Key Aspects Of The Trivalent Chromium Plating Process
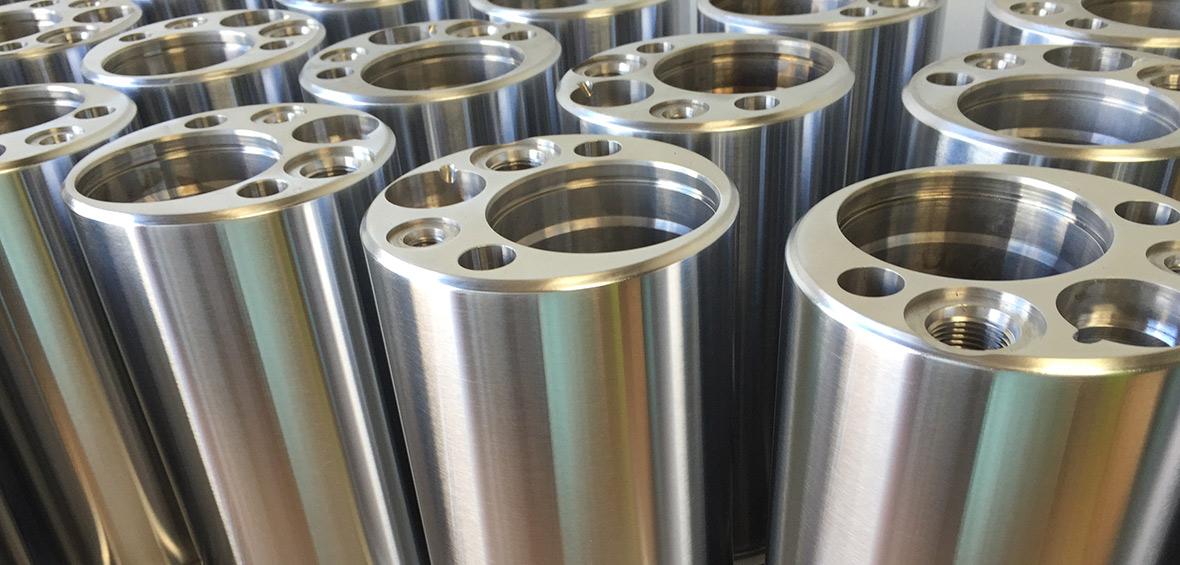
Trivalent chromium finishing is an electroplating process used to deposit a protective coating of trivalent chromium on metal parts. This chromium plating offers excellent corrosion resistance and is becoming increasingly popular as an alternative to traditional hexavalent chromium plating due to its non-toxic and environmentally friendly nature. This article explores the trivalent chromium finishing process in detail along with its advantages over conventional chromium plating and applications.
The Trivalent Chromium Plating Process
The trivalent chromium plating process involves placing the metal parts that need protection into a chrome plating bath containing trivalent chromium salts like chromium sulfate or chromium chloride. Electric current is then passed through the bath, which causes the trivalent chromium ions to deposit uniformly as a thin film onto the cathode parts.
Some key aspects of the trivalent chromium plating process include:
- Pretreatment: Parts are first cleaned and activated using alkaline cleaners, acid dips, and rinses to remove oils and prepare the metal surface for plating.
- Plating tank: The trivalent chromium plating solution contains trivalent chromium salts, brighteners, buffering agents, and other additives to ensure even deposition of chromium. Proprietary additives prevent oxidation to the toxic hexavalent state.
- Current application: A direct current voltage is applied using the parts as the cathode and insoluble anodes like titanium. This facilitates the reduction of Trivalent Chromium Finishing ions and their uniform deposition on the cathode parts.
- Post-plating rinses: Parts are rinsed after plating to remove residues from the surface. They may also undergo additional treatments like passivation.
- Drying and packaging: Parts are dried and packaged for shipping after thorough rinsing and quality inspection.
Key Advantages of Trivalent Chromium Plating
Compared to traditional hexavalent chromium plating, trivalent chromium finishing offers several advantages:
Environmental Friendliness
- It contains no toxic hexavalent chromium, eliminating the health, safety, and environmental risks linked to hexavalent chromium. Wastewater can be treated and disposed of safely.
Superior Corrosion Resistance
- Tests show the corrosion resistance of trivalent chromium coating is on par or even better than hexavalent chromium in various corrosive environments like salts sprays.
Uniform, Dense Coatings
- Trivalent chromium baths deposit uniform, pinhole-free coatings ranging from 0.2 to 2.5 micrometers in thickness, protecting metals from corrosion.
compatibility with automotive standards
- Trivalent chromium coating meets specifications for use in automotive, aerospace and industrial applications according to various international standards like ASTM B688.
Low operational costs
- Operational costs are lower than hexavalent chromium plating as no extra precautions are needed regarding toxic wastewater treatment.
Potential Applications
With its environmental friendly profile and corrosion protection, trivalent chromium plating is suited for:
Automotive Components
- Parts for engines, transmissions, chassis greatly benefit from the corrosion resistance of trivalent chromium against various automotive fluids, salts, abrasion.
Industrial Hardware
- Bolts, screws, nuts, machinery parts see extended life and lowered maintenance costs with a trivalent chromium coating.
Aerospace Applications
- Trivalent chromium is commonly used in aircraft components that require lightweight rust and corrosion protection.
Architectural Hardware
- Door handles, locks, railings, etc. installed outdoors perform better with trivalent chromium's barrier against environmental degradation.
Military and Marine Hardware
- Parts subjected to marine environments, off-road conditions can be protected cost-effectively using non-toxic trivalent chromium plating.
Future of Trivalent Chromium Plating
With increasing environmental regulations against hexavalent chromium worldwide, trivalent chromium finishing is expected to become the dominant chromium plating process. Manufacturers recognise its compliance with industry standards while providing eco-friendly corrosion protection. As bath chemistries and plating parameters continue optimizing, trivalent chromium's service life, shelf life and uniformity will further improve. With no future restrictions anticipated, it will remain a viable surface engineering solution, safeguarding infrastructure from corrosion and protecting investments for many years ahead.
Trivalent chromium plating offers metal parts a safe, non-toxic and environmentally compliant means of corrosion protection through dense, uniform chromium coatings. Its properties match or surpass traditional hexavalent chromium plating. With the advantages of being hexavalent-chromium free and meeting global industrial standards, trivalent chromium finishing is emerging as the chromium plating method of choice across sectors worldwide.
Get More Insights On This Topic: https://www.trendingwebwire.com/trivalent-chromium-finishing-an-environment-friendly-process/
- Art
- Causes
- Crafts
- Dance
- Drinks
- Film
- Fitness
- Food
- Games
- Gardening
- Health
- Home
- Literature
- Music
- Networking
- Other
- Party
- Religion
- Shopping
- Sports
- Theater
- Wellness
- IT, Cloud, Software and Technology