What Are Industrial Warp Knitting Base Fabrics
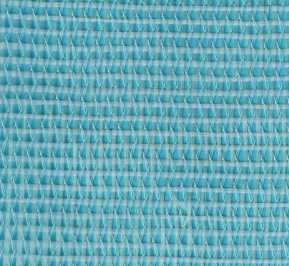
Industrial warp knitting base fabrics use a warp knitting process.
Warp knitting offers material construction flexibility unmatched by many other methods. From flexible multi-layer materials for automotive interiors and flame retardant fabrics to advanced material processes for lamination of various medical fabrics, protective clothing, and equipment, the use of high-performance warp knitting is exploding in a wide variety of applications. Many industry players are unfamiliar with the yarn production process and how technical fabrics and knitting play a powerful and growing role in the advanced material selection process.
By forming loops in the vertical or warp direction, the fabric produced by warp knitting has a flatter, tighter, and less elastic knit. Warp knitting is usually produced across the beam and is the fastest way to convert yarn into fabric, making it efficient and cost-effective. Some other benefits of warp knitting include:
Structure: more knots lead to more form while maintaining some give and take;
Flexibility: small shrinkage, good tensile properties;
Customization: Highly customized technical features allow you to deal with more diverse design projects;
Versatility: Warp knitting can make solid fabrics, meshes, and geogrids.
With its structured adaptability, cost-effective output, and ability to fashion around novel designs, warp knitting is the best choice for many advanced material fabric projects.
Haining Jingda Cloth Industry Co., Ltd. is a garment fabrics manufacturer, its main products are polyester and other fabric products, welcome to inquire!
- Art
- Causes
- Crafts
- Dance
- Drinks
- Film
- Fitness
- Food
- Games
- Gardening
- Health
- Home
- Literature
- Music
- Networking
- Other
- Party
- Religion
- Shopping
- Sports
- Theater
- Wellness
- IT, Cloud, Software and Technology