Train HVAC Systems: Ensuring Passenger Comfort During Travel
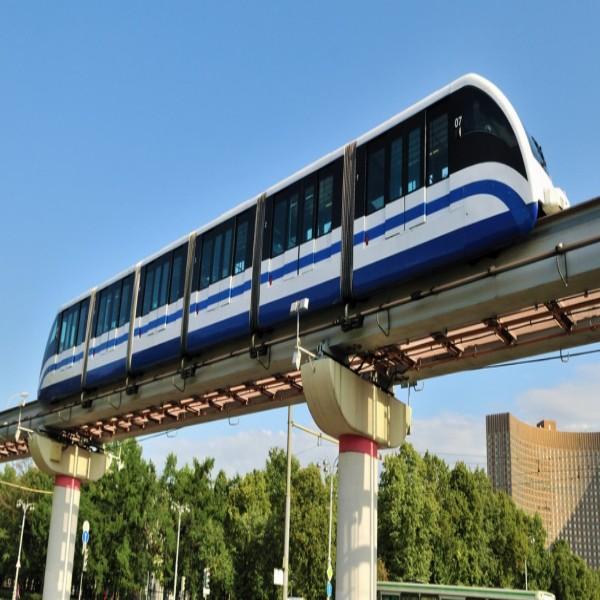
HVAC Design Considerations for Trains
Train HVAC systems must be designed to efficiently heat and cool large volumes of air while operating within the constraints of vehicle design and power availability. Locomotives often have limited on-board power generating capacity, so HVAC units are optimized for energy efficiency. Temperature control needs also vary significantly based on exterior weather conditions and passenger load.
Distribution of conditioned air throughout the train is another design challenge. Airflow needs to reach all passenger seating areas while preventing drafts. Distribution ducting must have minimal leakage and be able to bypass cars that are not in use. Controls adjust airflow based on real-time sensor data from different zones.
Heating Systems
Electric resistance heating, heat pumps, and waste heat recovery from other mechanical systems are common train heating technologies. Resistance heating directly generates heat from current flowing through heating elements. However, it is energy inefficient compared to heat pumps.
Heat pumps transfer thermal energy from one medium to another rather than generating heat. Train HVAC use less power but require space for outdoor heat exchangers. Waste heat recovery captures exhaust heat from engines, compressors or generators to pre-warm intake air.
Ventilation and Filtration
Proper ventilation is crucial on trains carrying many passengers over extended periods. Outside air is drawn into the HVAC system through intake vents. It passes through high-efficiency particulate arrestor (HEPA) or other filters before being heated or cooled.
Filtration removes airborne particles, allergens and pathogens from recirculated cabin air. Some systems also include activated carbon or potassium permanganate filters to adsorb odors and gases. Ventilation rates adjust based on occupancy levels and air quality sensors. Cabin pressure is slightly higher than the outside to prevent inward drafts.
Cooling Systems
Air conditioning units for trains require compact and energy-efficient designs. Various technologies are used such as vapor compression, thermoelectric, thermo-acoustic and heat pipe systems. Vapor compression is the most common approach for larger locomotives and passenger coaches.
It uses a refrigerant circuit, compressor, condenser, expansion valve and evaporator similar to household A/C units. Smaller thermoelectric coolers directly convert electric current to a temperature difference between two conductive plates. Newer absorption chillers can upgrade waste heat to cooling capacity.
Get more insights on Train HVAC
- Art
- Causes
- Crafts
- Dance
- Drinks
- Film
- Fitness
- Food
- Jogos
- Gardening
- Health
- Início
- Literature
- Music
- Networking
- Outro
- Party
- Religion
- Shopping
- Sports
- Theater
- Wellness
- IT, Cloud, Software and Technology