Recycled Plastic Granules: A Valuable Resource for Various Industries
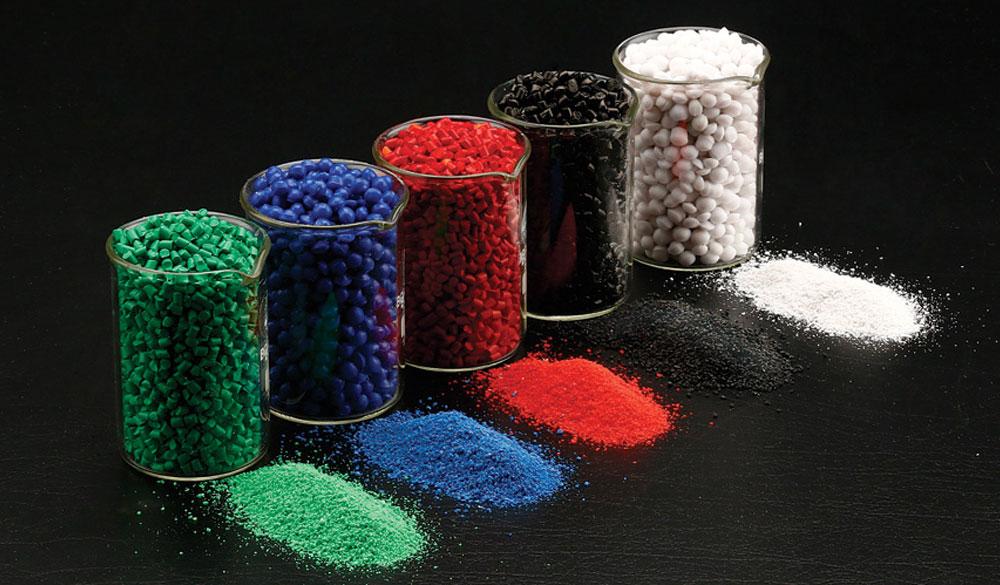
Properties and Production of Recycled Plastic Granules
Recycled plastic granules are small resin pellets produced from plastic waste such as plastic bottles, containers, bags, and films. The plastic waste goes through an intensive cleaning, sorting, shredding, and grinding process to break it down into uniform granules. The granules preserve the key properties of the original plastic resin while ensuring consistency for industrial uses.
The production process starts with collecting plastic waste from municipal recycling programs or industrial sources. Workers first manually sort the plastics by resin type, including polyethylene terephthalate (PET), high-density polyethylene (HDPE), polyvinyl chloride (PVC), low-density polyethylene (LDPE), and polypropylene (PP). The sorted plastics then go through intensive washing to remove dirt, labels, and other contaminants.
Next, the cleaned plastics enter a serie of shredders and granulators that finely shred the materials. Powerful shredding blades break the plastics into fine flakes that are further ground into uniform plastic pellets or granules around 2-5 millimeters in size. Modern automated equipment can process thousands of pounds of plastic waste per hour. Quality checks ensure only high purity granules meet standards for industrial use.
Applications in Manufacturing Industries
Recycled Plastic Granules find many applications thanks to their versatile mechanical properties and lower costs compared to virgin plastics. Common uses include:
Plastic Molding - Injection and blow molding are two major applications. The granules are remelted and formed into new plastic consumer goods like packaging, containers, furniture, and automobile parts. Recycled content averages 20-30% without compromising product quality.
Construction Materials - Granules are mixed into asphalt to produce eco-friendly asphalt pavement with recycled content up to 15-20%. They also feature in fence posts, decking, drainage pipes, and insulation boards.
Landscaping - Rotomolded plastic lumber, landscape edging, parking stops, and outdoor furniture use 10-50% recycled plastic content. The durable, weatherproof materials provide long service life with reduced environmental footprint.
Textiles - Fiber manufacturers produce polyester and nylon fibers from recycled plastic waste. Spun into yarn, the fibers find applications in clothing, geotextiles, and industrial fabrics.
The Benefits of Using Recycled Plastic Granules
There are significant economic and environmental benefits associated with using recycled plastic granules as a substitute for virgin plastic resins in various applications:
Reduced Production Costs - Recycled plastic costs 20-50% less than equivalent virgin plastic. Lower feedstock costs transfer significant savings potential to product manufacturers.
Resource Conservation - Manufacturing plastic from recycled feedstock requires 80-90% less energy than using fossil fuels to produce virgin plastic from crude oil. This reduces overall environmental impact.
Landfill Diversion - Recycling plastic waste prevents valuable plastic materials from entering overflowing landfills and persisting in the environment for centuries. The U.S. alone discards over 32 million tons of plastic annually.
Sustainable Materials Supply - With global crude oil reserves depleting, recycled plastic serves as a renewable resource that does not rely on non-renewable fossil fuels. It guarantees a stable plastics supply chain.
Green Image and Credentials - Incorporating recycled plastic content helps manufacturers achieve sustainability certifications and promotes their brands as environmentally conscious. This improves public perception and market positioning.
Challenges in Utilizing Recycled Plastic More Broadly
While recycled plastic granules present an attractive value proposition for industry as well as municipalities managing plastic waste, certain challenges currently limit their widespread use:
Quality Control Issues - The mixed nature of real-world plastic waste streams means granules can contain contaminants. Quality fluctuations make them unreliable feedstock compared to standardized virgin plastics.
End Market Demand - Stable market demand pull is needed from large-volume plastic product manufacturers in major consuming sectors to continually absorb available recycled plastic supply.
Economic Incentives - Government incentives like tax relief or purchase mandates could stimulate more collection, recycling infrastructure investment, and end-use markets for recycled plastics on a national scale.
Standardization Needs - Uniform specifications, testing protocols, and classification are lacking for recycled plastic types and quality grades. This uncertainty limits supply chain integration.
Behavior Change - Public education and policy tools are still needed to significantly improve plastic waste diversion rates from landfilling and boost recycling infrastructure.
In summary, recycled plastic granules exemplify how sustainably reclaiming plastic waste resources can benefit both the environment and industry if challenges around quality, demand, and standardization can be progressively addressed through innovation and collaborative effort across the plastics value chain.
Get more insights on This Topic- Recycled Plastic Granules
- Art
- Causes
- Crafts
- Dance
- Drinks
- Film
- Fitness
- Food
- Jogos
- Gardening
- Health
- Início
- Literature
- Music
- Networking
- Outro
- Party
- Religion
- Shopping
- Sports
- Theater
- Wellness
- IT, Cloud, Software and Technology