The Wonderful World Of Precision Gearboxes
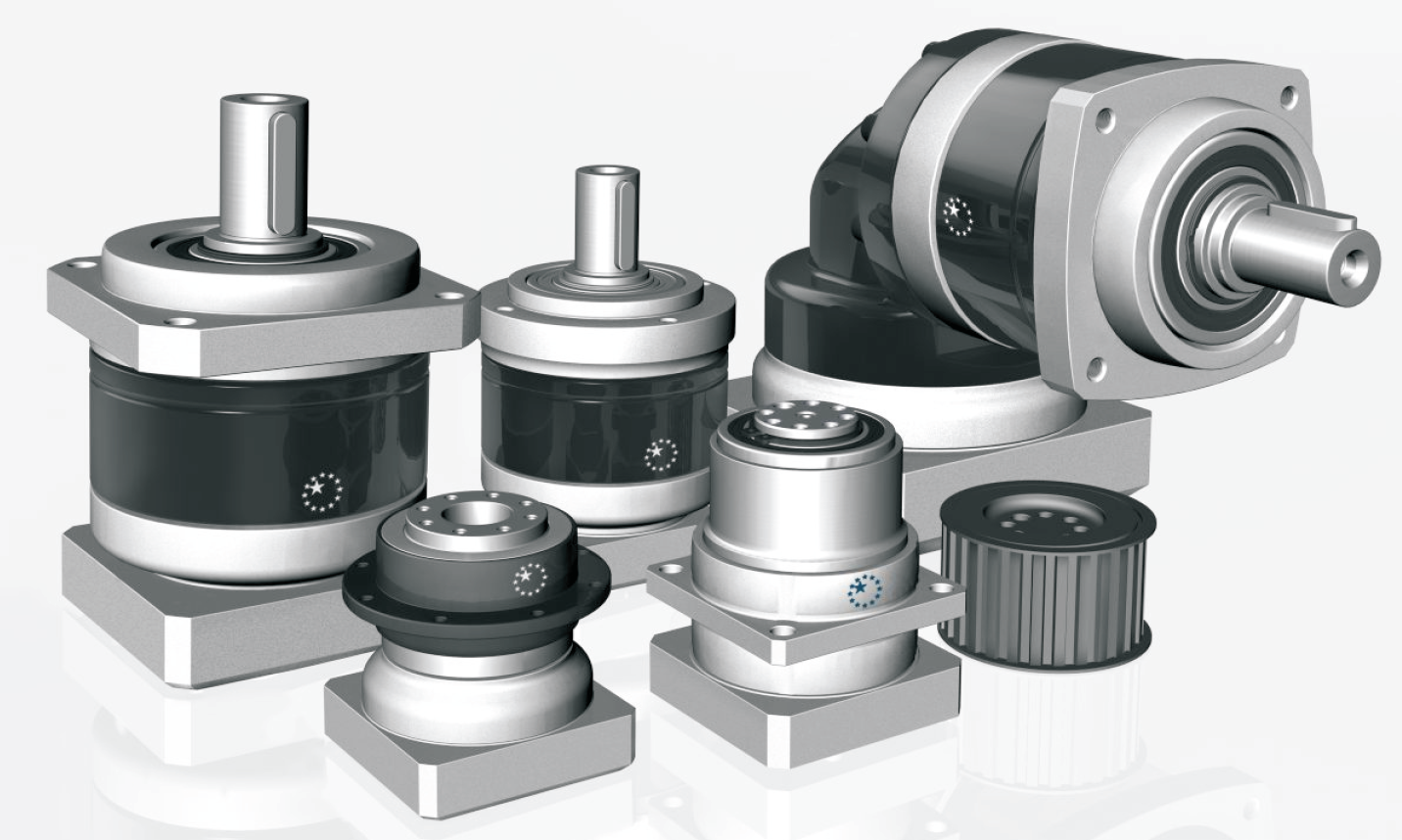
Gearboxes play a crucial role in many machines and mechanical systems by changing the speed, torque, and direction of a power source. Among the various types of gearboxes available, precision gearboxes stand out for their high accuracy and precise control capabilities. In this article, we will take a deeper look into precision gearboxes - what makes them special, their applications, design and manufacturing process.
What is a Precision Gearbox?
A precision gearbox refers to a customized gearbox designed to operate with extremely high precision and low tolerances. Some key characteristics that distinguish a precision gearbox include:
accuracy: Precision gearboxes can achieve gear meshing errors of less than 2-3 microns, which is nearly 100 times more accurate than a standard automotive gearbox. This level of accuracy enables precision control.
Rpeatability: The transmission ratio and output motion of a precision gearbox is repeatable to within a few microradians. This consistency is crucial for applications requiring synchronized motion.
Backlash: Precision gearboxes are designed and manufactured to minimize backlash or play between gear teeth. Very small backlash of less than 5 microns is common.
Load capacity: While maximizing precision, precision gearboxes can also handle substantial loads and torque requirements depending on the application.
Applications of Precision Gearboxes
Given their high accuracy and repeatability, precision gearboxes find application in industries where synchronized motion and precision are paramount. Here are some key application areas:
Robotics: Precison robot arms, pick and place machines commonly use precision gearboxes to enable accurate positional control and repeatable motion.
Semiconductor manufacturing: Lithography machines, steppers used in IC production rely on precision gearboxes to achieve sub-micron placement of circuits on wafers.
Medical devices: Surgical robots, MRI machines, dental chairs use precision gearing for synchronized motion critical for safety and accuracy in medical procedures.
Optics: Precision Gearboxe rotate lenses, mirrors and other optical components with utmost alignment in telescopes, microscopes and inspection systems.
3D printing: 3D printers that use stereolithography or laser sintering employ precision gearing to maneuver print heads, platforms and lasers with nanometer level positioning.
Design and Manufacturing Process
The dimensional precision and repeatability delivered by precision gearboxes is a result of their meticulous design and manufacturing process. Here are the key steps:
Design: Gear profiles, dimensions, tolerances and types are carefully selected based on torque-speed requirements. Modeling validates transmission ratios.
Materials: High-grade, precisely-controlled alloys like hardened steel and stainless steel are preferred for their strength and dimensional stability.
Cutting: Gears are single-point cut on high-precision CNC hobbing or shaping machines to an accuracy of 1-2 microns.
Heat treatment: Case hardening via carburizing or nitriding increases hardness and wear resistance of gear teeth.
Finishing: Gear teeth are ground and hardened to achieve roughness of 0.1Ra or better and necessary finish.
Assembly: Components are assembled within tight tolerances in cleanrooms using precision tools to prevent defects.
Testing: Gearboxes undergo dynamic, thermocycling and lifetime testing to validate precision and durability.
Customization is a hallmark of precision gearbox manufacturing as non-standard ratios, torque capabilities, enclosure types and mounting configurations can be incorporated. Modern 3D printing and EDM techniques are also helping achieve new levels of precision.
Quality Assurance and Certifications
Maintaining highest precision over the operational lifetime is critical for repeatable performance of precision gearboxes. Leading manufacturers:
Perform ISO 9001 certified quality processes
Issue test & calibration certificates with each unit
Offer customized preventive maintenance programs
Use FEA, lubrication experts for reduced wear & noise
Provide applications support from conceptualization stage
Precision gearboxes supplying industries like semiconductors are often NSF H1 certified for incidental food contact. Medical grade boxes meet biocompatibility & electromagnetic standards like ISO 13485 & IEC 60601-1.
Precision gearboxes exemplify the pinnacle of gear design and manufacturing technology. Their high accuracy and repeatability enables critical applications across industries. With continuous innovation, precision gearing will keep solving synchronization challenges for cutting-edge mechanical systems.
For more insights, read- https://www.pressreleasebulletin.com/precision-gearbox-trends-size-and-share-analysis/
- Art
- Causes
- Crafts
- Dance
- Drinks
- Film
- Fitness
- Food
- Games
- Gardening
- Health
- Home
- Literature
- Music
- Networking
- Other
- Party
- Religion
- Shopping
- Sports
- Theater
- Wellness
- IT, Cloud, Software and Technology