E-Coat: An Environmentally-Friendly Coating Process for Automotive and Other Metal Parts
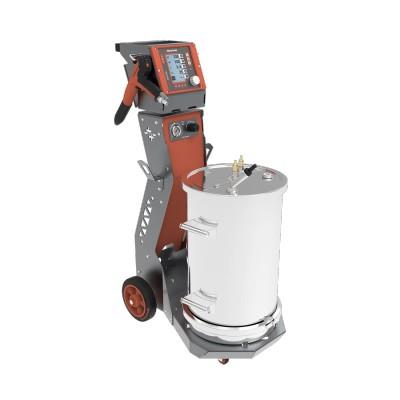
What is E-Coat?
E-coat, also known as electrophoretic coating or electrocoat, is a process where a paint material combines with an electric charge to deposit and bond with a metal substrate. In this electrodeposition process, a part is immersed in a water-based solution containing paint particles. An electric current is passed through the solution, causing the paint pigments to migrate and adhere to the part in a uniform, accurately controlled film build.
History and Development
The foundation of modern E-Coat technology was laid in the 1940s. During World War II, researchers at General Motors explored using an electrical current to quickly coat artillery shells and other metal items for corrosion protection. In the years following the war, the automotive industry adopted E-coat for applying primers to auto bodies. The process provided a more consistent coating compared to conventional spray methods. Advances in E-coat materials and equipment over the subsequent decades led to its widespread use in industries like appliances, heavy machinery, and construction.
Coating Properties and Benefits
Compared to traditional spray primers, E-coat provides excellent film thickness uniformity, edge coverage, and concealment of surface defects. The coatings achieve full film cure within 5-10 minutes after application using low-temperature baking. E-coat films are highly resistant to corrosion, chipping, abrasion, and fading. They also function as an effective electrically insulating barrier on cars, trucks, and other conductive metal structures. From an environmental perspective, E-coat is a low-VOC process that emits negligible amounts of toxins compared to spray primers. It allows for easy recycling of overspray material back into the tank.
Applications in Automotive Assembly
Today, E-coat is universally employed by vehicle manufacturers globally to apply cathodic electrophoretic primers. In a typical automotive coating line, auto bodies sequentially undergo pretreatment wash, E-coat application, and curing before proceeding to other finishing steps. The E-coat primer acts as a base for the topcoat system and protects the metal from corrosion for the vehicle's lifetime. Other common auto components given E-coat include bumpers, suspension parts, and various small stamped metal parts. The consistent, void-free primer layer assures long-term corrosion resistance essential for safety-related applications.
Use in Appliance Manufacturing
White goods like refrigerators, washing machines, and air conditioners rely extensively on E-coat technology. Intricate assemblies containing countless small folded and formed metal parts need full, defect-free coverage that E-coat delivers efficiently. Major home appliance manufacturers electrodeposit epoxy-based or polyester-based white or grey E-coat primers on steel cabinets prior to powder topcoating. This protects the metal interiors and exteriors from corrosion during the product's 15-20 year lifespan. E-coat's low-energy curing also fits well with appliance makers' stringent production schedules.
Growth in Industrial Equipment Segments
As concerns about environmental regulations and sustainability increase, industrial segments are adopting E-coat for its green profile. Businesses producing transportation and materials handling equipment, agricultural and construction machinery, power tools, and metal consumer durables have incorporated electrodeposition coating lines. E-coating components for off-road vehicles, cranes, farm implements and infrastructure ensures long-lasting protective finishes. Some industrial applications also utilize E-coat as a corrosion-inhibiting sealer on parts like fasteners and hardware prior to packaging. With its consistent results and eco-friendly process attributes, E-coat looks poised for further gains across multiple manufacturing verticals.
Future Technology Advances
Researchers continue enhancing E-coat formulations and application methods. Waterborne systems that reduce volatile organic compound emissions are increasingly common. Powder E-coat systems using an E-coat resin suspended in an aqueous solution followed by powder bonding allows for lower-temperature curing. Novolac epoxy resins improve corrosion and chemical resistance. Advances in equipment automation and controls aid optimizing film thickness and current efficiency. Looking ahead, the next technological milestones may include innovative resin chemistries, non-aqueous E-coat dispersions, and digital monitoring systems for real-time process diagnostics and quality management. Such refinements will extend E-coat's prospect of delivering attractive finished parts economically and with minimal environmental impact.
In an E-coat has established itself as an essential metal finishing process across many major manufacturing sectors thanks to its versatile corrosion protection, low emissions profile and consistent coating performance. Advancements aim to further strengthen its credentials as an environmentally-friendly coating technology supported by reliable processes and enabling technologies. E-coat continues powering the production of durable, attractively finished metal components globally.
Get more insights on, E-Coat
Get This Report in English Language: E-Coat
Get This Report in Japanese Language: Eコート
Get This Report in Korean Language: 전자 코트
About Author:
Money Singh is a seasoned content writer with over four years of experience in the market research sector. Her expertise spans various industries, including food and beverages, biotechnology, chemical and materials, defense and aerospace, consumer goods, etc. (https://www.linkedin.com/in/money-singh-590844163)
- Art
- Causes
- Crafts
- Dance
- Drinks
- Film
- Fitness
- Food
- Games
- Gardening
- Health
- Home
- Literature
- Music
- Networking
- Other
- Party
- Religion
- Shopping
- Sports
- Theater
- Wellness
- IT, Cloud, Software and Technology