How does the wet tissue machine ensure uniform size of the wipes?
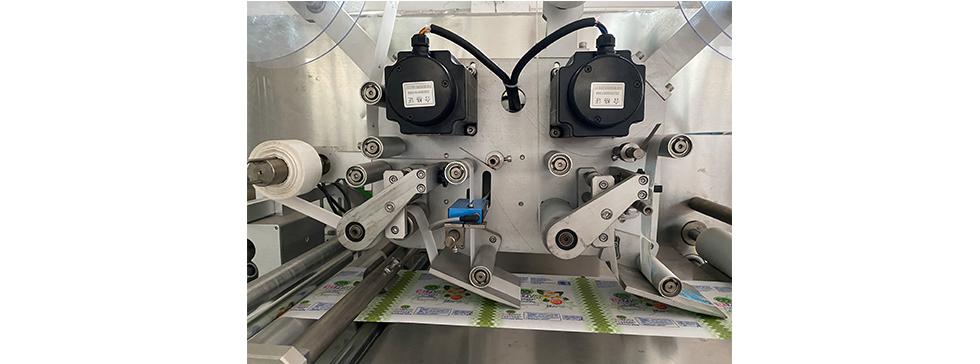
The wet tissue machine ensures the uniform size of wipes through a combination of precise engineering, automated control systems, and quality mechanisms integrated into its design.
Here are the key processes that contribute to this uniformity:
-
Material Feeding System: The fabric roll is fed into the machine under constant tension using a tension control system. This ensures consistent material flow, preventing distortions that could affect wipe dimensions.
-
Cutting Mechanism: High-precision rotary cutters or guillotine blades are used to cut the fabric into individual wipes. These cutting systems are calibrated to ensure accurate and consistent dimensions, maintaining uniformity throughout the production process.
-
Folding Unit: The machine uses advanced folding mechanisms to fold the wipes uniformly. Techniques like "Z-fold" or "C-fold" are controlled by pre-set configurations to ensure each wipe is folded to the exact specifications.
-
Wetness Distribution: The system evenly distributes the cleaning solution over the fabric to maintain consistent moisture levels across all wipes. This avoids shrinkage or expansion that could affect wipe size.
-
Sensors and Automation: Modern wet tissue machines use sensors and automated controls to monitor the fabric's alignment, cutting accuracy, and folding precision in real time. Any deviations are detected and corrected immediately.
-
Stacking and Packaging: Uniform stacking and packaging mechanisms further ensure that each wipe meets size standards. Quality checks at this stage confirm consistency before the final product is sealed.
By combining these precise and automated processes, wet tissue machines deliver high-quality, uniformly sized wipes suitable for consumer and industrial applications.
- Art
- Causes
- Crafts
- Dance
- Drinks
- Film
- Fitness
- Food
- Games
- Gardening
- Health
- Home
- Literature
- Music
- Networking
- Other
- Party
- Religion
- Shopping
- Sports
- Theater
- Wellness
- IT, Cloud, Software and Technology