Propanal Manufacturing Plant Project Report: Comprehensive Insights
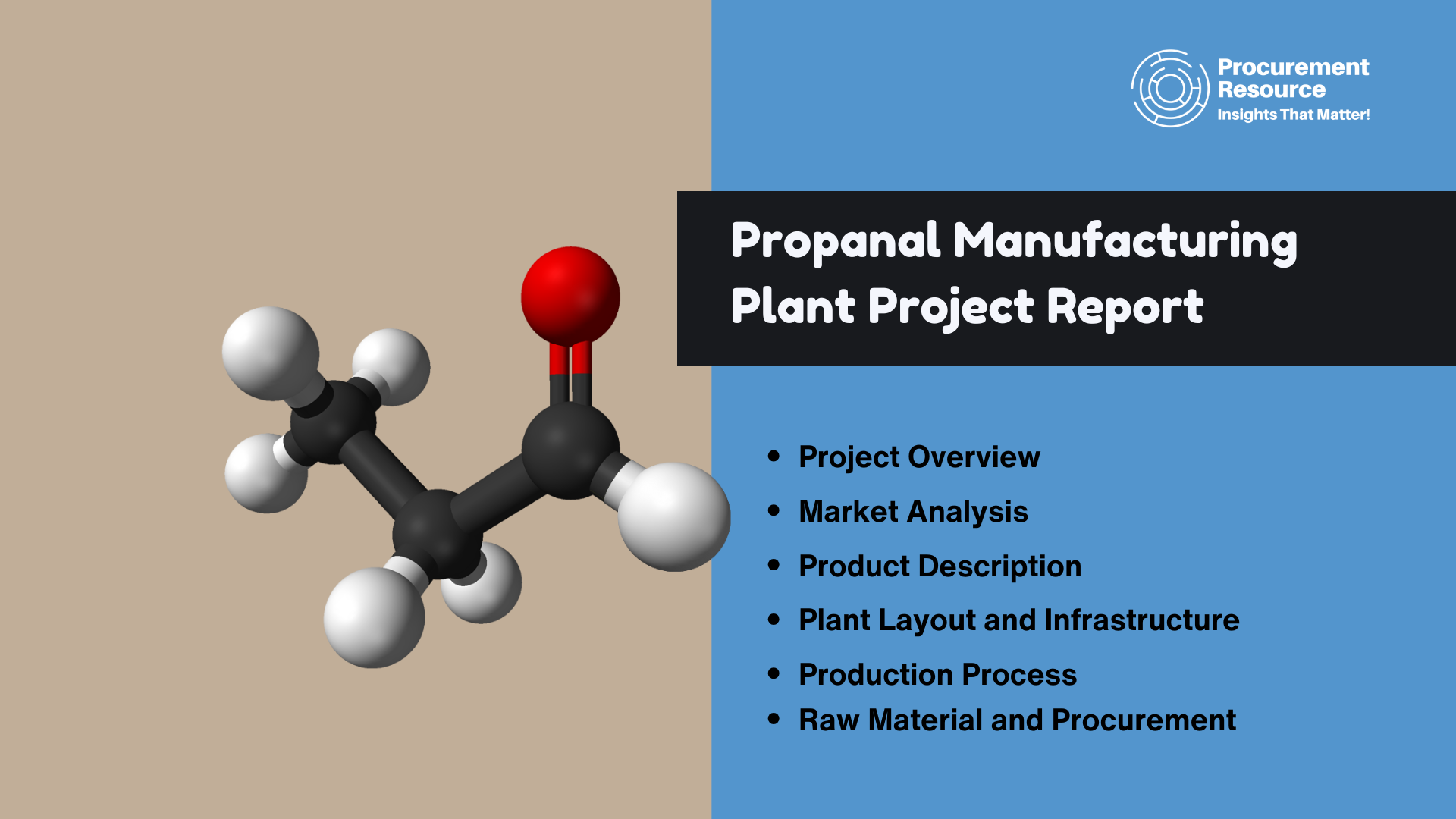
Propanal, commonly known as propionaldehyde, is an important aldehyde compound with wide-ranging applications in the chemical industry. It serves as a precursor for various downstream products, including pharmaceuticals, agrochemicals, flavors, fragrances, and plasticizers. Establishing a Propanal Manufacturing Plant Project Report requires a detailed understanding of raw material sourcing, production technologies, safety considerations, market dynamics, and regulatory compliance. This project report provides an in-depth analysis of the key aspects involved in planning, constructing, and operating a propanal manufacturing facility.
Overview of Propanal and Its Applications
Propanal (CH3CH2CHO) is a volatile, colorless liquid characterized by its pungent, aldehyde-like odor. It is a valuable intermediate in the production of chemicals that find use in a variety of industries:
- Pharmaceuticals:
Propanal is used in the synthesis of certain pharmaceutical intermediates, including active ingredients in drugs and specialty compounds for health-related products. - Agrochemicals:
The agricultural sector relies on propanal derivatives to produce fungicides, insecticides, and herbicides. - Flavors and Fragrances:
Due to its aldehyde functional group, propanal serves as a building block for various flavor and fragrance components, enhancing the sensory appeal of consumer goods. - Plastics and Polymers:
Propanal is used in the production of plasticizers, which improve the flexibility and durability of polymer products.
Raw Materials and Feedstock
The primary feedstocks for propanal production are propylene and synthesis gas (syngas), a mixture of hydrogen (H2) and carbon monoxide (CO). Ensuring a stable and cost-effective supply of these raw materials is crucial for plant operations.
- Propylene:
Derived from petroleum refining and steam cracking processes, propylene serves as the primary starting material for hydroformylation reactions that produce propanal. - Synthesis Gas (Syngas):
Produced from natural gas reforming or partial oxidation of hydrocarbons, syngas provides the carbon monoxide and hydrogen required for the hydroformylation process. - Catalysts and Process Aids:
The production process relies on catalysts, such as rhodium or cobalt complexes, to drive the hydroformylation reaction efficiently. Optimized catalyst systems enhance yield, selectivity, and overall process economics.
Production Process and Technologies
Propanal is primarily manufactured through the hydroformylation of propylene, also known as the oxo process. This well-established technology offers high efficiency and scalability. Key steps in the production process include:
-
Hydroformylation Reaction:
Propylene reacts with carbon monoxide and hydrogen in the presence of a homogeneous catalyst, typically a rhodium or cobalt complex. The reaction yields propanal as the primary product, along with smaller amounts of higher aldehydes. -
Separation and Purification:
The crude product stream is subjected to separation processes to remove unreacted propylene, syngas, and by-products. Distillation is commonly employed to purify the propanal, ensuring it meets industry standards for downstream applications. -
Recycling of Feedstocks and Catalysts:
Unreacted gases and catalysts are often recycled back into the process to improve efficiency and reduce waste, thereby lowering overall production costs.
Safety Considerations and Hazard Management
Propanal production involves the handling of flammable gases, reactive chemicals, and potentially hazardous catalysts. Safety measures are critical to protect workers, equipment, and the environment.
-
Process Safety and Monitoring:
Advanced process control systems, including real-time monitoring of temperature, pressure, and flow rates, ensure stable and safe operations. Automated shutdown systems and interlocks prevent accidents during deviations. -
Hazardous Material Handling:
Proper storage and handling protocols for feedstocks and intermediates minimize risks associated with leaks, fires, and chemical exposure. Specialized storage tanks, gas detectors, and emergency ventilation systems contribute to a safer plant environment. -
Regular Maintenance and Training:
Scheduled maintenance of equipment, combined with regular employee training programs, ensures that all personnel are well-versed in safety procedures and emergency response protocols.
Market Trends and Demand Drivers
Understanding the demand for propanal and its derivatives is essential for determining plant capacity, product portfolio, and target markets.
-
Growing Demand in Pharmaceuticals and Agrochemicals:
As the global population continues to grow, the demand for crop protection products and pharmaceutical intermediates rises, driving the need for propanal as a key raw material. -
Expansion in Flavors and Fragrances Industry:
The increasing popularity of natural and synthetic flavors and fragrances in food, beverages, and personal care products contributes to steady demand for propanal derivatives. -
Emerging Applications in Specialty Chemicals:
Propanal’s versatility has led to its adoption in emerging chemical applications, such as advanced polymers and bio-based materials. This opens new revenue streams for manufacturers and supports long-term market growth. -
Regional Growth Dynamics:
The Asia-Pacific region, in particular, has seen significant growth in chemical manufacturing, with rising demand for propanal from both domestic and export-oriented industries. North America and Europe continue to represent stable markets, driven by innovation and established end-use industries.
Cost Structure and Financial Considerations
Establishing a propanal manufacturing plant involves substantial capital and operating expenses. A thorough cost analysis helps determine the project’s economic feasibility and long-term profitability.
- Capital Expenditures (CAPEX):
- Construction and installation of reactors, distillation columns, and auxiliary equipment.
- Investment in safety systems, storage tanks, and utilities infrastructure.
- Licensing fees for proprietary catalysts and process technologies.
- Operating Expenses (OPEX):
- Procurement of feedstocks (propylene and syngas) and catalysts.
- Utility costs, including energy consumption for heating, cooling, and distillation.
- Maintenance, labor, and regulatory compliance costs.
- Revenue and Profitability Analysis:
- Pricing of propanal is influenced by raw material costs, production efficiency, and market demand.
- Diversifying product lines and targeting high-value end-use applications can improve margins and overall profitability.
Environmental and Regulatory Compliance
Propanal manufacturing must adhere to stringent environmental regulations and sustainability standards. Implementing advanced process technologies and waste management systems helps minimize environmental impact.
- Emission Controls and By-Product Management:
- Installation of scrubbers, flare systems, and catalytic converters reduces greenhouse gas emissions and ensures compliance with local and international environmental laws.
- Efficient recovery and recycling of by-products, unreacted gases, and spent catalysts improve resource utilization and reduce waste.
- Sustainability Initiatives:
- Integrating renewable feedstocks and improving energy efficiency supports the global push for greener chemical production.
- Participating in industry certification programs and adopting sustainable practices enhances the plant’s reputation and marketability.
Building a propanal manufacturing plant involves addressing key technical, economic, and regulatory challenges. By leveraging established production technologies, maintaining a focus on safety and environmental standards, and aligning with market demand, manufacturers can establish a successful, sustainable operation in the growing market for propanal and its derivatives.
Contact Us:
Company Name: Procurement Resource
Contact Person: Leo Frank
Email: sales@procurementresource.com
Toll-Free Numbers:
- USA & Canada: +1 307 363 1045
- UK: +44 7537171117
- Asia-Pacific (APAC): +91 1203185500
Address: 30 North Gould Street, Sheridan, WY 82801, USA
- Art
- Causes
- Crafts
- Dance
- Drinks
- Film
- Fitness
- Food
- Jogos
- Gardening
- Health
- Início
- Literature
- Music
- Networking
- Outro
- Party
- Religion
- Shopping
- Sports
- Theater
- Wellness
- IT, Cloud, Software and Technology