HDPE Sheets: The Versatile Power of HDPE Plastic Sheets in Modern Applications
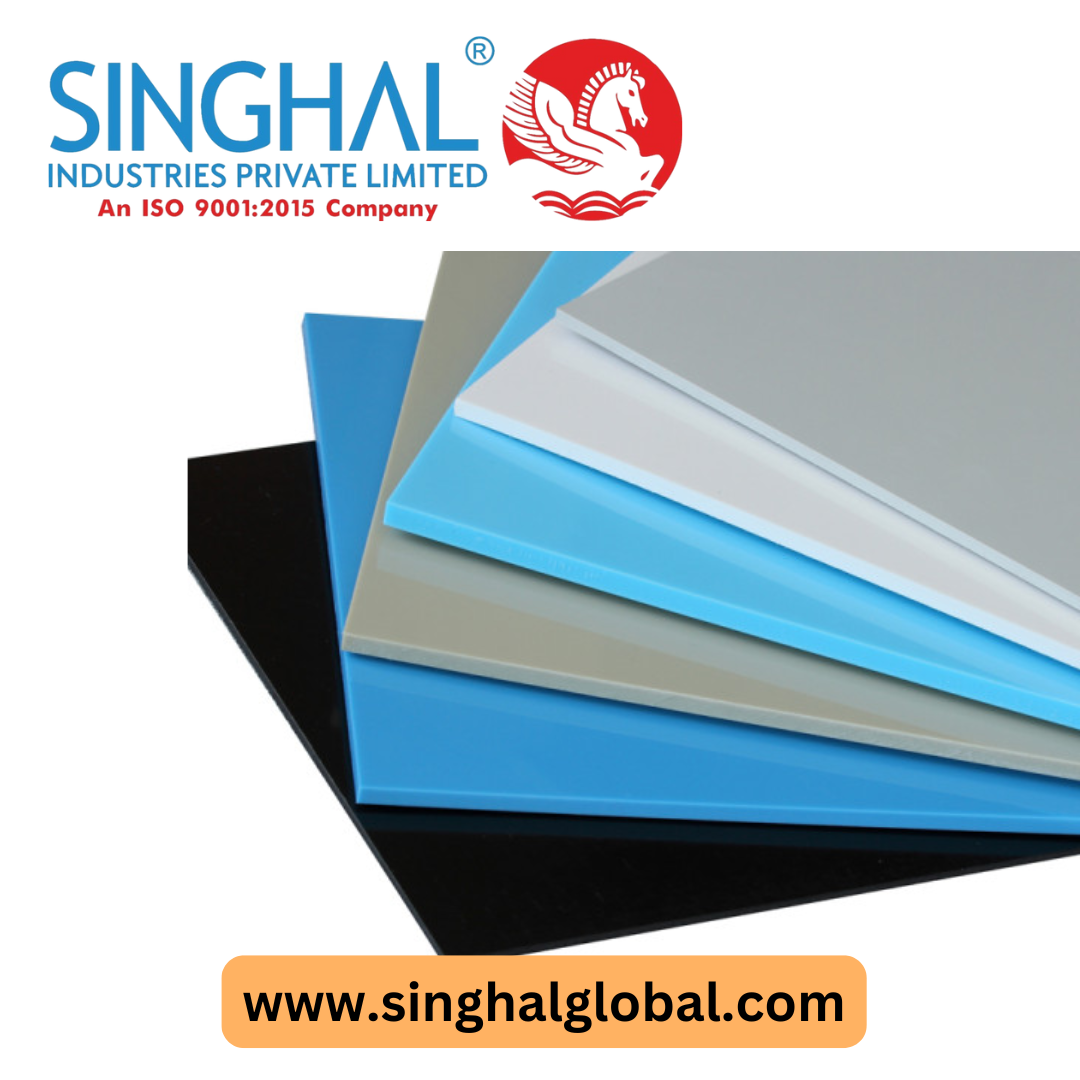
High-Density Polyethylene (HDPE) sheets are a fundamental material in the world of plastics, offering a combination of durability, flexibility, and resistance that makes them suitable for a wide range of applications. From industrial uses to everyday products, HDPE sheets are celebrated for their strength and versatility. This article delves into the properties, benefits, types, applications, and installation of Polyethylene Sheets, providing a comprehensive overview of why they are a preferred choice in various industries.
What are HDPE Sheets?
HDPE sheets are made from high-density polyethylene, a thermoplastic polymer known for its high strength-to-density ratio. HDPE is created through the polymerization of ethylene, resulting in a material that is robust, lightweight, and resistant to impact. HDPE sheets are available in various thicknesses and sizes, making them suitable for a multitude of applications.
Key Properties of HDPE Sheets
HDPE sheets boast a range of properties that contribute to their widespread use. These properties include:
-
Durability: HDPE sheets are highly resistant to impact and can withstand significant stress without cracking or breaking. This makes them ideal for applications that require robust, long-lasting materials.
-
Chemical Resistance: HDPE is resistant to many chemicals, including acids, alkalis, and solvents. This property makes HDPE sheets suitable for use in chemical processing and storage.
-
Weather Resistance: HDPE sheets can endure harsh weather conditions, including exposure to UV rays and extreme temperatures. They do not degrade or become brittle under prolonged sunlight or temperature fluctuations.
-
Low Moisture Absorption: HDPE sheets have low moisture absorption, preventing them from swelling or deforming when exposed to water or other liquids.
-
Flexibility: Despite their strength, HDPE sheets are flexible and can be easily cut, shaped, or welded to fit various applications.
-
Ease of Fabrication: HDPE sheets can be fabricated using standard techniques such as welding, machining, and thermoforming, making them versatile for different projects.
Types of HDPE Sheets
HDPE sheets come in various types, each tailored for specific applications:
-
Standard HDPE Sheets: These are the most common type of HDPE sheets, used in a wide range of general-purpose applications. They offer excellent impact resistance and durability.
-
Anti-Slip HDPE Sheets: These sheets feature a textured surface that provides additional grip, making them ideal for applications where slip resistance is crucial, such as flooring and industrial walkways.
-
Colored HDPE Sheets: Available in various colors, these sheets are used for aesthetic purposes or to color-code different parts of a system or product. They maintain the same durability and resistance as standard HDPE sheets.
-
High-Gloss HDPE Sheets: These sheets have a smooth, glossy surface and are often used in applications requiring a polished appearance, such as display panels and signage.
-
Recycled HDPE Sheets: Made from recycled HDPE material, these sheets offer an eco-friendly option for those seeking sustainable materials while still benefiting from the properties of HDPE.
Applications of HDPE Sheets
HDPE sheets are used across numerous industries due to their versatile properties. Some common applications include:
-
Construction and Architecture: HDPE sheets are used for various construction purposes, including barriers, cladding, and drainage systems. Their durability and weather resistance make them suitable for both residential and commercial buildings.
-
Industrial Applications: In industrial settings, HDPE sheets are used for equipment liners, containment barriers, and structural components. Their chemical resistance and durability make them ideal for handling harsh environments and substances.
-
Agriculture: HDPE sheets are employed in agricultural applications such as pond liners, greenhouse coverings, and silage bags. They help in controlling soil moisture and protecting crops from adverse conditions.
-
Transportation: HDPE sheets are used in the transportation sector for vehicle components, such as truck liners and panels, due to their impact resistance and ability to withstand extreme temperatures.
-
Food Processing: In the food industry, HDPE sheets are used for food-grade applications such as cutting boards and conveyor belts. Their low moisture absorption and ease of cleaning make them suitable for food processing environments.
-
Signage and Display: HDPE sheets are often used for signage and display panels, thanks to their ability to be easily fabricated into various shapes and their high-quality appearance.
Installation and Fabrication of HDPE Sheets
The Polyethylene Roll are relatively easy to work with, thanks to their flexibility and ease of fabrication. Here are some common methods for working with HDPE sheets:
-
Cutting: HDPE sheets can be cut using standard tools such as saws, knives, or laser cutters. For precise cuts, a table saw or CNC machine is recommended.
-
Welding: HDPE sheets can be welded using hot-air welding or extrusion welding techniques. These methods create strong, seamless joints, making them ideal for applications requiring a high degree of structural integrity.
-
Drilling and Machining: HDPE sheets can be drilled and machined using standard equipment. It is important to use sharp tools and avoid overheating to maintain the material's integrity.
-
Adhesive Bonding: Although less common, HDPE sheets can be bonded using specialized adhesives designed for plastic materials.
-
Thermoforming: HDPE sheets can be heated and shaped using thermoforming techniques, allowing them to be molded into complex shapes for various applications.
Benefits of Using HDPE Sheets
HDPE sheets offer several benefits that make them a popular choice across various industries:
-
Cost-Effectiveness: HDPE sheets provide a high-performance material at a relatively low cost. Their durability and resistance reduce the need for frequent replacements, offering long-term savings.
-
Environmental Impact: HDPE is a recyclable material, and using recycled HDPE sheets contributes to sustainability efforts. Additionally, their longevity reduces waste and the need for frequent replacements.
-
Low Maintenance: HDPE sheets are easy to clean and maintain. Their resistance to moisture and chemicals ensures that they remain in good condition with minimal upkeep.
-
Safety: HDPE sheets are non-toxic and do not release harmful fumes or chemicals, making them safe for use in food processing and other sensitive applications.
Conclusion
The High Density Polyethylene Plastic offer a versatile, durable, and cost-effective solution for a wide range of applications across various industries. Their unique properties, including high impact resistance, chemical resistance, and weather durability, make them an ideal choice for everything from construction and industrial uses to food processing and signage. With easy fabrication options and low maintenance requirements, HDPE sheets continue to be a preferred material for professionals and DIY enthusiasts alike. Whether you are working on a large-scale industrial project or a simple home improvement task, HDPE sheets provide the performance and reliability you need.
Frequently Asked Questions (FAQs)
Q1: How durable are HDPE sheets?
A1: HDPE sheets are highly durable, with excellent resistance to impact, weather conditions, and chemicals. They can last for decades, depending on the application and environmental conditions.
Q2: Can HDPE sheets be used outdoors?
A2: Yes, HDPE sheets are suitable for outdoor use due to their UV resistance and weather durability. They are commonly used in applications exposed to the elements, such as construction and agricultural projects.
Q3: Are HDPE sheets safe for food contact?
A3: Yes, HDPE sheets are safe for food contact and are often used in food processing and handling applications. They are non-toxic and do not leach harmful substances.
- Art
- Causes
- Crafts
- Dance
- Drinks
- Film
- Fitness
- Food
- Giochi
- Gardening
- Health
- Home
- Literature
- Music
- Networking
- Altre informazioni
- Party
- Religion
- Shopping
- Sports
- Theater
- Wellness
- IT, Cloud, Software and Technology