Train Seat Materials: How Interior Design Impacts Passenger Comfort
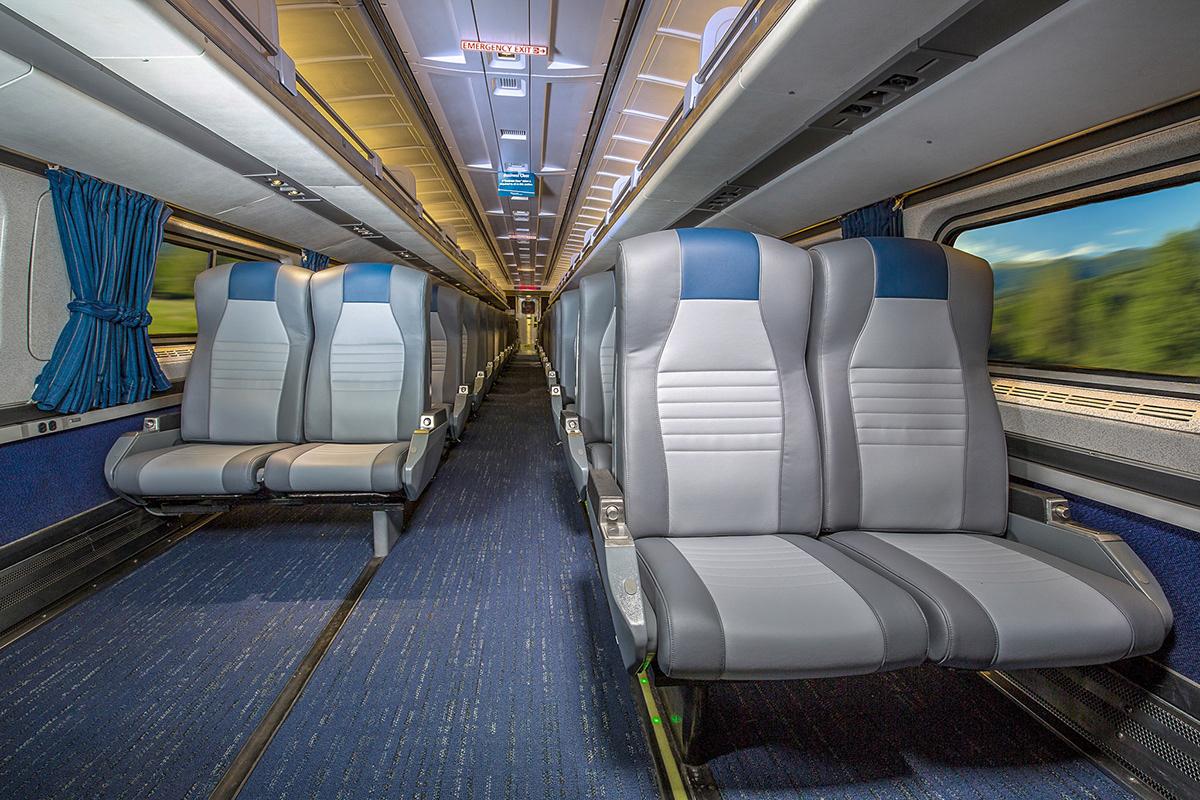
Travelling by train has been a preferred mode of transportation for many due to its convenience and comfort. However, the materials used for train seats play a crucial role in enhancing or hindering the passenger experience. This article examines the various materials commonly used for train seats and how their properties impact issues like comfort, safety, durability and maintenance.
Fabrics
Fabrics remain one of the most widely used materials for train seat covers due to their ability to provide cushioning and comfort. Some of the commonly used fabrics include:
Vinyl: Vinyl fabrics are very durable and easy to clean which makes them suitable for high traffic train environments. However, they are not breathable and can cause passengers to feel hot and sweaty during long journeys.
Leather: Genuine leather provides excellent durability but requires more maintenance compared to synthetic materials. Faux leather offers a cheaper alternative that provides equal durability. However, both leather and faux leather are not breathable.
Woven fabrics: Materials like cotton, polyester and linen blends provide breathability and are softer on the skin. However, they stain and wear out more quickly when exposed to sunlight, food/drink spills etc. Regular washing is required to maintain hygiene.
Microfiber: Dense microfiber fabrics are stain resistant, breathable and quick drying. They are a popular choice for many trains due to their durability and ability to withstand high traffic conditions.
Plastics and Composites
Plastics and engineered composites are also commonly used for train seat construction and components due to their strength, durability and lightweight properties:
Polycarbonate: Durable and impact resistant polycarbonate is used for seatbacks on many trains. It is lightweight, easy to form into complex 3D shapes and maintains structural integrity in the event of a collision.
Fiberglass: Fiberglass reinforced plastic composites provide durability and corrosion resistance at a lower cost compared to metals. They are used extensively for seat frames, panels and exterior train body parts.
Polyethylene (PE): Low density PE plastics are used for lightweight seat components like armrests, cup holders etc. They can be easily molded into complex shapes.
Thermoplastics: Various thermoplastics like acrylonitrile butadiene styrene (ABS) and polypropylene (PP) are preferred for interior fittings and components due to their flexibility in production.
Metals
Stainless steel and aluminum alloys continue to be important materials for train interiors due to their strength, recyclability and corrosion resistance:
Stainless steel: Grades 304 and 316 stainless steel offer high strength with excellent corrosion resistance ideal for structural components and fittings in heavily used train interiors. However, it is costly.
Aluminum: Aluminum alloys like 6061-T6 provide lightweight strength and rigidity at a lower cost compared to steel. Aluminum interior fittings and panels are widely used. Various surface treatments ensure durability and easy cleaning.
Titanium: Titanium and its alloys are increasingly used for seat frames, passenger doors and other critical components demanding strength and lightweight properties. However, high material cost remains a barrier for widespread use.
Selection Factors
Train operators must carefully evaluate multiple factors when selecting Seat Materials to fulfill performance, passenger comfort and budget requirements:
Durability: Materials able to withstand years of heavy use with minimum wear require low maintenance and avoid premature replacement costs.
Comfort: Breathability, temperature regulation, softness are important for long distance travel comfort.
Hygiene: Easy to clean non-porous surfaces help maintain hygiene in high traffic confined train interiors.
Safety: Seats made from flame retardant, impact resistant materials provide protection during collisions.
Sustainability: Use of recycled/recyclable materials supports green initiatives.
Cost: Initial material and production costs balanced against long-term usage, maintenance & replacement expenses.
Aesthetics: Pleasant appearance and finish that enhances the onboard experience.
The right choice of seat materials backed by proper design, maintenance and passenger feedback helps optimize the train travel experience. Ongoing research continues to yield newer technologies meeting the diverse and evolving needs of transportation systems worldwide.
Conclusion
Selection of appropriate train seat materials impacts critical issues of passenger comfort, hygiene and safety. While plastics, composites and lightweight metals offer benefits of durability, modern fabrics enhance seating comfort on long journeys. Train operators must carefully evaluate short-term costs against long-term performance requirements to deliver an optimal travelling experience through material choices. Continuous innovation is further improving sustainability and passenger wellness.
Get More Insights On Train Seat Materials
- Art
- Causes
- Crafts
- Dance
- Drinks
- Film
- Fitness
- Food
- الألعاب
- Gardening
- Health
- الرئيسية
- Literature
- Music
- Networking
- أخرى
- Party
- Religion
- Shopping
- Sports
- Theater
- Wellness
- IT, Cloud, Software and Technology