Why You Should Hire a Piping Stress Analysis Company
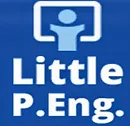
Piping systems are an important part of any facility, and they must be designed to withstand the stresses that can be put on them on a daily basis. This includes pressure, thermal, seismic, and other loads that can cause damage or failure to the system. Piping stress analysis is the process of determining how strong or how vulnerable your system is to these loads. It also ensures that your piping is built to meet the required safety and regulatory standards imposed on it.
A piping stress analysis company should be able to provide you with the services you need to properly evaluate your piping and ensure that it is safe to operate under all conditions. They should have experience with various piping materials and operating conditions, and they should be familiar with the industry’s codes and regulations that govern them. Additionally, they should have extensive knowledge of engineering work planning and control methods. Finally, they should be able to perform a variety of analytical models for piping systems and other structural components.
Pipe stress analysis is a process of predicting the stresses and reactions in a piping system or on equipment like tanks, vessels, pumps, mixers, exchangers and fire-tube boilers to be sure that they are within their design limits. Performing this analysis can help to avoid issues like upheaval buckling, fluid hammer and other problems that can be costly and dangerous.
It’s especially important to conduct a piping stress analysis when you’re designing a new system, and it’s equally critical for existing facilities. The stresses in your piping can change over time, and the conditions under which they are operated can be different from when they were initially designed. Therefore, it’s important to get them analyzed regularly so that you can identify potential problems before they become a serious issue.
Some pipes are more likely to require a piping stress analysis than others, including those that will be subjected to extreme temperatures or conditions, those that connect to sensitive equipment, and those that will undergo special cases such as depressurization and repressurization. Other factors that could require a stress analysis include changes in piping material specification, tie-in locations and revisions to applicable codes and standards.
Using standard commercially available software, PSI constructs the model, applies the client specified load & design conditions and processes and evaluates the results. The resulting analysis can show deflections, rotations, linear and nonlinear reactions, nozzle loading, fatigue, seismic effects, stress distributions and more. If there are any areas where the loads are too high, PSI can work with the customer to develop mitigation solutions like changing the support layout or increasing the load capacity.
- Art
- Causes
- Crafts
- Dance
- Drinks
- Film
- Fitness
- Food
- Giochi
- Gardening
- Health
- Home
- Literature
- Music
- Networking
- Altre informazioni
- Party
- Religion
- Shopping
- Sports
- Theater
- Wellness
- IT, Cloud, Software and Technology