X-Ray Machine Manufacturing: X-Ray Imaging Has Been One Of The Most Important Medical Tools Since Its Discovery
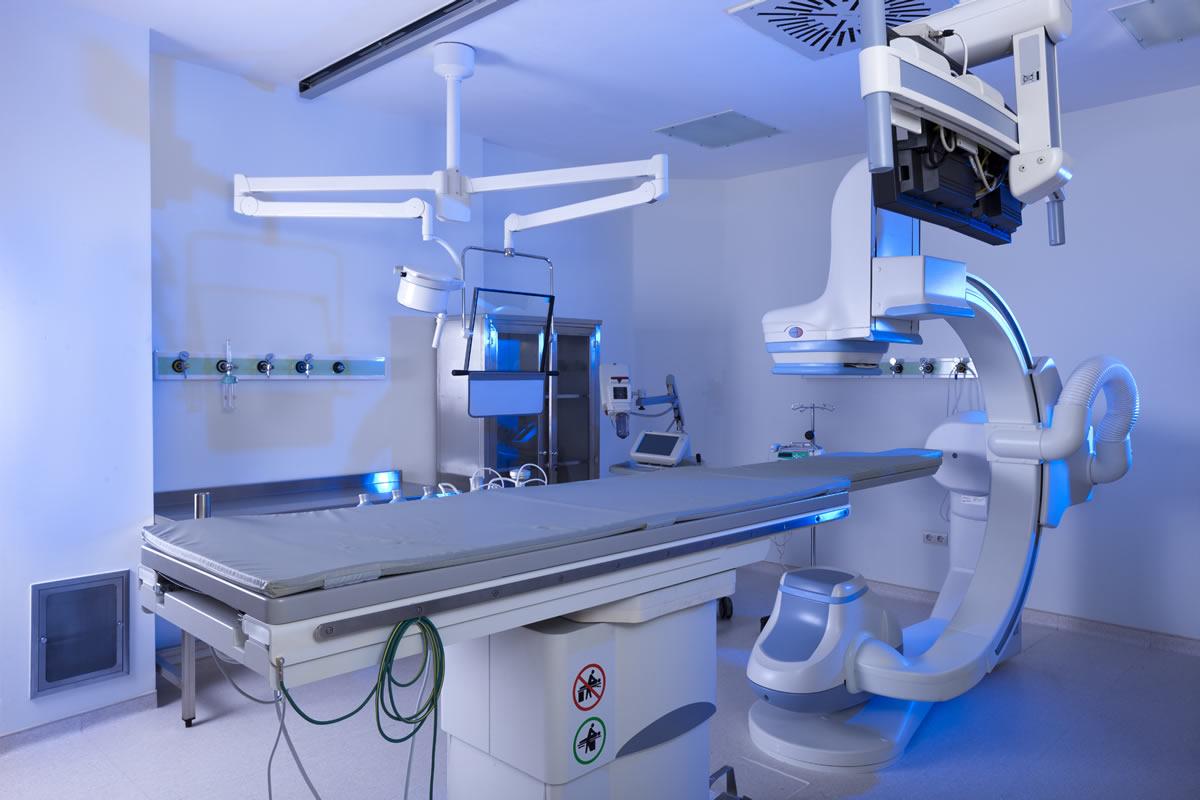
X-ray imaging has been one of the most important medical tools since its discovery in 1895. X-rays have revolutionized the fields of medicine and industry by allowing us to see inside the human body and manufactured products in a safe, non-invasive way. The technology behind x-ray machines has advanced significantly over the past century, leading to more powerful, precise and portable devices. In this article, we will take an in-depth look at the manufacturing process of modern x-ray machines and the innovations driving the industry forward.
Components of an X-ray Machine
A basic x-ray machine consists of several key components:
X-ray Tube
At the heart of every x-ray system is the x-ray tube. The tube houses an electron gun that ejects electrons and a metal target that the electrons collide with. This collision produces x-rays through a process called bremsstrahlung. Advanced x-ray tubes can be Micro Focus or Nano Focus, allowing sharper images. Tube technology continues to improve yield and lifetime.
Filter
An x-ray tube produces a range of radiation frequencies, but only a narrow band is useful for imaging. X-ray filters select this narrow spectrum by absorbing other frequencies. Filters are made of high-Z materials like molybdenum and are precisely cut to filter x-rays.
Collimator
To minimize exposure of the patient to stray radiation, collimators are used. Consisting of heavily shielded materials with adjustable openings, collimators shape the x-ray beam directly onto the area being imaged. Modern collimators have motorized, computer-controlled operation for precision collimation.
Detector
X-ray detectors capture the image, with earliest units using film but now primarily digital flat panel detectors. Advanced amorphous silicon and CMOS detectors provide high resolution and sensitivity for clearer images. Detectors are integrated into the tubehead or control unit.
Control Console
Central to the machine is the control console, housing high voltage generators, computers and electronics to operate the system. Console software controls exposure factors, archive and transfer images, and in newer units provides advanced post-processing tools.
Manufacturing Process
Manufacturing an X-Ray System involves extensive precision engineering with tight quality controls. Key stages of the manufacturing process include:
Materials Selection and Procurement
High purity semiconductor wafers and advanced metals are selected for components. Raw materials undergo stringent quality testing to meet specifications.
Component Fabrication
Individual components like tubes, detectors, collimators and electronics are fabricated in controlled clean rooms. Amorphous silicon panels for detectors require vacuum deposition of thin film transistors.
Assembly and Integration
Components like the tubehead and control console are assembled on automated lines. Software is installed and extensive calibration and testing ensures all parts function as designed together in the system.
Customization and Configuration
Systems are customized per order - floor or ceiling mounted, digital or computed radiography, room design beyond the unit itself. Configurations optimize work flows for each customer's needs.
Quality Assurance Testing
Rigorous testing checks all system functions meet engineering and industry standards. This includes imaging performance, radiation outputs and safety features. Only fully functioning units pass quality assurance.
Packaging and Shipping
Systems are crated protecting all components for shipment. Documentation includes operator manuals, preventative maintenance guides and any special installation instructions.
On-site Installation and Training
Technicians install the system, set up any furniture or room modifications, and train staff on safe and efficient use of the new equipment. On-going support is also provided.
Innovation in X-ray Technology
Continued improvements are expanding the clinical capabilities of x-ray equipment:
Iterative Reconstruction
Advanced algorithms reduce noise and artefacts, enabling lower dose scans. Deep learning methods now enable very low dose chest exams equivalent to a routine 4 view study.
Dual Energy Imaging
By acquiring images at two different x-ray energy spectra, dual energy provides material decomposition and novel applications like virtual non-contrast exams.
CBCT and Tomosynthesis
Cone beam CT and tomosynthesis create 3D and quasi-3D images from a 2D detector, improving detection, guidance and monitoring of treatment response.
DR and Mobile C-arms
The move to all digital flat panel detectors allows high quality mobile exams at the bedside or in surgical/trauma situations previously requiring analog imaging.
Emerging Technologies
On the horizon are spectral CT to further enhance material differentiation, compressed sensing approaches to ultra-low dose CT, and quantum dot imagers promising improved detection efficiency over current technologies.
As a key healthcare technology, investment in x-ray machine manufacturing supports advanced clinical applications and improved patient outcomes. While the basic principles remain the same after over a century, continuous engineering innovation keeps the modality at the forefront of diagnostic medicine and interventional procedures. The future remains bright as each new generation of x-ray systems brings greater capabilities to providers and patients alike.
Get More Insights On X-Ray Machine Manufacturing
- Art
- Causes
- Crafts
- Dance
- Drinks
- Film
- Fitness
- Food
- Jocuri
- Gardening
- Health
- Home
- Literature
- Music
- Networking
- Alte
- Party
- Religion
- Shopping
- Sports
- Theater
- Wellness
- IT, Cloud, Software and Technology