Safety Instrumented System - Ensuring Safety in Process Industries
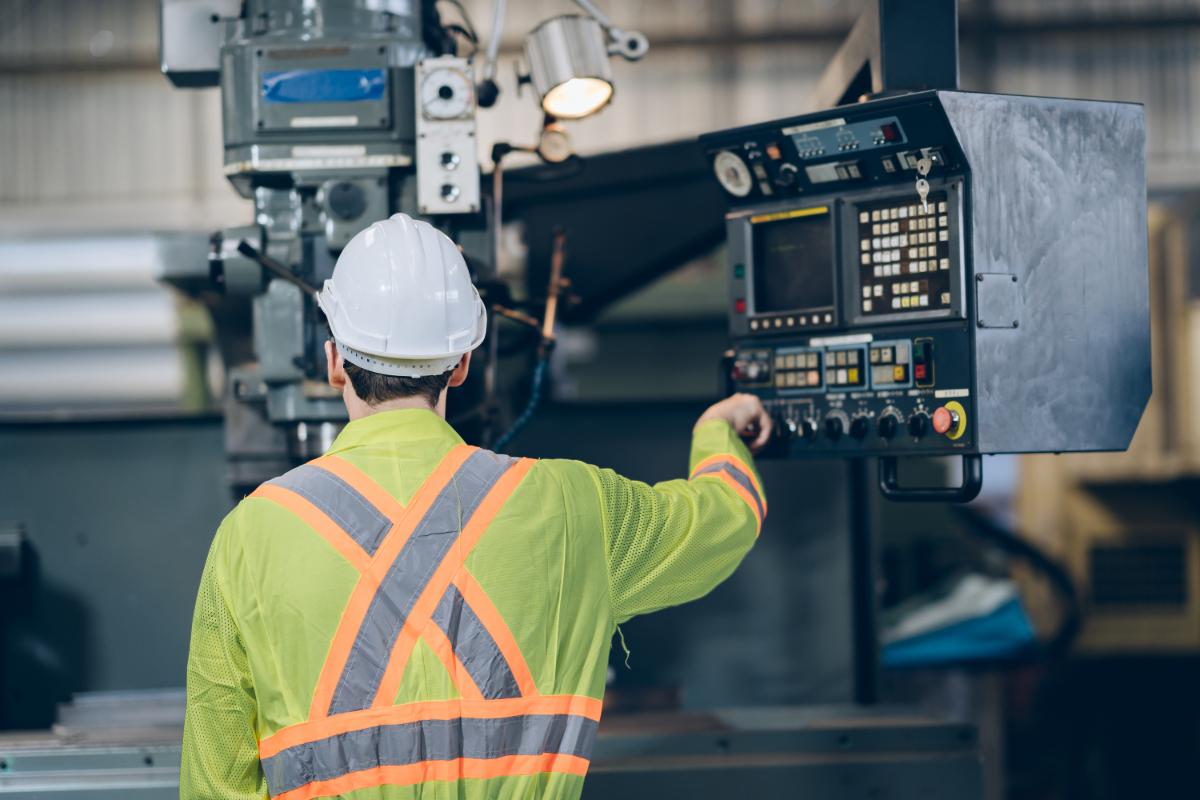
Process industries use complex machinery and handle hazardous materials on a daily basis. A single accident can have devastating consequences on both human lives as well as the environment. To prevent such catastrophes, industries employ strict safety protocols and employ advanced technological solutions. One such important technology used for process safety is Safety Instrumented System or SIS.
What is a Safety Instrumented System?
A Safety Instrumented System refers to an independent and highly reliable system designed to take the process to a safe state when defined hazardous conditions are detected. The primary function of a SIS is to prevent or mitigate the consequences of potentially dangerous failures or deviant situations. It works in conjunction with the basic process control system but operates independently without relying on it.
A typical SIS comprises of field sensing instruments or transmitters that continuously monitor process parameters like temperature, pressure, flow etc. These sensors transmit the parameter values to a logic solver which checks if the values exceed predefined safety limits. If a safety limit is breached, the logic solver triggers safety instrumented functions (SIFs) via final control elements like shut-off valves to avoid hazardous situations. SIFs are designed to maintain the process in a defined safe state until the normal operation can be restored.
Key Components of a SIS
Field Devices: These are sensors, transmitters and analyzers located in the field that continuously monitor process parameters. Common field devices include temperature sensors, pressure transmitters, flow meters etc.
Logic Solver: Also called a Safety Programmable Logic Controller (SPLC), it receives input signals from field devices and runs safety logic programs to check for safety trips. It triggers SIFs in case of a safety trip.
Final Control Elements: These are devices like shut-off valves, emergency shutdown valves etc. that are activated by the SPLC to take the process to a predefined safe state.
Power Supply: SIS requires a reliable independent power source like batteries or UPS to work even during plant power failure scenarios. This ensures functional operation at all times.
Bypass Switches: Provide a means to take the SIS out of operation temporarily for testing or maintenance purposes while keeping the process running.
Annunciator: Provides visual alerts in the control room about the status of SIS like current operating mode, active trips etc. This aids process monitoring.
Emergency Shutdown System: Often integrated with SIS, it can be manually triggered by operators to shutdown entire sections or plants during emergency situations.
Designing and Testing a Robust SIS
The key success factors for an effective SIS include robust design, sufficient testing and strict operational discipline. During design phase, proper allocation of safety instrumented functions is critical. Strict requirements are set for reliability, response time and availability. Redundancy with voting logic is commonly used.
After installation, SIS has to undergo exhaustive testing during pre-commissioning and commissioning stages to validate design integrity and parameters. This includes proof tests and diagnostic tests of sensors, logic solvers and final elements. Regular testing helps uncover weaknesses early.
Strict operational practices are followed with limited access, comprehensive documentation and rigorous change management process. Bypass protocols with timeout limits prevent extended operation without safety layers. Periodic audits and functional safety assessments ensure continuous performance.
Applying SIS Principles in Other Industries
The concepts and standards used for SIS design are now being adopted in other high-risk domains beyond process industries. Rail transport networks employ train protection systems based on independent safety layers for collision avoidance.
Nuclear power plants have multiple independent shutdown systems along with extensive instrumentation for flawless operation. Aviation relies on fly-by-wire control augmentation to maintain aircraft stability automatically during critical flight phases.
Emerging applications include functional safety for autonomous vehicles, medical devices, robotics and smart grids. The goal remains the same - to add robust and reliable safeguards that can activate independently to ward off potential hazards. This strengthens the overall safety integrity level across many complex modern systems.
With increasing complexity of industrial processes and stakes involving human lives and environment, functional safety has become a strategic imperative. Safety Instrumented Systems play a pivotal role by incorporating design resilience and independent protection layers. Their stringent engineering and validation procedures set a high standard. Ongoing advancements will further strengthen safe operation in high-risk sectors through smarter instrumentation, deep learning algorithms and integrated functional safety approaches.
Get More Insights On This Topic: https://www.newsanalyticspro.com/fortifying-protection-understanding-safety-instrumented-systems/
- Art
- Causes
- Crafts
- Dance
- Drinks
- Film
- Fitness
- Food
- Games
- Gardening
- Health
- Home
- Literature
- Music
- Networking
- Other
- Party
- Religion
- Shopping
- Sports
- Theater
- Wellness
- IT, Cloud, Software and Technology