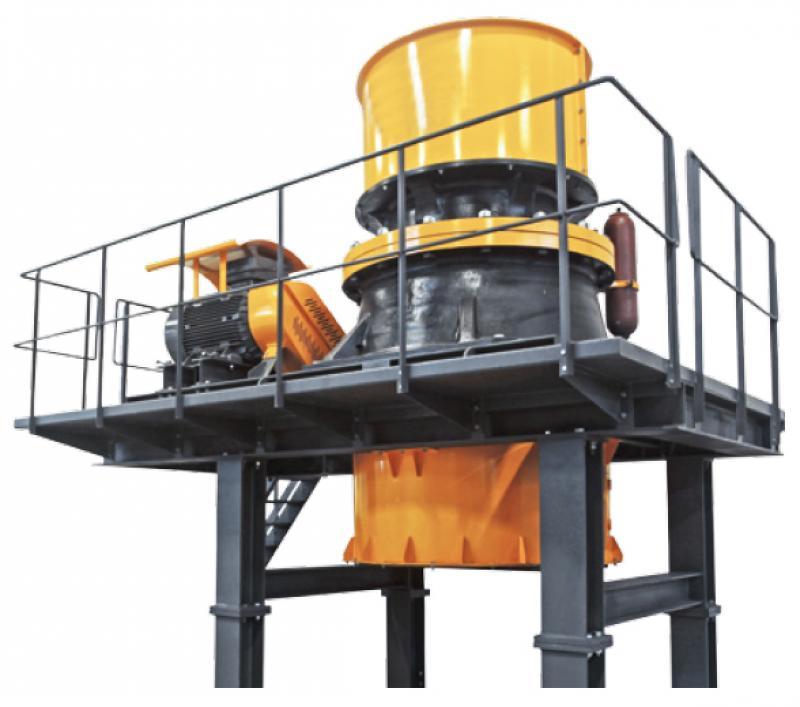