Automotive Bearing Market: Key Materials and Manufacturing Techniques
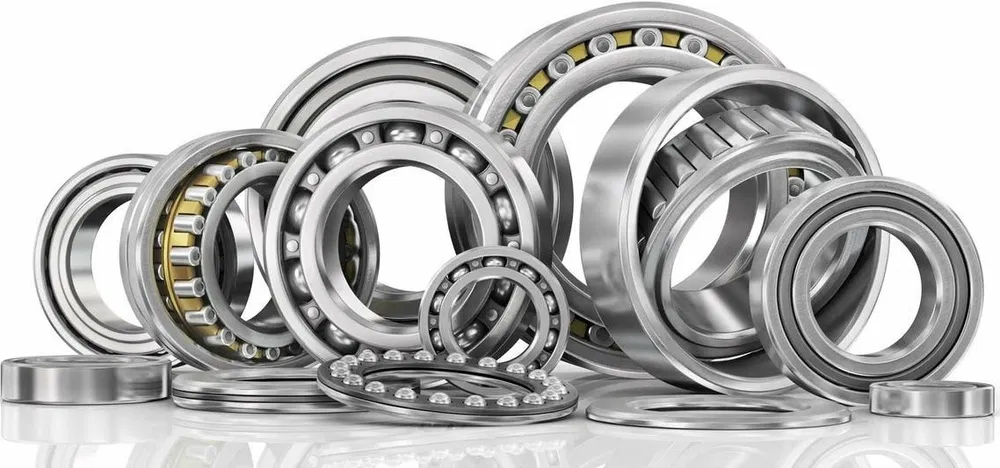
Introduction
The automotive bearing market relies on high-performance materials and advanced manufacturing techniques to meet the growing demands of modern vehicles. Bearings play a critical role in reducing friction, enhancing efficiency, and improving vehicle durability. Innovations in material science and precision engineering have led to the development of bearings that offer higher strength, lower weight, and enhanced thermal resistance. This article explores the key materials used in automotive bearings and the latest manufacturing techniques shaping the industry.
Key Materials Used in Automotive Bearings
1. Steel Bearings: The Industry Standard
Steel remains the most widely used material in automotive bearings due to its strength, durability, and cost-effectiveness. Common types include:
-
High-Carbon Chromium Steel (52100 Steel) – Provides excellent hardness and wear resistance.
-
Stainless Steel – Offers corrosion resistance and is used in harsh environmental conditions.
-
Case-Hardened Steel – Enhances toughness while maintaining a hard surface for extended lifespan.
2. Ceramic Bearings: High-Performance Applications
Ceramic bearings, particularly silicon nitride (Si₃N₄) and zirconia (ZrO₂), are gaining popularity in electric vehicles (EVs) and high-performance applications due to:
-
Lightweight properties, reducing overall vehicle weight.
-
Higher thermal resistance, making them ideal for high-speed electric motors.
-
Lower friction, leading to improved energy efficiency and reduced heat generation.
3. Hybrid Bearings: Combining the Best of Both Worlds
Hybrid bearings integrate ceramic rolling elements with steel raceways, offering benefits such as:
-
Improved durability and extended lifespan.
-
Reduced friction and operational noise.
-
Better performance in extreme temperature and speed conditions.
4. Polymer and Composite Bearings: A Growing Trend
Innovations in polymer-based bearings have introduced materials like PTFE (Polytetrafluoroethylene) and PEEK (Polyetheretherketone), which provide:
-
Self-lubricating properties, reducing the need for external lubrication.
-
Corrosion resistance, making them ideal for extreme weather conditions.
-
Lightweight characteristics, improving fuel efficiency in combustion engine vehicles.
Advanced Manufacturing Techniques in Automotive Bearings
1. Precision Machining and Grinding
Modern CNC (Computer Numerical Control) machining and precision grinding ensure:
-
Tight tolerances for high-performance bearings.
-
Enhanced surface finishes, reducing friction and wear.
-
Automated quality control for consistent manufacturing.
2. Heat Treatment for Enhanced Durability
Heat treatment processes such as induction hardening, carburizing, and nitriding improve bearing longevity by:
-
Increasing surface hardness while maintaining a tough core.
-
Enhancing resistance to wear and fatigue under extreme loads.
-
Optimizing material microstructure for high-stress applications.
3. 3D Printing and Additive Manufacturing
Advancements in additive manufacturing are enabling the production of customized and lightweight bearing designs. Benefits include:
-
Rapid prototyping for innovative bearing geometries.
-
On-demand production, reducing lead times and inventory costs.
-
Material efficiency, minimizing waste in production.
4. Coatings and Surface Treatments
To improve bearing performance and longevity, manufacturers apply specialized coatings such as:
-
Diamond-like carbon (DLC) coatings, which reduce wear and friction.
-
PTFE coatings for self-lubricating properties.
-
Anti-corrosion coatings for harsh environmental conditions.
5. Automation and AI-Driven Manufacturing
With the rise of Industry 4.0, AI and robotics are transforming bearing production through:
-
Automated assembly lines for high precision and efficiency.
-
AI-driven defect detection and quality control.
-
Data-driven predictive maintenance for manufacturing equipment.
Future Trends in Automotive Bearing Materials and Manufacturing
-
Increased adoption of hybrid and ceramic bearings in EVs.
-
Sustainability-focused manufacturing, using recycled and bio-based materials.
-
Further integration of AI and automation in quality control and production processes.
-
Development of nano-coatings and self-healing materials to extend bearing life.
Conclusion
The automotive bearing market is evolving with advancements in material science and manufacturing technologies. With a focus on durability, efficiency, and sustainability, manufacturers are leveraging high-performance materials and precision manufacturing techniques to meet the demands of modern and future vehicles. As the industry progresses, continuous innovation will drive the development of next-generation automotive bearings, improving performance across internal combustion, hybrid, and electric vehicles.
- Art
- Causes
- Crafts
- Dance
- Drinks
- Film
- Fitness
- Food
- Juegos
- Gardening
- Health
- Home
- Literature
- Music
- Networking
- Other
- Party
- Religion
- Shopping
- Sports
- Theater
- Wellness
- IT, Cloud, Software and Technology