Machine Condition Monitoring Enabling Predictive Maintenance and Reducing Operation Costs
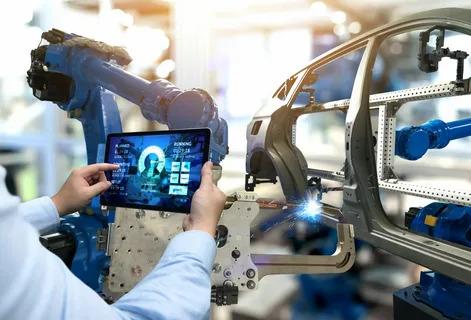
Introduction
With machines being the backbone of industrial operations, preventing unexpected downtime and maintaining high equipment reliability is crucial. Traditionally, maintenance was performed on a scheduled or reactive basis after a failure occurred. However, this run-to-fail approach leads to unplanned downtime and higher costs in the long run. Machine condition monitoring enables a proactive maintenance approach through continuous equipment performance monitoring and fault detection. This allows issues to be addressed before a breakdown and helps maximize asset uptime.
Condition Monitoring Technologies
A variety of sensor-based technologies are used for continuous Machine Condition Monitoring. Vibration analysis is one of the most common techniques to detect mechanical and structural faults in rotating equipment like motors, pumps and compressors. Changes in vibration levels and frequencies indicate developing issues like unbalance, misalignment and bearing damage. Thermography uses infrared cameras to detect high temperature spots indicating electrical or mechanical problems. Oil analysis helps identify wear particles in lubricating oil and predicts component condition. Acoustic monitoring tracks unusual noise patterns from machines. Other technologies like ultrasound, motor current signature analysis also provide key condition parameters.
ROI and Machine Condition Monitoring
While upfront investment is required for hardware, software, skills development and data management, the overall ROI on predictive maintenance ranges from 300-800% depending on the industry, according to studies. Downtime costs are significantly reduced through early fault detection and proactive repairs improving plant/system availability. Long-term maintenance costs also decrease through optimized spare part inventory and extended asset life. When implemented as part of an overall asset management strategy, predictive maintenance maximizes efficiency through improved reliability, safety and productivity. Cloud-based solutions have also reduced implementation time facilitating its adoption across industries. With gains in the Industrial Internet and advanced analytics, predictive maintenance will become more pervasive and powerful in the future.
By continuously monitoring equipment parameters and detecting anomalies early through powerful technologies and analytics, predictive maintenance enables a condition-based proactive strategy for asset management. This significantly reduces unplanned downtime, cuts maintenance costs through optimized repairs, extends asset life and improves overall plant reliability. Being able to accurately determine remaining useful life facilitates effective asset replacement planning. Industries across the board are leveraging these benefits to drive greater profits through improved efficiencies, productivity and enhanced safety through prevention of catastrophic failures. Predictive maintenance will continue growing as next-gen IIoT systems and analytics deliver more valuable insights for optimized maintenance planning.
Get more insights on Machine Condition Monitoring
- Art
- Causes
- Crafts
- Dance
- Drinks
- Film
- Fitness
- Food
- Games
- Gardening
- Health
- Home
- Literature
- Music
- Networking
- Other
- Party
- Religion
- Shopping
- Sports
- Theater
- Wellness
- IT, Cloud, Software and Technology