Overcoming Common Challenges in Thermoformed Plastics Production
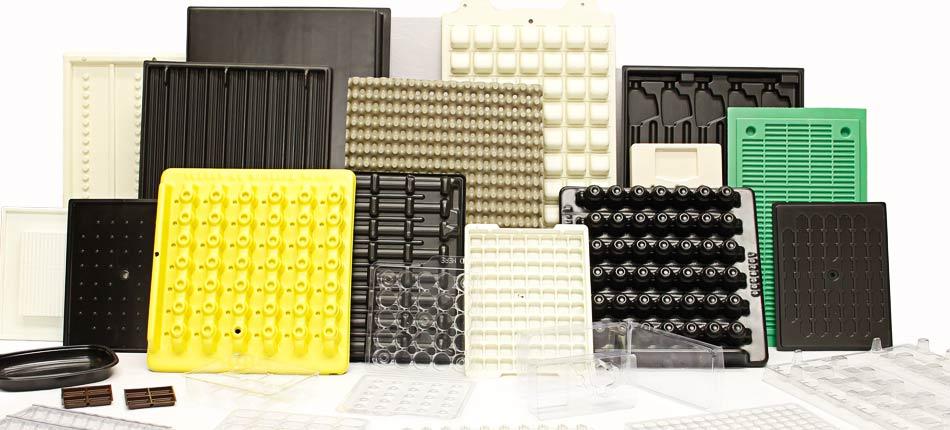
Understanding Thermoforming as a Manufacturing Process
Thermoforming is a manufacturing process where a plastic sheet is heated to a pliable forming temperature, formed to a specific shape in a mold, and trimmed to create a usable product. The key steps in thermoforming include heating, forming, cooling, and trimming. In the heating phase, a sheet of plastic such as PVC, polypropylene, or polystyrene is uniformly heated to its softening point. Once pliable, the sheet is then placed over a plaster, aluminum, or steel mold and drawn down using vacuum pressure or mechanical force. The sheet material closely conforms to the mold features and is left to cool, hardening its new shape. Finally, the excess plastic surrounding the mold outline is trimmed away, producing a formed plastic part ready for finishing, decoration, or assembly into a final product.
Compared to other plastic processing methods like injection molding, thermoforming allows for lower production costs thanks to fewer mold changes and less wasted material. It is also ideal for producing thin, contoured parts in small to medium batch sizes. Common thermoformed products include food and consumer packaging, appliances, medical devices, automotive components, and more. By understanding the thermoforming process in detail, manufacturers can optimize techniques for maximum part quality, throughput, and cost-effectiveness.
Key Thermoforming Methods
There are several main methods used in thervoforming depending on the application needs:
Vacuum forming is the most common technique, where the heated plastic sheet is clamped over a pre-formed mold or male plug. Vacuum pressure is then applied from below, sucking the sheet tightly over surfaces and features. This method works well for shallow draw depths and allows quick mold changes.
Pressure forming applies mechanical pressure from above using a stamp or press. It is better suited than vacuum for deep, complex part shapes with minimal flash or thickness variations. Pressure forming machines require more robust construction than vacuum machines.
Drape forming involves manually molding the softened sheet over an angled or contoured surface using gravity, pressure rolls, or clamping. It has the lowest capital investment of the forming methods.
Matched-die vacuum forming uses a top and bottom die that closes around the sheet, providing an even draw and more reproducible results compared to single-sided vacuum. However, it has a higher cost per cavity.
Thermoforming allows variation in material thickness by differentially heating zones of the sheet prior to forming. Combined with selective vacuum or pressure, this enables forming complex geometries with locally-modified thicknesses for functional requirements.
Factors Impacting Thermoforming Quality
Process parameters like plastic type and thickness, heating temperatures and times, draw rates, and cooling methods all directly influence the quality, strength, and aesthetics of formed parts. Careful control and optimization of these factors is needed for repeatable production of dimensionally accurate parts with no defects. Some of the main quality factors to consider include:
Heating Uniformity - Plastic must be heated evenly throughout to a precise softening point. Using carefully-zoned infrared or contact heaters help prevent warping or weak areas.
Material Strength & Stiffness - Crystalline plastics tend to be stronger but more difficult to form than amorphous polymers. Film thickness also dramatically affects stiffness and formability.
Draw Rates - Too fast a draw can result in thin, weak areas or splits, while too slow causes defects from non-uniform cooling. Controlled vacuum ramping optimizes consistent draws.
Dimensional Stability - Formed parts must be carefully trimmed while still warm to minimally shrink during cooling. Rapid trimming and handling limits shrinkage variation.
Surface Finish - Finish is influenced by factors like material clarity, heating control, mold material and texture. Polishing molds improves appearance replication.
As the demand for thermoformed parts grows in step with key end-markets, manufacturers continue refining techniques to overcome challenges and achieve the quality levels required. Automation, in-line process monitoring, and data-driven optimizations have taken forming capabilities to new heights.
Common Thermoformed Plastic Applications
Medical Device Packaging - Blister packs, sterilization wraps, procedure trays maximize protection while presenting products attractively. Gas permeability tuning preserves sterility.
Consumer Products - Food packaging like clamshells, cups, containers along with household appliances benefit from economical large volume production.
Automotive Interiors - Instrument panels, air vents, and trim components take advantage of thermoforming's design freedoms and ability to form complex shapes.
Electronics Enclosure - Housings for electronics, communications equipment, and industrial machinery demand high tolerances and feature replication that vacuum forming delivers cost-effectively.
Sanitary Equipment - Commercial restroom and foodservice fittings like trash bins and dispensers have durable, cleanable, chemically-resistant thermoformed plastic constructions.
Construction Materials - Wall panels, door skins, partitions and signs are made with weather-resistant reinforced composites thermoformed for architectural designs.
Other areas utilizing thermoformed plastic parts span medical devices, recreational vehicles, public transit vehicles, aviation/aerospace applications, agricultural equipment, and more. As long as the production volumes justify the capital investment, thermoforming provides a competitively-priced solution for fabricated plastic components and assemblies.
In summary, thermoforming has evolved into a mainstream manufacturing process capable of producing quality plastic parts in batches that meet the needs of diverse industries. Continuous improvements in materials, tooling, automation, and controls are expanding its use for more demanding applications requiring tight quality control. Understanding key techniques empowers manufacturers to take full advantage of thermoforming's economy, design freedom, and customization possibilities.
- Art
- Causes
- Crafts
- Dance
- Drinks
- Film
- Fitness
- Food
- الألعاب
- Gardening
- Health
- الرئيسية
- Literature
- Music
- Networking
- أخرى
- Party
- Religion
- Shopping
- Sports
- Theater
- Wellness
- IT, Cloud, Software and Technology