Waterproof Coatings: Providing Protection from Water Damage
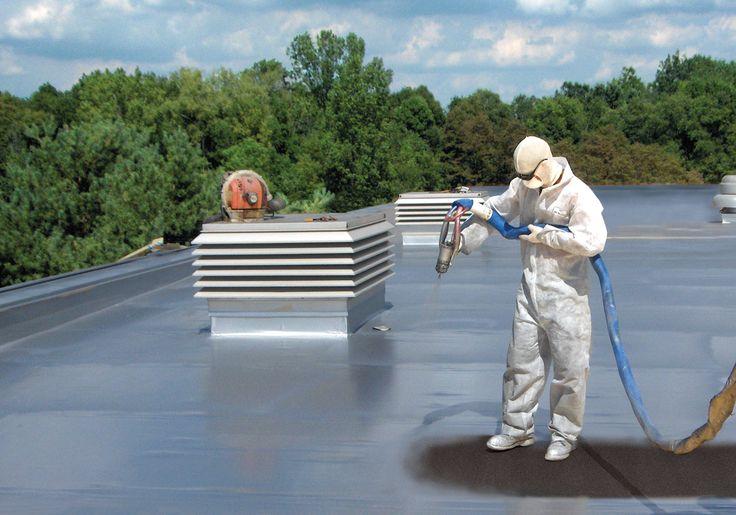
Waterproof coatings have played an essential role in protecting various substrates from damage caused by water exposure. As water poses significant risks of degradation to materials like wood, concrete, and metals, developing durable barrier treatments has been a critical area of research and development. This article explores the chemistry and applications of modern waterproofing systems used in construction, infrastructure, and other industries.
Types of Waterproof Coatings
Waterproof Coatings can generally be categorized into two main types - thin film membranes and thick film penetrating sealers. Thin film membranes form a continuous protective layer that prevents water from entering the substrate. Common thin film membranes include epoxy, polyurethane, acrylic, and asphalt emulsions that are often reinforced with fabric or fiberglass mats. Thick film penetrating sealers are formulated to penetrate deep into porous materials like concrete, masonry, and wood. Silane, siloxane, and silicone-based sealers are typical thick film formulations that fill capillaries and pores.
Durability Considerations
For waterproof coatings to perform effectively over the long-term, they must demonstrate resilience to environmental conditions that can compromise performance. Exposure to ultraviolet radiation from sunlight can degrade many polymer-based formulations over time if they lack adequate UV stabilization additives. Thermal cycling from daily and seasonal temperature fluctuations also stresses coatings and can lead to loss of adhesion or cohesion. Chemical contamination from deicing salts, pollution, and biological growth requires resistance from the coating. Proper surface preparation and application are crucial to achieving the designed service life of a waterproofing system.
Applications in Construction
In construction, waterproof coatings find widespread use in below-grade and immersed applications to protect foundations, basements, tunnels, and other subterranean structures from water intrusion. Epoxy and polyurea are common choices for their toughness and seamless application over irregular surfaces in containment structures. Polyurethane and polyurea elastomers have gained popularity for waterproofing roofs due to flexibility and extended lifetime via UV resistance. Swimming pools and fountains rely on specialized chlorinated rubber, acrylic, and epoxy formulations to provide a durable barrier without contaminating water. Coatings are also applied to shed walls, planters, and numerous other exterior surfaces around buildings.
Infrastructure Waterproofing
It play an equally important role in infrastructure to protect assets from moisture damage. Transportation structures like bridges, tunnels, parking garages, and ship decks commonly use polyurethane and polyurea systems for waterproofing structural elements and vehicle surface interfaces. Water and wastewater containment facilities employ thick elastomeric sheet membranes or spray-applied polyurea to create water-tight tank linings and digester covers. Runways, helipads, and other pavement benefit from asphalt and cementitious coatings to prevent water intrusion into subsurface layers. Specialized epoxy and polyurea formulations have even enabled waterproofing applications on dams and water retaining structures.
Conformance to Standards
Maintaining technical conformance with recognized performance standards is important to ensure waterproof coatings deliver the intended level of protection for their designed service life. Key standards include ASTM C836 for flexible waterproof coatings used under concrete, ASTM C957 for elastomeric sheet waterproofing membranes, ASTM D2240 for shore hardness/flexibility testing, and ASTM D412 for tensile strength/elongation requirements. In the European market, EN 1504 conformity is widely specified for chemical, water, vapor, and other exposure resistance parameters. Meeting voluntary standards helps verify proper quality control for the materials and builds confidence for specifiers, owners, and contractors.
Quality Application is Critical
While premium coatings formulations deliver high waterproofing effectiveness, the quality of surface preparation and application strongly influences the long-term protection provided. Proper cleaning, priming, and profile preparation are prerequisite to achieve optimal adhesion to the substrate. Coatings must be applied uniformly to the recommended wet and dry film thicknesses through spray, roller, trowel, or other methods suitable for the material and location. Adequate curing times before exposure to moisture, along with protection of the newly coated surface until fully cured, guard against premature degradation. Strict quality control monitoring and contractor certification help ensure correct installation practices are followed.
Waterproof coatings serve as a vital line of defense against moisture damage across diverse structures and assets. Choosing the right formulation for a given substrate and exposure conditions, coupled with precision application methods, provides durable barriers to protect investments for decades. Ongoing innovations continue to expand the capabilities and performance of modern waterproofing systems. When properly specified and installed to conform with standards, these coatings reliably safeguard infrastructure from the costly effects of water intrusion and deterioration.
Get More Insights on Waterproof Coatings
- Art
- Causes
- Crafts
- Dance
- Drinks
- Film
- Fitness
- Food
- Games
- Gardening
- Health
- Home
- Literature
- Music
- Networking
- Other
- Party
- Religion
- Shopping
- Sports
- Theater
- Wellness
- IT, Cloud, Software and Technology