Polyamide 12: A Versatile and Sustainable Engineering Plastic
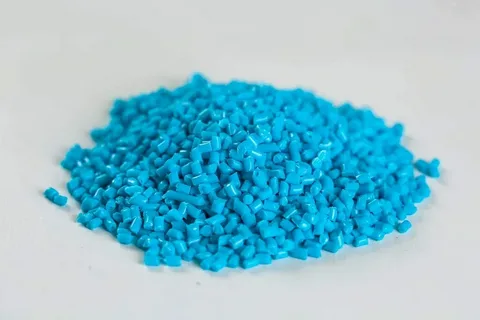
Polyamide 12, commonly known as nylon 12, is a semi-crystalline thermoplastic that offers a unique balance of properties making it well-suited for numerous industrial applications. With its combination of strength, toughness, chemical resistance and ease of processing, polyamide 12 has gained widespread adoption across many sectors including automotive, electronics, and oil and gas. This article explores the characteristics, production process and uses of this versatile engineering plastic.
Chemical Structure and Properties
Polyamide 12 belongs to the nylon family of polymers which are synthesized through step-growth polymerization of ω-amino acids and ω-aminocarboxylic acids. Its monomer is lauryl lactam which consists of a twelve-carbon alkyl group connected to a lactam ring. This linear alkyl structure gives polyamide 12 its distinct semi-crystalline morphology and mechanical behavior.
Some key properties of polyamide 12 include:
- Tensile strength of around 55 MPa and elastic modulus of 1.2 GPa, providing good load-bearing capabilities.
- Impact resistance superior to other nylons like nylon 6 or nylon 6,6 owing to its flexible alkyl chains.
- Melting point between 173-178°C allowing for ease of processing through techniques like injection molding.
- Chemical resistance to oils, greases, dilute acids and alkalis up to 90°C. This resistance can be further enhanced with additives.
- Low moisture absorption of only 1-2% compared to other nylons, imparting dimensional stability.
Production Process
Polyamide 12 is commercially synthesized through a continuous process called polycondensation. In this process, lauryl lactam monomer undergoes ring-opening polymerization in the presence of a catalyst like 12-aminododecanoic acid at temperatures between 180-230°C and pressures of 1-5 bar.
The polymer melt produced is then extruded and quenched to obtain polyamide 12 pellets or granules. These pellets can be directly used for subsequent molding or fabrication applications. Additives may also be incorporated during production to impart color, enhance mechanical properties or provide UV resistance.
Subheading
Uses of Polyamide 12
Automotive Applications
Due to its heat resistance, toughness and strength-to-weight ratio, polyamide 12 sees extensive use in the automotive industry. It is used to produce structural components in the engine bay along with clips, inserts, gears and pulleys. Polyamide 12 composites reinforced with glass fibers are utilized for under-hood components like intake manifolds. The plastic also finds application in exterior trim pieces, fasteners and electrical components owing to its electrical insulation abilities.
Electronics Applications
Properties like low moisture absorption and dimensional stability make polyamide 12 suitable for use in electronic devices and connectors. It is employed as an insulator in electronic circuit boards and components. Polyamide 12 tapes offer protective and insulating functions in electronics packaging applications. The plastic's flame retardant grades meet stringent standards for components in appliances, telecom hardware, computers and power tools.
Oil and Gas Applications
Good chemical resistance and mechanical properties allow polyamide 12 to be deployed extensively in the oil and gas industry. It is used to create high-pressure hoses, pipes, valves and seals that withstand exposure to hydrocarbon fluids at high temperatures. Filter cartridges, gaskets and pipe fittings fabricated from polyamide 12 effectively serve extraction, refining and transportation operations.
Other Uses
Some other applications of polyamide 12 include seals and gaskets in industrial machinery due to its fatigue and wear resistance. Its toughness and processability make it suitable for sports equipment manufacturing. Polyamide 12 found increasing adoption in 3D printing applications because of its printability on fused deposition modeling (FDM) systems. The plastic also has usage in apparel, tubing, machinery components and medical devices.
Sustainability Attributes
Being largely derived from sustainable castor oil, polyamide 12 has eco-friendly production and end-of-life characteristics compared to conventional plastics. Almost 100% of the material can potentially be recycled. Its recyclability has been demonstrated at manufacturing plants to produce new polyamide 12 products with minimal loss in properties. The plastic also biodegrades faster than petrochemical plastics if released into the environment. Polyamide 12 thus provides an environmentally preferable alternative to other engineering thermoplastics in suitable applications.
Conclusion
This article discussed the chemistry, production, properties and applications of the thermoplastic polymer polyamide 12. The unique combination of strength, toughness, heat resistance and chemical tolerance offered by the material have led to its widespread utilization in automotive, electronics, oil and gas industries and more. Coupled with sustainability advantages, polyamide 12 looks poised to see increasing adoption among engineers and product designers looking for alternative solutions. Its versatile characteristics make it a preferred choice for a variety applications requiring performance and durability.
Get more insights on: https://www.ukwebwire.com/polyamide-12-growth-and-trends/
- Art
- Causes
- Crafts
- Dance
- Drinks
- Film
- Fitness
- Food
- Spiele
- Gardening
- Health
- Startseite
- Literature
- Music
- Networking
- Andere
- Party
- Religion
- Shopping
- Sports
- Theater
- Wellness
- IT, Cloud, Software and Technology