Polyphenylene Sulfide: A Versatile Engineering Thermoplastic
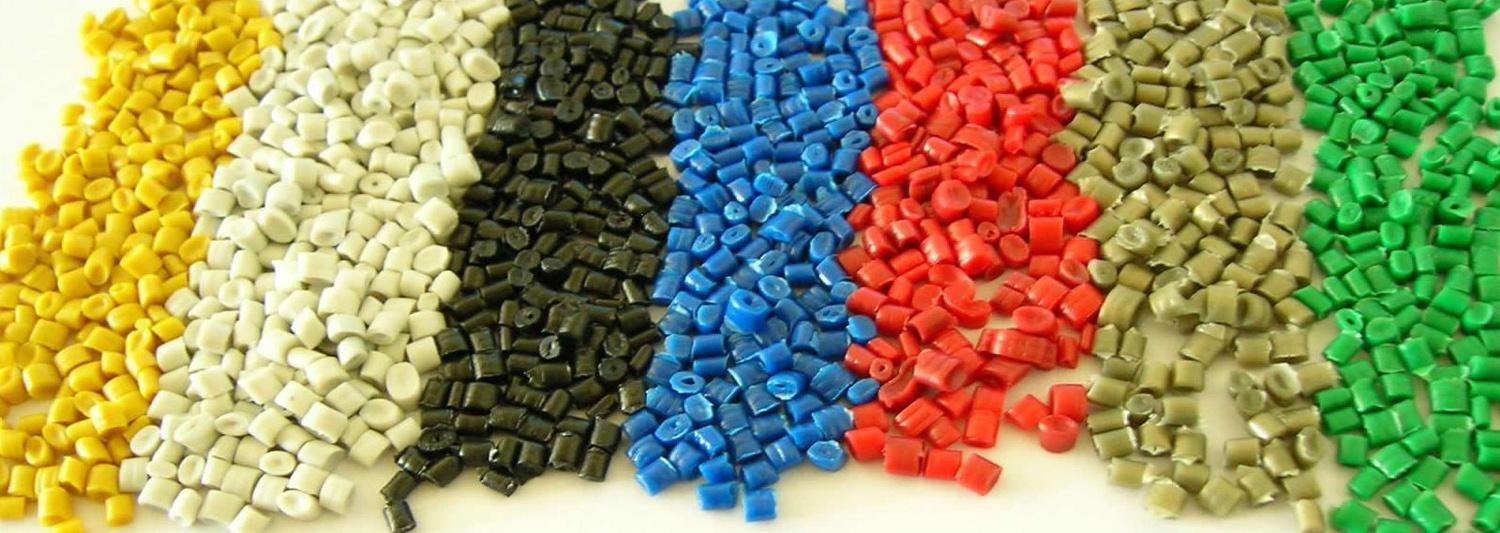
Introduction
Polyphenylene sulfide, commonly known as PPS, is a semi-crystalline thermoplastic polymer with excellent chemical and heat resistance properties. It was first developed in the late 1960s as an alternative to nylon in high-temperature applications. Since then, PPS has found widespread use across many industries due to its versatile material properties. This article provides an in-depth look at PPS, its properties, manufacturing process, applications, and future potential.
Chemical Structure and Properties
PPS is composed of aromatic rings linked with sulfide groups. This basic molecular structure gives PPS its unique blend of properties. It has excellent resistance to chemicals, solvents, and weathering. PPS retains its strength and stiffness even at high temperatures up to 260°C. It also has superior dimensional stability and low moisture absorption. PPS is self-extinguishing with a UL 94 V-0 flame rating. It offers high flowability for injection and compression molding while retaining dimensional accuracy in the final parts. These robust material properties make PPS suitable for demanding applications in automotive, electronics, aerospace and other industries.
Manufacturing Process
PPS is manufactured through a step-growth polycondensation reaction between p-dichlorobenzene and sodium sulfide. The reaction takes place in a solvent like N-methylpyrrolidone (NMP) under high temperature and pressure. This polymerization process yields PPS with high molecular weight. After polymerization, the solvent is removed leaving behind solid pellets or flakes of PPS resin. The PPS resin can then be processed using various molding techniques like injection molding, extrusion, and compression molding to create finished parts and products. Common molding grades of PPS have melting points between 280-290°C, making them easy to process into complex shapes without degradation.
Automotive Applications
In the automotive industry, PPS finds wide usage in under-the-hood applications requiring heat and chemical resistance. PPS parts are commonly found in engine components like manifold runners, charge air ducts, fuel system parts and turbochargers. Its high heat deflection temperature allows PPS parts to withstand continuous heat exposure near the engine without deformation. PPS is also gaining popularity for exterior automotive applications due to its UV resistance, impact strength and dimensional stability over a wide temperature range. Some exterior PPS parts include mirror housings, lamp housings, radiator grills and air intake manifolds. In electric vehicles, PPS is used to make parts for motor windings, battery casings, and cables due to its ability to operate efficiently at high temperatures generated within.
Electronics Applications
In the electronics industry, PPS meets critical requirements for electrical insulators, connectors and housings. Its excellent dielectric properties, high operating temperatures and flame retardancy make PPS well-suited for electronics applications. Some common uses of PPS in electronics include electric/electronic component housings, connectors, wire terminals and sockets. PPS insulators are used in transformers, switchgears and electrical panels. Mobile device and laptop housings increasingly use PPS parts due to their thin wall design capabilities and ability to withstand surface abrasion and impact. PPS cable wrappers provide protection and insulation while ensuring electrical efficiency even under extreme conditions. With 5G technology driving demands for higher frequencies and power levels, PPS is poised to grow in electronics insulation applications.
Medical Applications
The biocompatibility, heat resistance and strength of PPS have led to increasing use of the material in medical devices and equipment. PPS tubing finds application in providing extra durability to devices like dialysis machines, infusion pumps and heart-lung bypass equipment. Due to being autoclavable, PPS is also used to make trays, containers and packaging for sterilized medical instruments. As a bearing material resistant to wear and degradation from body fluids, PPS is emerging as a replacement for metals in articulating joints of implants. Other medical uses of PPS include components for MRI and CT scanners, sterilizers, surgical tools and endoscopy devices. As healthcare moves more towards home-based care, PPS material promises lower infection risks and greater reliability for medical devices used outside hospitals.
Future Outlook
Going forward, Polyphenylene Sulfide (PPS) will continue gaining importance as an engineering plastic in niche markets requiring superior heat and chemical resistance compared to traditional plastics. New filler compound technologies are enhancing the strength, stiffness and impact properties of PPS. Continuous fiber reinforced PPS composites will enable lighter weight designs in transportation and aerospace. PPS surface functionalization will foster innovative biomaterial applications. Emerging technologies in 5G communication, electric vehicles, renewable energy offer huge prospects for PPS parts. Overall, the unique blend of high performance characteristics at an affordable price point has ensured PPS a bright future as a versatile specialty thermoplastic.
Get more insights, On Polyphenylene Sulfide (PPS)
- Art
- Causes
- Crafts
- Dance
- Drinks
- Film
- Fitness
- Food
- Spellen
- Gardening
- Health
- Home
- Literature
- Music
- Networking
- Other
- Party
- Religion
- Shopping
- Sports
- Theater
- Wellness
- IT, Cloud, Software and Technology