Marine Coatings Market: Protecting Ships from Corrosion in Harsh Marine Environments
Introduction to Marine Coatings
Marine coatings, also known as marine paints, are specialized paints and coatings used for surfaces submerged in sea water or exposed to marine environments. They protect the hulls and other exterior parts of ships, offshore oil rigs, yachts and other marine vessels from corrosion caused by salt water, abrasion from ocean waves and biological fouling from aquatic organisms. Different types of marine coatings are used depending on the specific application and environmental conditions. In this article we’ll explore the marine coatings market outlook.
Epoxy Coatings for Anti-Corrosion Protection
Epoxy coatings are some of the most popular and widely used marine coatings today due to their excellent barrier protection against corrosion. They form a tough, chemical-resistant film once cured that strongly adheres to metal surfaces and acts as an effective barrier to moisture and oxygen permeation. This prevents corrosion even under prolonged immersion in seawater. Epoxy coatings provide robust adhesion to steel, creating an impervious layer that insulates the metal surface from corrosive ions in seawater. Their chemical resistance also makes them suitable for marine vessels operating in polluted waters or carrying chemical cargoes.
Fouling Release Coatings to Reduce Drag
Fouling release coatings are specifically designed to prevent calcareous marine organisms like barnacles and tube worms from attaching to ship hulls. By reducing drag-inducing biofouling buildup, these coatings can significantly reduce fuel costs and emissions for shipping and cruise companies. They work by creating very slippery surfaces that prevent initial attachment of fouling organisms yet facilitate easy release of any organisms that do manage to attach. Common fouling release coating chemistries include silicone elastomers and fluoropolymers that maintain non-stick properties even after years of being submerged.
Anti-Corrosive Paints for Decks and Superstructures
Specialized anti-corrosive paints are needed to protect the exterior metal surfaces above waterline like ship decks and superstructures. These are subjected to weathering from sun, rain, thermal changes and occasional water splashes. Offshore oil rig structural steel also require similar protection in harsh conditions like sea spray and weather exposure. The coatings used include high-durability epoxies, polyurethanes and acrylics that form exterior grade films resistant to ultraviolet (UV) rays, moisture and corrosion. Tropical-grade versions offer additional UV resistance for equatorial maritime regions.
Anodes for Cathodic Protection on Ship Hulls
Galvanic or sacrificial anodes are another important part of marine anti-corrosion systems. They work by cathodic protection where the anode metal corrodes preferentially instead of the ship's hull. Common anode metals used include aluminum, zinc and magnesium. These are fastened to the ship's hull and act as a galvanic cell to divert corrosion from the steel onto themselves through an electrochemical reaction. This increases the lifespan and corrosion resistance of marine vessels considerably, especially oil tankers and LNG carriers operating in corrosive saltwater conditions.
New Biocidal Coatings to Prevent Marine Fouling
Environmentally-compliant self-polishing copolymer (SPC) antifouling coatings were introduced in 2008 to replace tributyltin-based paints banned for releasing toxic organotins into the marine environment. SPCs are swellable pigment-filled paints that employ controlled release of biocides like copper and zinc to prevent fouling settlement without polluting surrounding waters. Newer research focuses on developing non-biocidal fouling release and slime release polymer coatings as more ecofriendly alternatives. Nanotechnology is another area being explored for next-gen non-stick, self-cleaning marine coating solutions.
Application and Maintenance of Marine Coatings
Special surface preparation involving grit blasting or power tool cleaning is needed for marine coatings to strongly bind to substrates. Primers are often applied as an undercoat before topcoats. Proper application requires observing conditions such as temperature, humidity, wet film thickness. Multiple coats may be needed with intermediate drying for some coatings. Maintenance involves regular inspections and overcoating/touch-ups to areas suffering excessive wear. MILD steel structures require ongoing sacificial anode maintenance. Advanced coating systems are minimized downtime for vessels and offshore rigs.
In summary, marine coatings protect ships and other maritime vessels from corrosion through barrier protection and sacrificial reactions, these features will provide positive impact to the growth of the marine coatings market. Choosing the right coating type according to application environment and conditions ensures durability and cost savings in the long run. Ongoing research also aims to develop more eco-friendly and foul-release based coating technologies for the shipping and offshore industries. With specialized formulations and optimized application-maintenance protocols, today's marine coatings can deliver years of reliable service even under demanding saltwater conditions. This safeguards maritime infrastructure assets and facilitates uninterrupted global seaborne trade and offshore operations.
Innovations Driving the Future of Marine Coatings Market
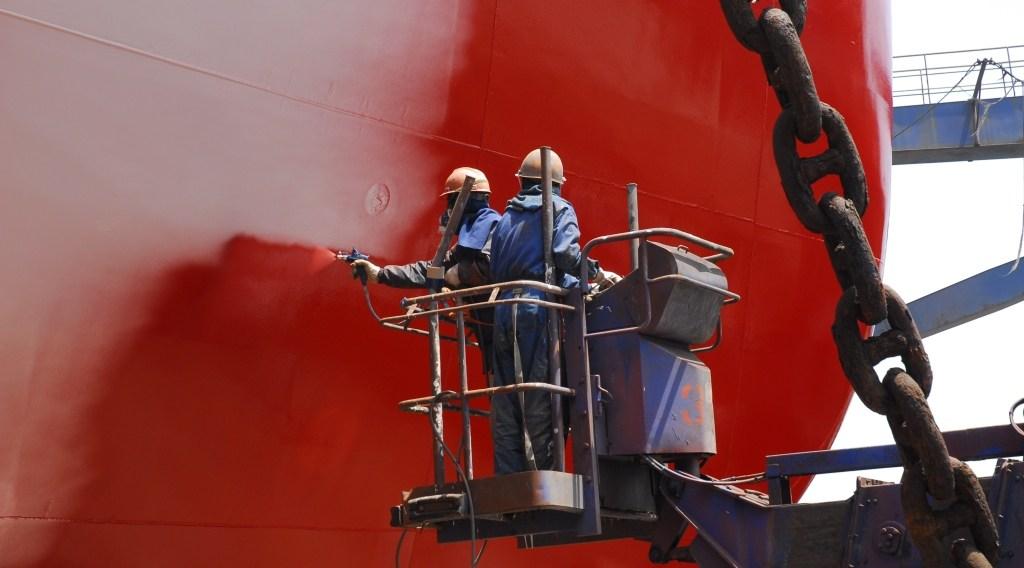