Cigar Cutters Manufacturing Plant Project Report 2025: Cost, Process and Market Trends
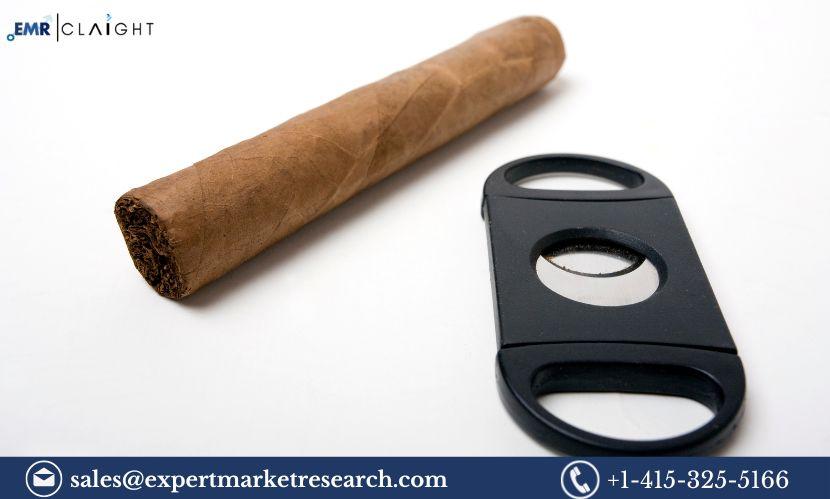
Introduction
The Cigar Cutters Manufacturing Plant Project Report outlines the process of setting up a facility dedicated to the production of high-quality cigar cutters. Cigar cutters are essential tools for cigar enthusiasts, providing an easy and precise way to trim the tip of a cigar before smoking. These cutters come in various forms, including guillotine cutters, punch cutters, v-cutters, and scissors, each offering a different cutting style depending on the smoker's preference. With a growing global market for premium cigars, the demand for high-quality cigar cutters is on the rise. This report serves as a guide for entrepreneurs and investors interested in establishing a cigar cutter manufacturing plant, detailing the required raw materials, production processes, machinery, safety standards, and market opportunities.
Market Overview
The cigar industry has seen steady growth, particularly among high-end consumers and cigar connoisseurs. This growth is driving demand for premium cigar accessories, with cigar cutters being one of the essential items for the smoking experience. According to market trends, premium cigar sales, especially in regions such as the United States and Europe, are on the rise, which increases the need for precision-engineered cigar cutters.
Cigar cutters are typically made from stainless steel, aluminium, and plastic, with some high-end models incorporating carbon fibre or titanium. As smoking culture becomes more refined, consumers are increasingly looking for cutters that offer not only functionality but also style and durability.
Get a Free Sample Report with Table of Contents@
Types of Cigar Cutters
There are several types of cigar cutters, each designed to cater to different preferences:
1. Guillotine Cutters
These cutters are the most common and feature a single or double blade that slices the end of the cigar. They are known for providing a clean, straight cut.
2. Punch Cutters
A punch cutter creates a small hole in the cigar's cap, providing a smoother, less intrusive cut, often favoured by smokers who prefer a tighter draw.
3. V-Cutters
A V-cutter produces a v-shaped cut at the tip of the cigar, which many smokers believe enhances the draw by exposing more of the cigar’s filler.
4. Scissors
Cigar scissors are designed for precision cutting, often used for larger or more robust cigars. These cutters have sharp, curved blades and are typically made of high-quality steel.
Manufacturing Process
The manufacturing of cigar cutters involves several stages, from raw material sourcing to the final product's assembly and packaging. Below is an outline of the key processes involved:
1. Raw Material Procurement
The primary materials used in cigar cutter production include:
- Stainless Steel: The most common material for the blades due to its strength, durability, and corrosion resistance.
- Aluminium or Zinc Alloys: Used for the cutter's body, ensuring lightweight but sturdy construction.
- Plastic or Rubber: Often used for grips or housing to provide comfort and aesthetic appeal.
- Titanium or Carbon Fibre: Used in high-end models for lightweight and strength properties.
Raw materials must meet industry standards for durability and precision, as the quality of the cutter depends heavily on the materials used.
2. Cutting and Shaping
Once the raw materials are sourced, the production process begins with the cutting and shaping of components. For the blades, this process typically involves CNC (Computer Numerical Control) machines or laser cutters to achieve the necessary sharpness and precision. Stamping presses or die cutters are used for creating the bodies and frames.
3. Blade Grinding and Sharpening
After the initial shaping, the blades are ground and sharpened to a razor-sharp edge. This is a critical step, as the effectiveness of the cigar cutter depends on the sharpness of the blade. Specialized grinding wheels or diamond-coated abrasives are used to ensure the blades meet the desired level of sharpness.
4. Assembly
The next step is the assembly of the cutter. This involves attaching the blades to the frame or housing. For guillotine cutters, this may involve a double-blade mechanism, while punch cutters require a rotating punch and housing assembly. V-cutters involve a specially designed mechanism that creates a “V” shape on the cigar cap.
5. Quality Control and Testing
Once the cutters are assembled, they undergo rigorous testing to ensure functionality and safety:
- Cutting Test: Each cutter is tested for sharpness, smoothness of action, and ease of use.
- Durability Test: The cutter is subjected to repeated usage to ensure that the blades remain sharp and the mechanism functions smoothly.
- Safety Test: Ensures that the cutter does not have any sharp edges that could pose a risk to the user.
6. Finishing and Packaging
After successful testing, the cutters are finished with polishing, anodising, or coating for added durability and aesthetic appeal. The final product is then carefully packaged, usually in protective boxes or cases, ready for distribution.
Machinery and Equipment Required
A cigar cutter manufacturing plant requires various machines to handle different stages of the production process:
- CNC Machines: For precise cutting and shaping of blades.
- Laser Cutters: For cutting complex shapes or designs in metal parts.
- Stamping Presses: Used to shape the cutter body and components.
- Grinders and Polishers: For sharpening and finishing the blades.
- Assembly Fixtures: To streamline the assembly of the cutter.
- Packaging Machines: For packaging the final products into boxes.
Safety and Quality Standards
Manufacturers of cigar cutters must comply with industry safety and quality standards to ensure that their products are both functional and safe to use. Key considerations include:
- Blade Safety: Sharp blades must be handled with care during manufacturing and packaging.
- Material Quality: The materials used must meet safety standards to prevent breakage or malfunction during use.
- Durability: The cutters must be able to withstand frequent use without degradation in performance.
- Ergonomics: Comfort is important in design to ensure the cutters are user-friendly.
Market Demand and Growth Potential
The global market for cigar accessories, including cigar cutters, is expected to grow as the popularity of premium cigars continues to rise. The rise of cigar smoking among connoisseurs and the growing trend of premium product purchases among affluent consumers is expected to drive demand for high-quality cigar cutters.
Key Consumer Markets:
- North America: The United States is a major consumer of premium cigars, thus driving the demand for cigar cutters.
- Europe: Countries like Germany, Spain, and the UK are significant markets for both cigars and cigar accessories.
- Asia: Emerging markets, especially in countries like Japan and China, are witnessing an increase in cigar consumption.
Opportunities in the Market:
- Customization: There is a growing demand for custom-designed cigar cutters, which offers an opportunity for manufacturers to cater to niche markets.
- Luxury Models: High-end cigar cutters, made from premium materials like titanium or carbon fibre, have significant market potential.
- Branding and Marketing: Developing a strong brand presence and marketing strategy will be crucial to success in this competitive market.
Investment and Financial Considerations
1. Initial Investment
Setting up a cigar cutter manufacturing plant requires substantial investment in machinery, raw materials, factory setup, and compliance with safety regulations. Depending on the scale of the operation, initial costs can range from several hundred thousand to millions of dollars.
2. Operational Costs
Ongoing costs will include raw material procurement, wages, energy bills, maintenance of machinery, and marketing expenses. The plant will also need to comply with local regulations regarding safety, environmental impact, and labour standards.
3. Profit Margins
Cigar cutters can be sold at a significant markup, especially in premium or luxury segments. While the initial manufacturing costs can be high, the potential for profit is substantial, especially with strong branding and market positioning.
FAQ
1. What materials are used to make cigar cutters?
Cigar cutters are typically made from stainless steel, aluminium, plastic, and in some cases, carbon fibre or titanium for premium models.
2. What are the different types of cigar cutters?
The main types of cigar cutters include guillotine cutters, punch cutters, v-cutters, and scissors, each offering a unique cutting style.
3. How sharp should a cigar cutter be?
A cigar cutter must have razor-sharp blades to ensure a clean, smooth cut. The sharper the blade, the better the cutter will perform in preventing the cigar from tearing.
4. What is the function of a punch cutter?
A punch cutter creates a small hole in the cap of the cigar. This offers a different smoking experience and is often preferred by smokers who enjoy a tighter draw.
5. Can a cigar cutter be used on all types of cigars?
Cigar cutters are designed to cut most cigars, but larger cigars may require larger cutters or scissors. Punch cutters are better suited for smaller ring gauge cigars.
6. How do I maintain my cigar cutter?
To maintain a cigar cutter, keep the blades clean and sharp. Regularly wipe the cutter to remove any tobacco or debris, and store it in a dry, safe place.
Media Contact:
Company Name: Claight Corporation
Contact Person: Lewis Fernandas, Corporate Sales Specialist — U.S.A.
Email: sales@expertmarketresearch.com
Toll Free Number: +1–415–325–5166 | +44–702–402–5790
Address: 30 North Gould Street, Sheridan, WY 82801, USA
Website: www.expertmarketresearch.com
Aus Site: https://www.expertmarketresearch.com.au
- Art
- Causes
- Crafts
- Dance
- Drinks
- Film
- Fitness
- Food
- الألعاب
- Gardening
- Health
- الرئيسية
- Literature
- Music
- Networking
- أخرى
- Party
- Religion
- Shopping
- Sports
- Theater
- Wellness
- IT, Cloud, Software and Technology