Cold Heading Machine: An Integral Part of Metal Forming Industry
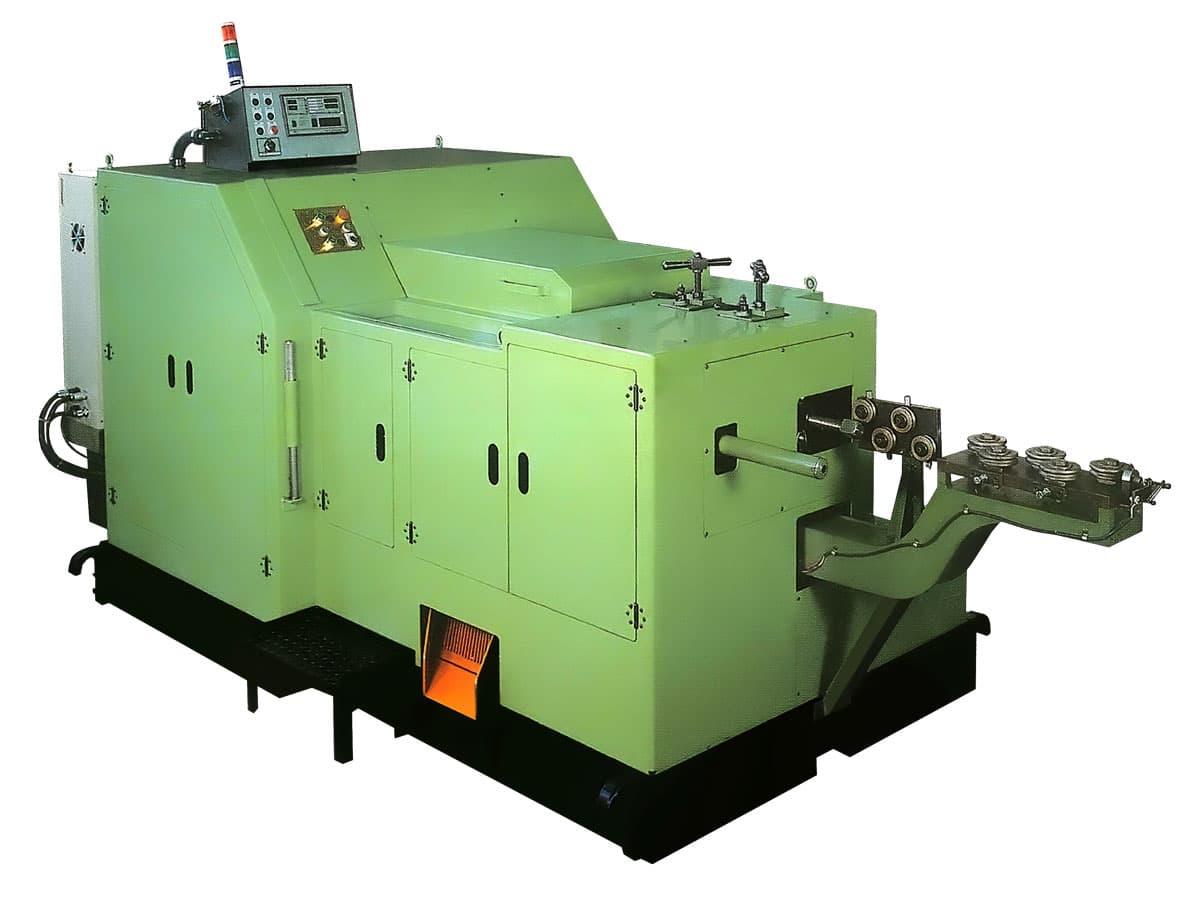
Cold heading is a metal forming process used to accurately shape metal parts by applying compressive forces at room temperature. It involves pushing or pressing metal blank or rod with a punch and die to create complex shapes that cannot be made by other forming processes like casting or machining. To perform this cold heading process, a specialized machine called a 'cold heading machine' is used. In this article, we will discuss what a cold heading machine is, its working, types, applications and importance in metal forming industry.
Working of a Cold Heading Machine
A cold heading machine consists of a hydraulically or mechanically driven ram that forces a punch into a close-fitting die cavity. Hydraulic or motor power moves the ram to exert forces on the punch to shape the metal. Lowering the ram and punch into the die forces the metal into the desired shape in the cavity. The punch and die are made of hard materials like tool steel to withstand high pressures without deforming.
The metal blank or rod is fed automatically into the die cavity before each heading cycle. Once the shaping is done, the ram pulls out along with the punch, ejecting the formed part. Lubricants are applied to reduce friction between the punch, die and metal during the heading process. This cycle repeats automatically to produce parts in large volumes.
Types of Cold Heading Machine
There are mainly three types of cold heading machines based on production capacity and application:
- Small cold header - Used for low volume production. Suitable for shops and job shops. Can form 5,000-20,000 pieces per hour.
- Medium cold header - For medium volume production of 50,000-150,000 pieces per hour. Used in dedicated heading operations.
- Large cold header - Heavy-duty machines for high volume mass production of more than 150,000 pieces per hour. Used by large OEMs and tier suppliers.
Applications of Cold Heading
Cold heading is widely used to manufacture small metal parts that have intricate shapes and tight tolerances. Some common applications where cold heading process and machines are utilized include:
- Automotive fasteners like bolts, nuts, screws, pins etc.
- Electrical and electronics components like contacts, terminals, connectors.
- Appliance parts like washers, springs.
- Bicycle and motorcycle parts.
- Tool components like punches, dress, taps.
- Medical device components.
Importance of Cold Heading in Metal Forming
Cold heading plays a vital role in mass producing intricate metal components used across many industries. Here are some key advantages of cold heading process and machines:
1. Precision and Accuracy
Cold heading allows creating complex internal and external geometries within very tight tolerances of ±0.025mm. This precision is difficult to achieve with other forming methods.
2. Repeatability
Being a closed-die process, cold heading offers excellent repeatability in part dimensions. Close tolerances are consistently maintained with thousands of pieces.
3. Material Savings
Cold heading is a net-shape process requiring little or no additional machining. This significantly reduces raw material wastage compared to casting or machining from billet.
4. Automation Compatible
Cold heading machines are designed for automatic feeding, forming and ejection cycles. This allows for highly automated, high volume production to lower manufacturing costs.
5. Applicable to Variety of Metals
The cold working process can form numerous metal alloys like steel, stainless steel, copper and aluminum alloys into intricate shapes.
6. Hardening Effect
The compressive forces applied during cold heading work-hardens metals, improving their strength. This eliminates the need for additional hardening processes.
7. Economical Tooling
Compared to other precision processes, cold heading needs relatively simple and lower cost dies that have long production runs before replacement.
cold heading is a vital net-shape metal forming technique offering precision, repeatability and automation compatibility for mass production. Application of advanced cold heading machines has enabled manufacturing complex small metallic components used across industries in a highly productive and cost-effective manner. Their importance in meeting the growing demand of miniature, high-strength fasteners and metallic components continues to rise in the metal forming industry.
Get More Insights On This Topic: Cold Heading Machine
- Art
- Causes
- Crafts
- Dance
- Drinks
- Film
- Fitness
- Food
- Games
- Gardening
- Health
- Home
- Literature
- Music
- Networking
- Other
- Party
- Religion
- Shopping
- Sports
- Theater
- Wellness
- IT, Cloud, Software and Technology