U.S Plastic-to-Fuel: An Emerging Solution to Plastic Waste Problems in the United States
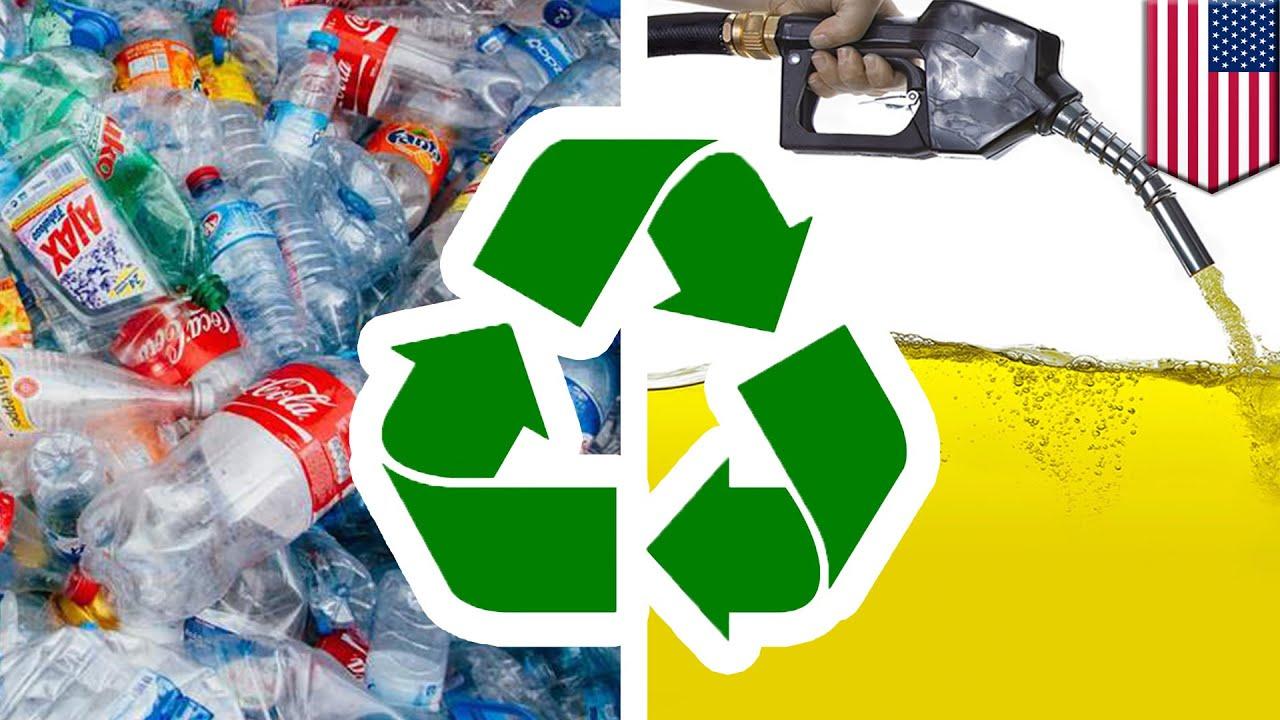
Introduction to Plastic Pollution in the U.S.
Only around 9% of plastics produced have been recycled since the 1970s. Each year, millions of tons of non-recycled plastics end up in U.S. landfills or the natural environment. Limited recycling infrastructure and the high costs of sorting and processing plastics have made recycling an unsustainable solution. As a result, plastic waste presents a growing environmental challenge.
How Plastic Waste is Currently Managed
Currently, the majority of plastic waste in the U.S. is sent to landfills or incineration plants. While landfill burial delays plastic's eventual break down into microplastics, incineration releases carbon dioxide and other emissions into the air. Neither option truly solves the problem of plastic accumulation. Some plastics are exported for recycling overseas, but this international waste trade raises economic and environmental justice issues for receiving nations. It is evident that new plastic waste management strategies are urgently needed.
The Potential of Plastic-to-Fuel Technology
U.S Plastic-to-Fuel technology uses thermal and catalytic processes to convert non-recycled plastics directly into synthetic crude oil, diesel, gasoline, and other energy products. The concept is similar to traditional petroleum refining, where crude oil is broken down then reassembled into fuels. In plastic-to-fuel processing, plastics like polyethylene and polypropylene are heated under oxygen-free or low-oxygen conditions to break chemical bonds and produce hydrocarbon chains and cyclic molecules. Catalysts then restructure these intermediate products into specific fuels.
The process has the potential to divert plastic waste from landfills and generate fuels from materials that currently have little to no economic or environmental value at end of life. Plastics-derived fuels have properties virtually indistinguishable from conventionally produced gasoline, diesel and jet fuel. This compatibility allows produced fuels to be seamlessly integrated into existing transportation fuel infrastructure and vehicles.
Demonstration Projects Emerging Across the U.S.
While plastic-to-fuel technology is still emerging, several companies are launching demonstrations projects across the U.S. Perhaps the largest is Global Renewables' $260 million waste plastic-to-gasoline plant under construction in Pasadena, Texas. Set to open in late 2024, it will process 30,000 tons of plastic annually to produce approximately 10 million gallons of gasoline.
Agilyx, based in Oregon, operates a commercial-scale plant in Tigard processing mixed plastic waste into synthetic crude oil, which is then refined locally into fuels and wax. Their next plant slated for development will have triple current capacity. Kentucky-based Blue Planet also runs demonstrations converting multi-material plastic waste into shipping fuel and naphtha blend stocks. Their recently announced project in Lake Charles, Louisiana will process over 5,000 tons of plastic annually when complete.
Meanwhile, Vadxx Energy in Austin, Texas is developing catalytic pyrolysis technology they claim provides higher oil yields in a smaller footprint. They aim to deliver their first commercial unit by 2025. Additional plastic-to-fuel demonstration projects are in planning or early operation across states like Pennsylvania, Florida, Washington and California as well. This developing infrastructure lays the foundation for wider plastic-to-fuel adoption across the United States.
Economic and Environmental Benefits
Plastic-to-fuel facilities promise numerous economic and environmental advantages over existing plastic management methods. They create local jobs in construction and plant operation. Using plastic waste as a feedstock generates revenue streams from fuel sales to offset high capital and processing costs. Produced fuels can help replace imported oil or enhance domestic energy security.
Importantly, plastic waste is transformed into useful energy sources rather than burdening landfills or incinerators indefinitely. Lifecycle analyses indicate plastic-to-fuel processes significantly reduce fossil CO2 emissions compared to incineration or crude oil refining. Plants also avoid plastic leakage into the environment by permanently integrating plastic molecules into vehicle fuel streams. Over time, a properly scaled national plastic-to-fuel network could process the bulk of non-recycled plastics in the U.S.
Regulatory and Logistical Challenges Remain
Despite the demonstrated benefits of plastic-to-fuel, challenges remain around waste supply, fuel quality acceptance, and regulations that currently prioritize recycling over conversion technologies. Consistent feedstock supply depends on developing plastic sorting, collection, and supply chain systems. Fuel product quality must meet specifications for different engine technologies and markets.
Currently, the U.S. Environmental Protection Agency classifies most plastic waste as non-hazardous solid waste rather than renewable feedstock. This designation fails to recognize conversion applications and hinders large-scale development and use of plastic fuels under the Renewable Fuel Standard program. As the technology progresses, supportive policies are still required to establish plastic-to-fuel as a mainstream waste management solution.
Get More Insights On This Topic: U.S Plastic-to-Fuel
Explore More Related Topic: Engineering Plastics Market
- Art
- Causes
- Crafts
- Dance
- Drinks
- Film
- Fitness
- Food
- Spellen
- Gardening
- Health
- Home
- Literature
- Music
- Networking
- Other
- Party
- Religion
- Shopping
- Sports
- Theater
- Wellness
- IT, Cloud, Software and Technology