Packaging Testing: Ensuring Safety and Quality
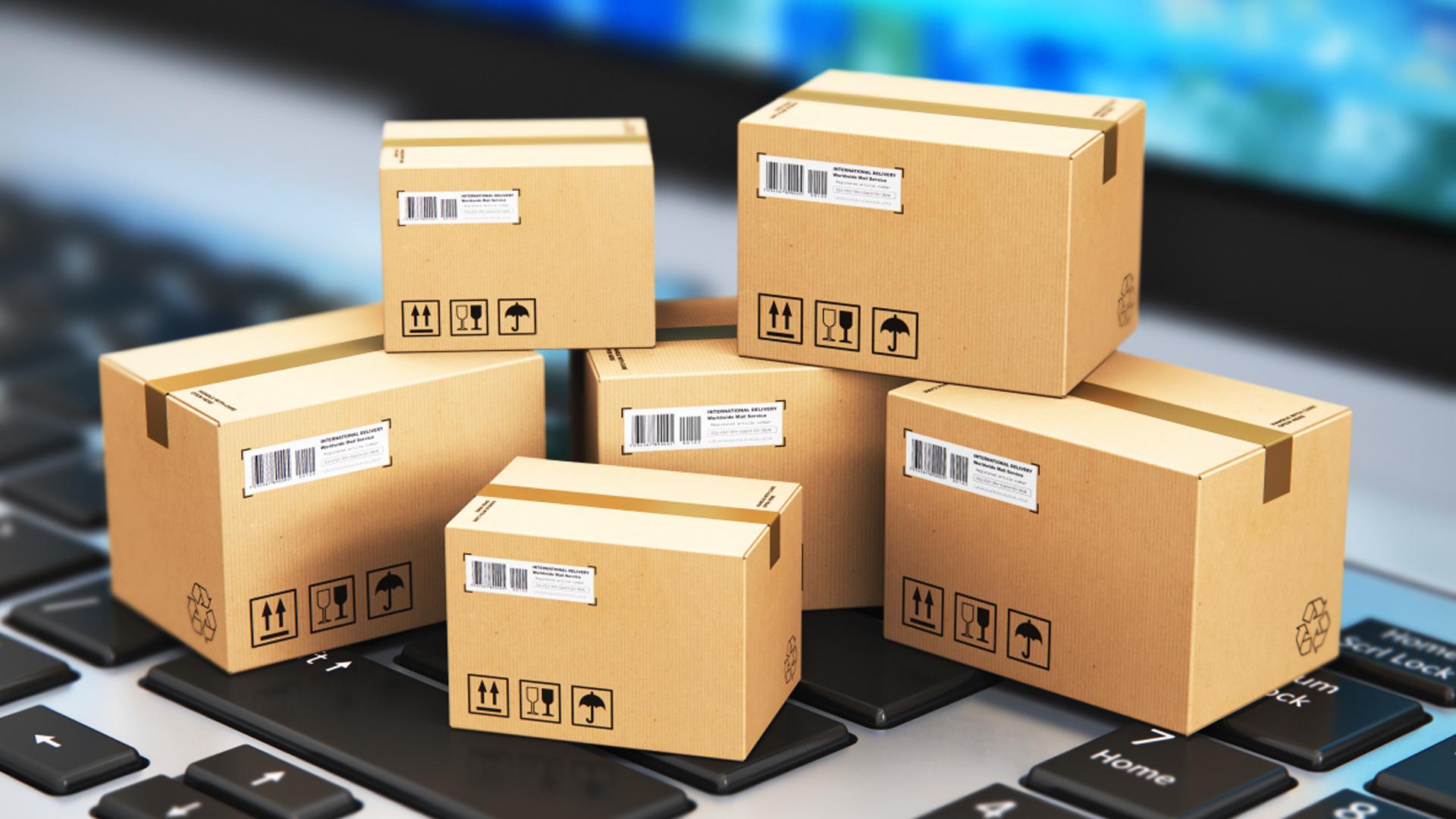
Packaging plays a vital role in product delivery and consumer experience. Proper packaging protects products from damage during transportation and prevents contamination. However, to ensure packaging effectiveness, different testing methods are required at various stages of development and production.
Design Validation Testing
Several tests are conducted during the packaging design stage to validate the concept. This stage examines if the proposed design will withstand intended product uses and distribution cycles.
Packaging Compatibility
One of the initial tests evaluates Packaging Testing Market material compatibility with the product and potential threats. Tests check for material stability when exposed to product attributes like moisture, chemicals, thermal effects etc. This identifies materials that can react or degrade when in contact with the product over time.
Quality Assurance Testing
Even after product launch, periodic packaging quality audits involve sampling from production and distribution. Common tests include shelf-life trials, seal integrity checks and finished package inspection. This ensures maintaining consistent quality standards over commercial production. Any potential issues are addressed proactively.
Rigorous packaging testing at design and production stages forms the backbone of an effective quality assurance program. While testing requires substantial investments, it plays a vital role in validating safety and preventing product losses resulting from packaging failures. A well-designed testing protocol incorporating the above key areas ensures packaging fulfills its critical purpose of protecting products through distribution cycles and provides optimal consumer experience.
Get more insights on Packaging Testing Market
- Art
- Causes
- Crafts
- Dance
- Drinks
- Film
- Fitness
- Food
- Jocuri
- Gardening
- Health
- Home
- Literature
- Music
- Networking
- Alte
- Party
- Religion
- Shopping
- Sports
- Theater
- Wellness
- IT, Cloud, Software and Technology