Benefits digitalization can bring to chemical industry
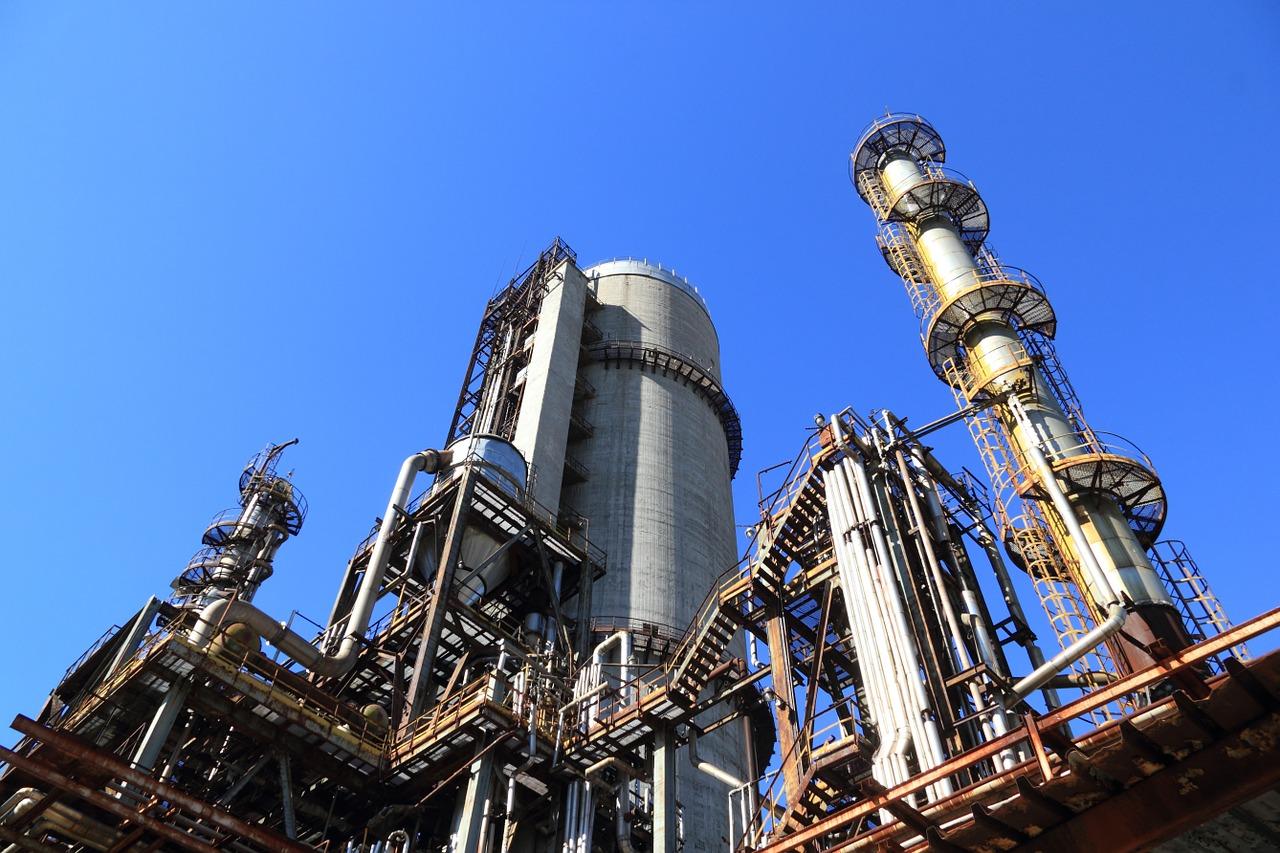
It can not only realize the learning of specific factories, but also speed up the training time while reducing risks and costs
When the COVID-19 broke out, the chemical industry with adverse risks had been on the road of Digitalization for a long time. The restrictive measures taken to limit the spread of the pandemic have accelerated the pace of change, because the industry needs to strengthen safe and reliable remote operations and work as much as possible.
In order to adapt to today's "new normal", chemical enterprises understand that many changes brought by the epidemic to work practices will continue. Those enterprises that invest in digital transformation have seen the benefits that digitalization can bring to this highly complex industry, such as process optimization and risk reduction.
Immersive learning
Technologies such as artificial intelligence (AI), machine learning (ML) and cloud computing are used to collect, store and analyze data, and then transform these data into actionable insights, thereby improving operational efficiency and security performance. But there is another area of interest: immersive training.
With the retirement of experienced operators and engineers, the chemical industry is facing the intergenerational transfer of labor, and it is increasingly necessary to transfer professional knowledge to younger workers. However, until recently, the industry has largely relied on traditional training methods, which do not really involve digital natives.
In high-risk industries such as chemicals, all employees must participate in and receive training in order to do their work safely. The answer lies in immersive training, which brings learning to life in an environment that this generation understands and embraces.
Engaging Staff
Today's young employees grow up in an immersive 3D environment, where they can interact, explore, make mistakes, and then try again. This may be the way they play video games with their friends, but these virtual worlds can also be used for industrial training.
Immersive training uses technologies such as augmented reality and virtual reality (AR and VR) to provide fascinating experiential learning in a safe, controllable and realistic virtual environment. Here, the customized training system is combined with ready-made game peripherals (such as host controller and VR headgear such as oculus rift) to support the learning of new employees and experienced employees.
AR and VR training can be used in many ways, which is crucial to the safety and performance of the factory, because it reduces the risk of accidents and reduces the need to close the factory for real training. New operators can learn and practice high-risk industrial procedures in safety training simulators, while teams "learn while doing" by using dynamic simulation learning scenarios.
Benefits of unification
The general VR and AR training environment has its own position, but by unifying many enterprise systems into a secure data center, chemical enterprises can reduce the time and energy to share detailed engineering data and strengthen learning by providing training scenarios for their businesses.
For example, connecting with the company's digital twins can expose the trainers to the plants in the immersive 3D real world, and even let the training environment simulate the dynamic process behavior of plants.
By using these unique virtual environments, enterprises can be sure that their employees understand the situation around the factory and the impact of wrong decisions, as well as performance improvements from correct safety and reliability practices, without affecting the safety and productivity of the factory and employees.
Cloud solutions
When you want to invest in immersive training solutions, it is best to consider cloud based solutions as much as possible.
The initial capital expenditure of the built-in simulator is high, but the subscription based cloud solution transfers the cost to the operating expenses matching the training activities and budget. In addition, internal solutions can only train a group of employees at a time. However, the cloud based option eliminates the constraints of self training and coaching modules.
As the European training center of total group's oil and petrochemical business, oleum is an early user of cloud based operator training simulator (OTS). By integrating OTs and enterprise learning management system, the company has found a modern, scalable, flexible and economic solution, which can expand the training capacity of operators without spending millions of dollars on travel expenses, and reduce the time of training operators from a few months to a few weeks.
Empower new employees
BASF is another chemical company that uses immersive training to train new operators, technicians and engineers. The company created a virtual reality version of the regional training center to enable its apprentices to conduct the same virtual training. They will start training in the virtual environment, and then enter the real workshop.
Alexander Karle, BASF chemical operator training director, said: "they like VR training very much because the system is similar to what they use at home."
"These children have just graduated from school and have no experience in process technology, so they must take the first step in the virtual environment and learn the operating system without causing any risk to themselves or equipment. When they enter the real training environment, they will feel more confident," Kahler added.
Students should return to VR environment during the whole learning process. BASF is very satisfied with the effect of the platform. So that the company now hopes to develop it as a cloud based solution so that apprentices can continue to study at home.
Maximize the return on training investment
Augmented reality technology and virtual reality technology enable enterprises to provide sustainable, efficient and effective accelerated training to maximize the return on investment (ROI) of factory personnel training.
Looking forward to the future, it is wise for companies to invest in immersive training now. This will ensure that their next generation of operators and engineers can maximize their role by providing an attractive and interactive training environment.
The latest generation of immersive digital tools enables enterprises to improve the efficiency and development of their training programs in a cost-effective and flexible way. Therefore, it is wise for companies looking forward to the future to invest in immersive training now.
This will ensure that they can get the most from the next generation of operators and engineers by providing an attractive and interactive training environment, so that they can stand out.
- Art
- Causes
- Crafts
- Dance
- Drinks
- Film
- Fitness
- Food
- Giochi
- Gardening
- Health
- Home
- Literature
- Music
- Networking
- Altre informazioni
- Party
- Religion
- Shopping
- Sports
- Theater
- Wellness
- IT, Cloud, Software and Technology