Thin Film Sputtering Market by Type, Material, and Application: A Comprehensive Overview
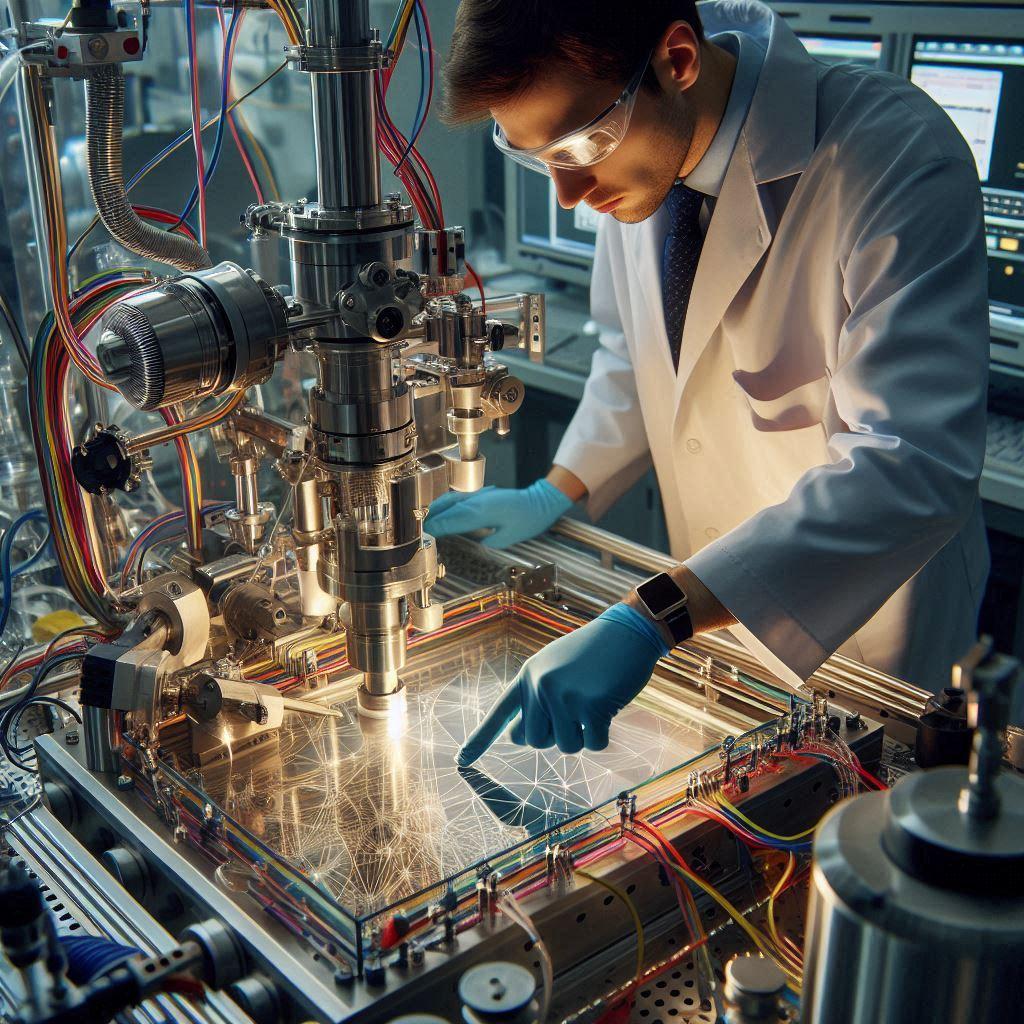
The thin film sputtering market is a key component of modern manufacturing processes, with its applications spanning multiple industries, including electronics, optoelectronics, medical devices, and more. Sputtering, a widely used technique for depositing thin films of materials onto substrates, is evolving with the development of new types of sputtering systems and target materials. This article explores the key segments of the thin film sputtering market, including type, target material, and application, shedding light on the current trends and future outlook.
Thin Film Sputtering Market by Type
Thin film sputtering technologies are the core of the market and are evolving rapidly to meet the demands of precision manufacturing across various industries. The following are the primary types of sputtering systems used in the thin film deposition process:
Diode Sputtering Diode sputtering is one of the simplest sputtering methods, using a DC (direct current) power supply to generate a plasma that dislodges target atoms. It is particularly useful for applications requiring high-quality thin films, such as in semiconductors, solar cells, and optical coatings. However, it is limited by its ability to work with only conductive materials.
DC Sputtering DC sputtering involves using direct current to generate the plasma required for the sputtering process. This technique is commonly used in the deposition of metals onto substrates. The DC sputtering process is known for its straightforward approach, cost-effectiveness, and efficiency in producing dense, high-quality films. It is widely used in semiconductor manufacturing and coatings for electronic components.
RF Sputtering (Radio Frequency Sputtering) RF sputtering uses alternating current (AC) in the form of radio frequencies to generate plasma, which makes it suitable for sputtering non-conductive materials. This method is ideal for applications where dielectric films, such as ceramic coatings or thin film insulators, are needed. RF sputtering is also frequently used in optoelectronics and solar energy applications.
Magnetron Sputtering Magnetron sputtering is one of the most commonly used sputtering techniques due to its high efficiency. By applying magnetic fields near the target material, it increases the ionization of the sputtered particles, making the process more effective. It is widely used for producing high-quality thin films in semiconductor devices, solar panels, and decorative coatings.
Reactive Sputtering Reactive sputtering involves introducing reactive gases (e.g., oxygen or nitrogen) into the sputtering chamber to react with the sputtered material, resulting in the formation of compounds or alloys. This process is essential for producing thin films with specific properties, such as oxides, nitrides, or carbide coatings. Reactive sputtering finds applications in the production of hard coatings, optical coatings, and thin-film semiconductors.
Ion Sputtering Ion sputtering utilizes ionized particles (often derived from a gas) to bombard the target material, causing the ejection of material atoms. This method provides higher energy to the sputtered material, improving the quality and adhesion of thin films. Ion sputtering is used primarily for high-performance coatings and specialized applications in electronics and optics.
Download PDF Brochure @ https://www.marketsandmarkets.com/pdfdownloadNew.asp?id=226582974
Thin Film Sputtering Market by Target Material
The choice of target material plays a crucial role in determining the properties of the thin films. The thin film sputtering market includes various target materials, each offering unique characteristics for specific applications. These are the main target materials used in thin film sputtering:
Metals Metal targets are among the most commonly used in thin film sputtering due to their excellent conductivity and ease of sputtering. Materials such as gold, silver, copper, aluminum, and titanium are widely employed in the production of thin metal films used in semiconductor components, electrical contacts, and conductive coatings.
Compounds Compound materials, such as oxides, nitrides, and carbides, are increasingly being used in sputtering to create thin films with specialized properties, such as enhanced durability, resistance to corrosion, and optical characteristics. This category includes materials like aluminum oxide (Al2O3), titanium nitride (TiN), and zinc oxide (ZnO), which are often used in optical coatings, semiconductors, and protective coatings.
Alloys Alloy targets are mixtures of two or more metals that are used for applications requiring specific mechanical, electrical, or thermal properties. Common alloys used in sputtering include stainless steel, brass, and aluminum alloys. These materials are essential for creating robust thin films used in aerospace, automotive, and electronics applications.
Semiconductor Materials Semiconductor materials such as silicon, germanium, and gallium arsenide are essential for producing thin films in the electronics and semiconductor industries. These materials are used to manufacture integrated circuits, solar cells, and microelectronic components, where precise thin film deposition is critical.
Others (Dielectric, Polymers, Organic Materials) Other target materials include dielectric materials, polymers, and organic materials. These are used for applications in energy storage, flexible electronics, and organic photovoltaic cells. Dielectric materials are commonly used for insulation in electronic devices, while organic materials are crucial for emerging technologies like organic light-emitting diodes (OLEDs) and organic solar cells.
Thin Film Sputtering Market by Application
The thin film sputtering process has a wide range of applications across various industries, each benefiting from thin films’ unique properties, such as conductivity, durability, and optical characteristics. The key applications include:
Image Sensors Thin film sputtering plays a critical role in the production of image sensors used in cameras, smartphones, and other imaging devices. Sputtered thin films are used to create highly sensitive layers for detecting light and converting it into electrical signals. The market for image sensors is expected to grow as demand for high-quality imaging continues to rise.
Electronics & Semiconductors Sputtering is essential in the electronics and semiconductor industries for the deposition of conductive and insulating thin films. It is used in the manufacturing of microchips, transistors, capacitors, and other semiconductor components, where precision and quality are paramount. As the demand for miniaturized electronics increases, the role of thin film sputtering continues to expand.
Optoelectronics Optoelectronics combines optical and electronic properties and is used in devices like light-emitting diodes (LEDs), solar cells, and laser diodes. Thin film sputtering is key to creating the functional coatings and layers needed for these devices. The growth of renewable energy sources, especially solar power, is driving the demand for sputtered thin films in the optoelectronics sector.
Wearable Devices The rise of wearable devices, such as fitness trackers, smartwatches, and health monitors, has led to an increased demand for thin film sputtering. These devices require durable, lightweight, and flexible coatings that sputtering can provide. The wearable devices segment is expected to continue its growth trajectory as consumer interest in health and fitness technology grows.
Optics Thin film sputtering is commonly used in optics to produce coatings for lenses, mirrors, and other optical devices. These coatings enhance optical properties such as reflection, transmission, and absorption. As the demand for high-performance optics in industries like telecommunications, photography, and astronomy grows, the sputtering market for optics will also expand.
Medical Devices Thin films are used in medical devices for applications such as implants, biosensors, and diagnostic equipment. Sputtered coatings can enhance the biocompatibility, durability, and functionality of medical devices. As the medical device industry continues to innovate, sputtering technologies are expected to play a key role in manufacturing high-performance, reliable devices.
Others Additional applications of thin film sputtering include decorative coatings, hard coatings for wear resistance, and coatings for magnetic storage devices. As new technologies emerge, the range of applications for thin film sputtering continues to grow, driven by its versatility and ability to create tailored thin films for specialized functions.
About MarketsandMarkets™
MarketsandMarkets™ is a blue ocean alternative in growth consulting and program management, leveraging a man-machine offering to drive supernormal growth for progressive organizations in the B2B space. We have the widest lens on emerging technologies, making us proficient in co-creating supernormal growth for clients.
The B2B economy is witnessing the emergence of $25 trillion of new revenue streams that are substituting existing revenue streams in this decade alone. We work with clients on growth programs, helping them monetize this $25 trillion opportunity through our service lines - TAM Expansion, Go-to-Market (GTM) Strategy to Execution, Market Share Gain, Account Enablement, and Thought Leadership Marketing.
Built on the ’GIVE Growth’ principle, we work with several Forbes Global 2000 B2B companies - helping them stay relevant in a disruptive ecosystem. Our insights and strategies are molded by our industry experts, cutting-edge AI-powered Market Intelligence Cloud, and years of research. The KnowledgeStore™ (our Market Intelligence Cloud) integrates our research, facilitates an analysis of interconnections through a set of applications, helping clients look at the entire ecosystem and understand the revenue shifts happening in their industry.
To find out more, visit www.MarketsandMarkets™.com or follow us on Twitter, LinkedIn and Facebook.
Contact:
Mr. Aashish Mehra
MarketsandMarkets™ INC.
630 Dundee Road
Suite 430
Northbrook, IL 60062
USA : 1-888-600-6441
- Art
- Causes
- Crafts
- Dance
- Drinks
- Film
- Fitness
- Food
- Jogos
- Gardening
- Health
- Início
- Literature
- Music
- Networking
- Outro
- Party
- Religion
- Shopping
- Sports
- Theater
- Wellness
- IT, Cloud, Software and Technology