Beyond Dimensions: The Importance of Tolerance Analysis in Product Design Optimization
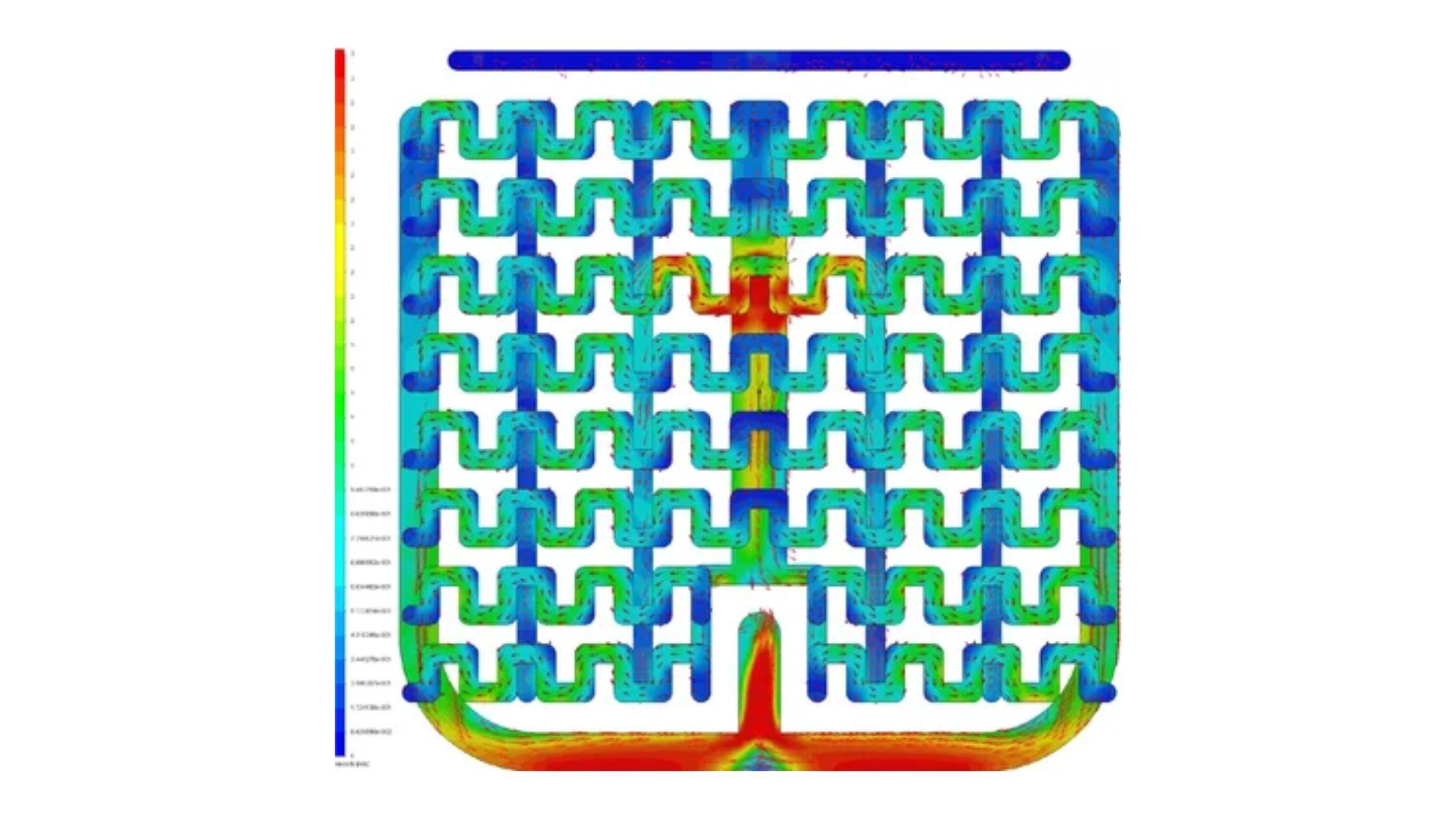
While designing any product, every detail matters, tolerance analysis stands as a pivotal process in ensuring optimal performance and quality. From aerospace components to consumer electronics, the meticulous assessment of dimensional variations and specifications is indispensable for achieving proper fit, functionality, and reliability. In this blog, we'll delve into the importance of tolerance analysis in product design, highlighting its crucial role in ensuring proper fit and functionality of assemblies, reducing manufacturing defects, and ultimately improving overall product quality.
Understanding Tolerance Analysis
Tolerance analysis involves the systematic evaluation of dimensional variations and specifications within an assembly to ensure that all parts fit together properly and that the assembly operates as intended. It addresses the inevitable variations that occur during the manufacturing process, such as variations in material properties, machining tolerances, and assembly methods. By quantifying these variations and their potential impact on product performance, engineers can make informed decisions to mitigate risks and optimize designs.
Ensuring Proper Fit and Functionality
At the heart of tolerance analysis lies the goal of ensuring proper fit and functionality of assemblies. In complex systems comprising numerous components, even minor deviations in dimensions or tolerances can lead to issues such as misalignment, interference, or inability to assemble parts correctly. Tolerance analysis allows engineers to assess the cumulative effect of dimensional variations and adjust tolerances accordingly to achieve precise mating and alignment of components. This ensures that the product functions as intended and enhances user experience and reliability.
Reducing Manufacturing Defects
One of the primary objectives of tolerance analysis is to identify and mitigate potential manufacturing defects early in the design process. By simulating various manufacturing scenarios and assessing the impact of tolerances on part quality, engineers can anticipate and address potential issues before they occur. This proactive approach reduce the risk of defects, such as parts being out of specification, excessive scrap rates, or assembly failures, thereby reducing rework, waste, and production costs.
Improving Overall Product Quality
Ultimately, the overarching goal of tolerance analysis is to improve overall product quality. By ensuring that components are manufactured within specified tolerances and that assemblies are designed to accommodate variations, engineers can enhance the performance, reliability, and durability of the final product. Tolerance analysis helps identify critical features and dimensions that significantly impact product functionality and quality, allowing engineers to prioritize areas for optimization and refinement.
Case Study: Tolerance Analysis in Automotive Design
To illustrate the importance of tolerance analysis, let's consider a case study in automotive design. In developing a new vehicle transmission system, engineers must ensure precise alignment and mating of gears, shafts, and bearings to optimize performance and efficiency. Through tolerance analysis, engineers can assess the dimensional variations in each component and evaluate their cumulative effect on gear meshing, lubrication, and power transmission. By fine-tuning tolerances and optimizing component designs, engineers can minimize friction, reduce noise and vibration, and enhance overall drivetrain performance.
Conclusion
Tolerance analysis plays a fundamental role in the product design process, serving as a cornerstone of precision and quality. By meticulously assessing dimensional variations and specifications, engineers can ensure proper fit and functionality of assemblies, reduce manufacturing defects, and ultimately improve overall product quality. Tolerance analysis empowers designers to anticipate and address potential issues early in the design phase, leading to more efficient production processes, enhanced performance, and greater customer satisfaction. As technology continues to evolve, the importance of tolerance analysis in achieving design excellence and innovation will only continue to grow.
- Art
- Causes
- Crafts
- Dance
- Drinks
- Film
- Fitness
- Food
- الألعاب
- Gardening
- Health
- الرئيسية
- Literature
- Music
- Networking
- أخرى
- Party
- Religion
- Shopping
- Sports
- Theater
- Wellness
- IT, Cloud, Software and Technology