PET Preforms: The Building Blocks of Plastic Bottles
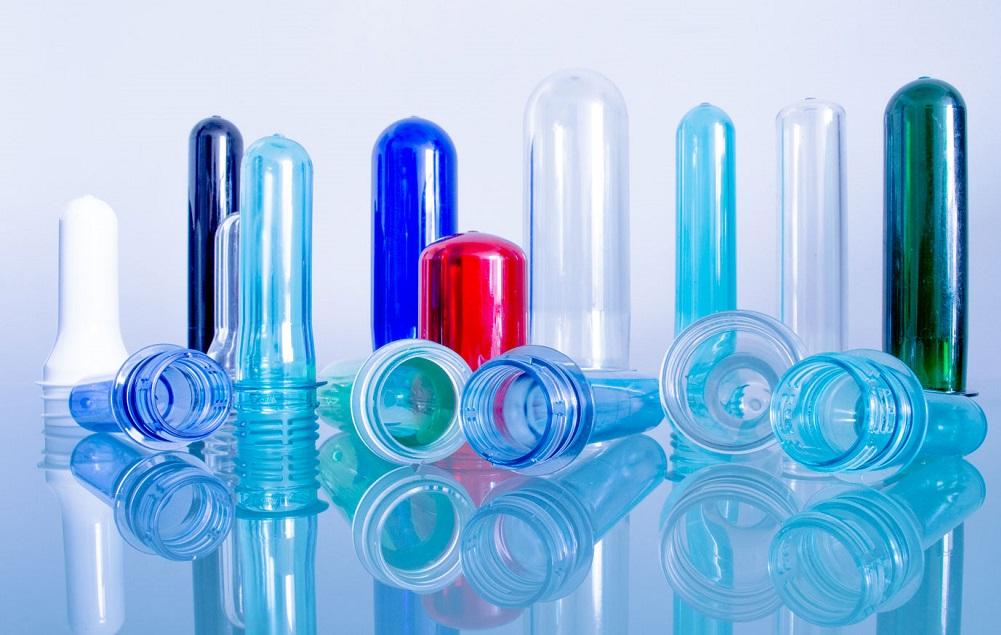
PET preforms are the small plastic structures that eventually become plastic water bottles and soda bottles after undergoing further processing. Despite their small size, preforms play a crucial role in the plastics manufacturing process and have undergone tremendous innovation over recent decades.
What are PET Preforms?
PET (Polyethylene Terephthalate) preforms are cylindrical plastic structures typically ranging from 2-5 inches in height and 1-2 inches in diameter. They are produced using injection molding from PET resin pellets. The preform walls are thick but contain an opening at one end where the bottle opening will eventually form.
While appearing quite simplistic in design, preforms contain the blueprint for transforming into a full plastic bottle. The thickness, shape and size variation along the PET Preforms carefully orchestrates the subsequent blow molding process into forming an efficient yet durable plastic container. Without preforms, plastic bottles could not be produced on a mass scale as required to meet modern demand.
Injection Molding of Preforms
The injection molding of preforms is a precise and carefully regulated process. PET resin pellets are melted down and injected into steel molds under high pressure. Different mold cavities can simultaneously produce multiple preforms during each cycle. The molten plastic cools and sets within a few seconds to form the desired semi-solid preform shape.
Quality control during injection molding is critical, as any defects at the preform stage become amplified when blown into bottle form. Variables like temperature, pressure, cycle times and material purity are closely monitored. Advanced monitoring systems can detect subtle changes that may impact preform quality. State-of-the-art molds also minimize waste and scrapage.
- Modifying Preforms; Barrier Technologies; Color and Additives
Modifying Preforms
Advancements in preform design have enabled major modifications over the years. Early preforms were quite basic but innovations have added new functionalities. Some preforms now contain threading to allow caps or triggers. Micro-cavities can be molded to seed nucleation sites for optimal stretching. Special channels or vents are integrated for pressure control during blowing.
Submicron layers can be co-injected or laminated into preforms for enhanced properties. Barrier technologies like ethylene vinyl alcohol (EVOH) or polyvinylidene chloride (PVDC) inhibit gas/liquid migration when used as an oxygen barrier layer. Such modified preforms have expanded PET applications into demanding packaging like hotfill containers.
Color and Additives
Preforms can be produced in a wide range of transparent and opaque colors to suit various product and brand needs. Colorants are either added directly into the PET resin or through an on-line conveying system prior to injection molding. Special effects like metallic appearances or color stabilization for recycling can also be achieved.
Functional additives are commonly included in preforms. UV stabilizers protect contents from light degradation. Nucleating agents precisely control crystallization during blowing. Antioxidants maintain structural integrity over long shelf lives. Slip additives reduce friction for easy reclosing. All additives are food contact compliant and do not migrate out of finished packaging.
- Blow Molding Process; Inspection and Quality Control
Blow Molding Process
During blow molding, preforms are heated, stretched and inflated to form full bottles. A preform is clamped open-end down in a split mold. Air is then injected through the preform base to expand it against the mold inner surface. As the hot plastic contacts the cooler mold, it quickly hardens into the final bottle shape.
A successful blow results in a container replicating precise dimensional accuracy, thickness distribution and strength required for stacking, filling, capping and distribution. The orientation of plastic chains during stretching also markedly enhances mechanical properties like impact resistance. An efficient single-step blow molding cycle can produce hundreds of bottles per minute on automated lines.
Inspection and Quality Control
Quality control does not end after preforms emerge from injection molds. State-of-the-art inspection stations utilize techniques like hyperspectral imaging, 3D laser profiling, RFID tracking and mass flow monitoring to screen for defects both invisible to the naked eye.
Preforms are checked for dimensional accuracy, structural flaws, contaminant particles, imperfections from molding, inadequate material distribution and more. Failed units are rejected while automated records trace back to corrective actions. Blowing simulations also validate preform design before large-scale production.
On-line NIR machines rapidly analyze chemical content and properties. Sample bottles produced are destructively tested for strength, leakage and shelf-life under accelerated aging. Statistical Process Control ensures consistent quality over the product lifetime. Together, strict quality systems produce preforms that meeting packaging needs with high reliability.
- Advancing Sustainability; Future of PET Preforms
Advancing Sustainability
As sustainability concerns grow worldwide, preform manufacturers are rising to the challenge. Efforts span optimizing material usage, designing for recycling, incorporating recycled content and reducing energy usage.
Preform weights have progressively lowered through engineering innovations while maintaining performance. Plant modernizations have transitioned many injection molding machines from hydraulic to more efficient all-electric models. Investments in waste heat recovery further cut carbon footprint.
PET preforms are now widely recycled to yield food-grade recycled PET (rPET) resins. Preform designs facilitate effective sorting and ensure rPET preforms perform at par. Some cutting-edge versions even incorporate up to 100% rPET. Such circular systems hold potential to radically reduce plastics' dependency on virgin fossil feedstock.
Future of PET Preforms
With constant marketplace demands, the evolution of PET preforms continues unabated. Future growth areas might include tailored barrier properties for new application frontiers, integration of bio-based PET, smart packaging functionality and novel recycling solutions. Digitalization and automation advances will optimize production hassle-free.
3D printing holds promise to disrupt preform making through customized complex geometries on-demand without molds. Antimicrobial properties may be tuned in to keep packaged items fresher. As packaging requirements progress in step with technological and social changes, expect PET preforms at the forefront of delivering sustainable packaging solutions for the coming decades.
Get more insights on this topic: PET Preforms
- Art
- Causes
- Crafts
- Dance
- Drinks
- Film
- Fitness
- Food
- Spellen
- Gardening
- Health
- Home
- Literature
- Music
- Networking
- Other
- Party
- Religion
- Shopping
- Sports
- Theater
- Wellness
- IT, Cloud, Software and Technology