Vacuum-Formed Component Manufacturers
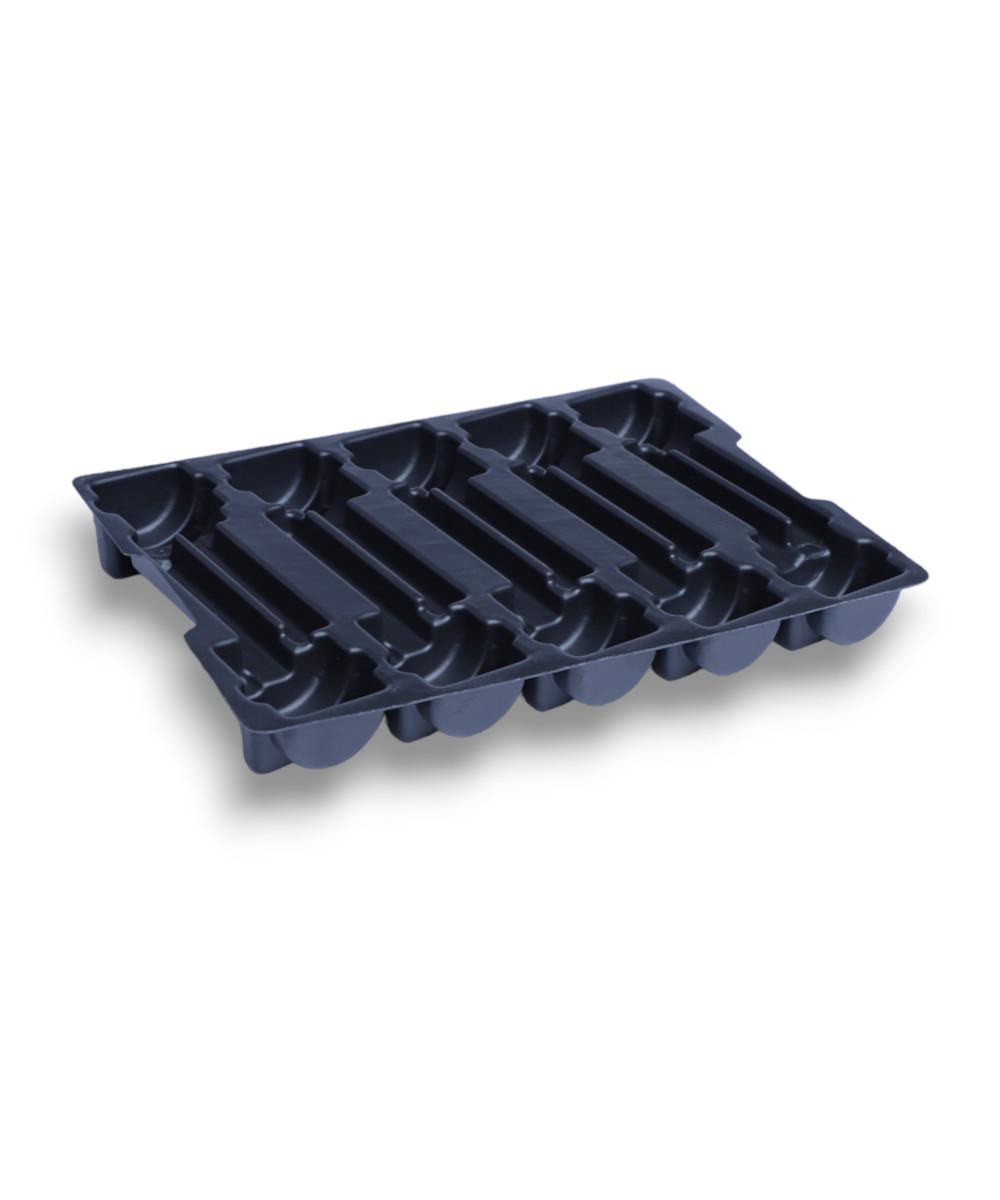
Vacuum Formed Component Manufacturers
Welcome to the world of vacuum formed components, where innovation and versatility collide! Whether you realize it or not, these remarkable creations play a significant role in our daily lives. From the sleek packaging that protects your favourite electronics to the custom trays that cradle medical supplies with precision – vacuum formed components are everywhere!
In this blog post, we will dive deep into the fascinating world of vacuum formed components. We'll explore what they are, their incredible benefits, and how various industries utilize them for their unique applications. So buckle up and get ready to be amazed by the endless possibilities offered by these ingenious manufacturing wonders. Let's jump right in!
What are vacuum formed components?
Vacuum formed components, also known as thermoformed plastics, are an integral part of modern manufacturing processes. The technique involves heating a flat plastic sheet until it becomes pliable and then draping it over a mould using vacuum pressure. As the plastic cools down, it solidifies into the desired shape.
What sets vacuum formed components apart is their ability to be moulded into complex shapes with precise details. This makes them incredibly versatile and suitable for a wide range of applications across various industries. From automotive parts and consumer goods to medical devices and aerospace equipment – vacuum-formed components can be found virtually everywhere.
Moreover, vacuum formed components boast excellent durability while remaining lightweight. This makes them ideal for industries where weight reduction is critical without compromising strength or functionality.
The benefits of vacuum formed components
Vacuum formed components offer numerous benefits that make them a popular choice in various industries. One of the main advantages is their versatility. Vacuum forming allows for the creation of complex shapes and designs, making it possible to produce components with unique contours and intricate details.
Another benefit is cost-effectiveness. Vacuum forming is a relatively low-cost manufacturing process compared to other methods such as injection moulding or CNC machining. This makes it an attractive option for both small-scale production runs and large-volume manufacturing.
In addition to being cost-effective, vacuum-formed components are also lightweight yet durable. The materials used in the vacuum-forming process are typically lighter than traditional materials like metal, which can help reduce overall weight in applications where weight matters, such as automotive or aerospace industries.
The benefits of vacuum-formed components make them a practical choice across various industries seeking cost-effective solutions without compromising on quality or design possibilities
Applications of vacuum formed components in different industries
Vacuum formed components have a wide range of applications across various industries. One industry that greatly benefits from vacuum-formed components is the automotive industry. These components are used to create interior parts such as dashboards, door panels, and console covers. Vacuum forming allows for complex shapes and designs at a lower cost compared to other manufacturing methods.
In the packaging industry, vacuum formed trays and inserts are commonly used to protect delicate or fragile products during transportation. The ability to customize the shape and size of these trays ensures a snug fit for each product, minimizing damage during transit.
The medical field also utilizes vacuum formed components in various ways. For example, custom-made orthotics can be created using this process, providing patients with comfortable and supportive devices that conform perfectly to their bodies. Additionally, dental prosthetics such as mouthguards and aligners can be produced using vacuum forming techniques.
In the electronics industry, vacuum formed plastic enclosures provide protection for sensitive electronic equipment while allowing easy access for maintenance or repairs. These enclosures can be designed with built-in features such as mounting brackets or cable management systems.
The future of vacuum formed components
As we look ahead to the future, it is clear that vacuum formed components will continue to play a vital role in various industries. With advancements in technology and materials, these components are only becoming more versatile and efficient.
One area where we can expect to see significant growth is in the automotive industry. Vacuum-formed components are already widely used for interior parts, such as dashboards and door panels. However, as electric vehicles become more prevalent, there will be an increased demand for lightweight yet durable components. Vacuum forming offers the perfect solution, allowing manufacturers to create complex shapes with ease.
Another sector that will benefit from vacuum formed components is the medical industry. From prosthetics to surgical trays, these components offer cost-effective solutions while maintaining high standards of quality and cleanliness. As medical technologies evolve rapidly, vacuum forming provides a flexible manufacturing process that can quickly adapt to changing needs.
Conclusion
In conclusion the future looks bright for vacuum formed component manufacturers. As technology advances and new possibilities emerge, these companies have a unique opportunity to innovate and provide solutions for countless applications across various industries. Whether it's creating custom packaging or producing intricate parts for aerospace engineering - vacuum-forming has proven itself time and time again as a reliable method of production that shows no signs of slowing down anytime soon!
- Art
- Causes
- Crafts
- Dance
- Drinks
- Film
- Fitness
- Food
- Spellen
- Gardening
- Health
- Home
- Literature
- Music
- Networking
- Other
- Party
- Religion
- Shopping
- Sports
- Theater
- Wellness
- IT, Cloud, Software and Technology