Substation Monitoring System: An Essential Tool for Electric Utilities
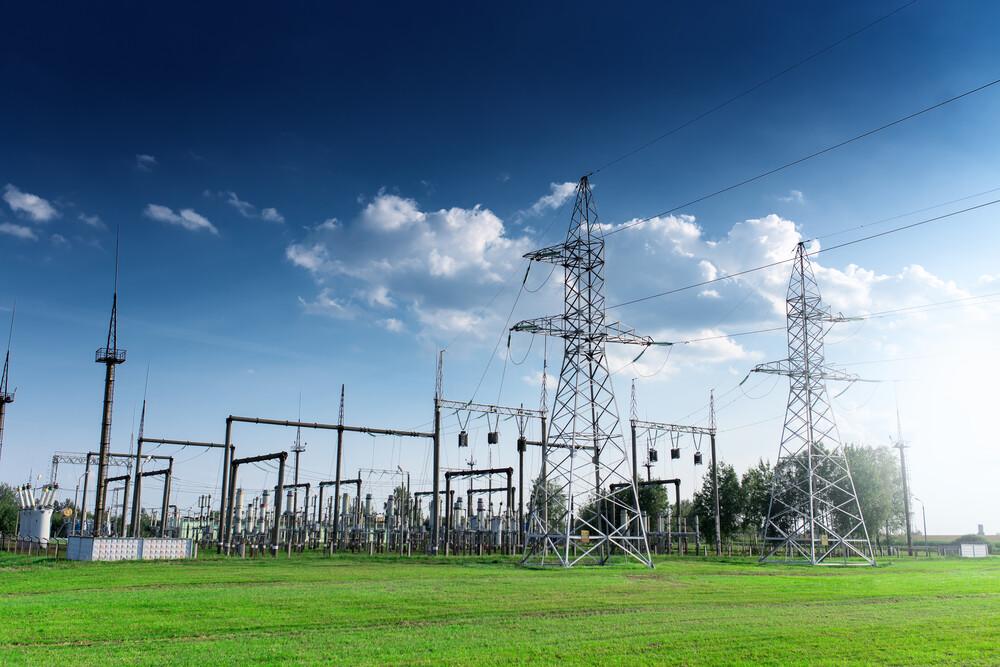
A substation monitoring system allows power companies to oversee their substations remotely in real-time. This improves reliability, safety, and efficiency across the electric grid. By detecting problems early, utilities can make repairs proactively and avoid outages. Remote monitoring also enhances worker safety by reducing the need for on-site inspections.
Hardware Components
Substation Monitoring System integrate a variety of hardware such as sensors, cameras, and programmable logic controllers (PLCs). Sensors monitor critical parameters like temperature, voltage, current, Pressure, resistance, and pollution levels. High resolution cameras provide live video surveillance of the entire substation area. PLCs serve as the core of the system, collecting all sensor data and transmitting it to the central control center via communications networks. Some key hardware includes:
- Temperature sensors to monitor equipment temperature rise which indicates overload or insulation failure.
- Voltage and current transformers to measure incoming and outgoing voltage/current levels.
- Gas sensors to detect levels of combustible, toxic and other hazardous gases leaks.
- Phasor measurement units to monitor power quality and grid balancing in real-time.
- Infrared cameras to detect hot spots on equipment visually without direct contact.
- Multi-agent PLCs equipped with I/O modules, memory, and CPU to aggregate all data.
Get more insights on - Substation Monitoring System
Get More Insights—Access the Report in the Language that Resonates with You.
- Art
- Causes
- Crafts
- Dance
- Drinks
- Film
- Fitness
- Food
- Juegos
- Gardening
- Health
- Home
- Literature
- Music
- Networking
- Other
- Party
- Religion
- Shopping
- Sports
- Theater
- Wellness
- IT, Cloud, Software and Technology