Automotive Wiring Harness: The Key Component Behind Your Car's Functions
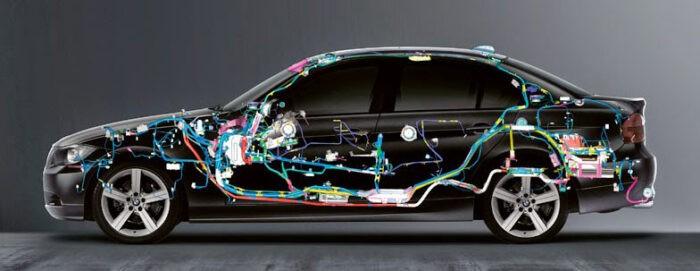
The automotive wiring harness plays a crucial role in the proper functioning of a vehicle. Often unseen but vital, the wiring harness distributes power and signals throughout the vehicle, connecting dozens of electronic control units and components.
What is an Automotive Wiring Harness?
An Automotive Wiring Harness is a pre-assembled group of cables or wires that transmit signals or power throughout a vehicle. Modern cars have wiring harnesses containing tens of meters of wires and cables bundled together. These wiring looms distribute power from the battery to components like the engine control module, lights, infotainment system, and more. They also transmit control signals between sensors, actuators, and electronic control units to operate features like power windows, central locking, ABS, and many others.
Components of a Wiring Harness
A typical automotive wiring harness contains the following main components:
- Cables or wires made of copper or aluminum to transmit power or data signals.Specialized cables are used for applications requiring high currents or noise immunity.
- Connectors to join cables together or connect to components.Common connector types include bullet, blade, and modular connectors.
- Grommets to protect wiring bundles from chafing as they pass through body panels.
- Ties, tapes and clips to bundle and organize cables into manageable groups.
- Shieldingmay be applied to noise-sensitive wires to protect against electromagnetic interference.
- Labelling for identification and traceability during installation and troubleshooting.
Harness Design Challenges
Designing automotive wiring harnesses is complex due to various technical and operability challenges:
- Space constraints under vehicle requiring optimal cable routing and packaging.
- Durability against vibration, impacts and extremes of hot/cold temperatures.
- Noise immunity of data and signal cables carrying sensitive information.
- Managing high amperage spikes from starter motors, wiper motors etc.
- Ease of repair/replacement and removability for access during maintenance.
- Lifecycle requirements exceeding vehicle lifespan through several component replacements.
- Operability challenges like sun load, moisture ingress, chaffing, corrosion resistance.
- Cost optimization through modular and standardized designs across vehicle ranges.
Harness Manufacturing Process
The production of modern automotive wiring harnesses is an involved process requiring resources, planning and precision:
1. Design and Validation: Engineers design optimal layout, routing and cable specs through CAD tools. Prototypes are fabricated and tested for validation.
2. Material procurement: Raw materials like specific grades of copper/aluminum wires and required connectors are procured in bulk.
3. Pre-assembly: Wires are cut, stripped and terminated/crimped to connectors using automated machinery. Shielding may be applied.
4. Bundling and organization: Wires are grouped, bundled, clipped and tied together manually or by robots according to the design.
5. Installation and layout validation: The full harness is installed on a rig and its fit, routing and functionality is tested before sign-off.
6. Testing: Completed harnesses undergo electrical, mechanical and environmental testing to ensure reliability and compliance.
7. Packaging and delivery: Harnesses are packaged safely for delivery to the automaker or integrated into vehicle assembly lines.
Innovations in Harness Technology
As electric vehicles and advance driver assistance systems drive new innovations, car wiring is evolving to meet evolving needs:
- Use of lighter yet high integrity materials like aluminum/composite cables and connectors.
- Advanced EMI shielding techniques for high bandwidth connectivity and signal integrity.
- Integrated circuit boards and modules replacing discrete cables for certain functions to optimize space and weight.
- Multifunctional wiring integrating data, power and even fluid transfer capabilities.
- Self-diagnostic wiring able to detect faults without manual inspection.
- Securely transmitting over-the-air software updates through advanced vehicle networks.
- Move to more standardized interfaces and fewer bespoke designs for economies of scale.
- Advanced condition monitoring systems to continuously check harness health and predict failures.
The automotive wiring harness is a critical but often overlooked system within a vehicle. Advancing rapidly in line with new vehicle technologies, harnesses remain mission-critical in enabling safe and reliable vehicle operation through optimal power and data distribution. With increased electrification and automation, wiring systems will continue evolving to deliver higher performance within stringent size, weight and cost constraints.
Get more insights on this topic: Automotive Wiring Harness
- Art
- Causes
- Crafts
- Dance
- Drinks
- Film
- Fitness
- Food
- Games
- Gardening
- Health
- Home
- Literature
- Music
- Networking
- Other
- Party
- Religion
- Shopping
- Sports
- Theater
- Wellness
- IT, Cloud, Software and Technology