What are the essential components of a laser marking system and their roles?
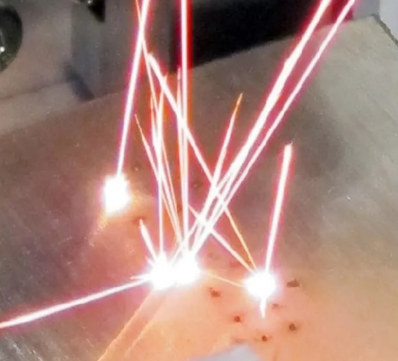
A laser marking system is an advanced technological solution that utilizes a focused laser beam to create permanent markings on various materials. This technology has found applications across multiple industries, including manufacturing, aerospace, automotive, medical devices, and consumer goods. Understanding the essential components of a laser marking system and their roles is crucial for businesses seeking to implement this technology effectively. This article delves into the key components of a laser marking system, explaining their functions and importance in the overall marking process.
1. Laser Source
The heart of any laser marking system is the laser source, which generates the laser beam used for marking. Different types of lasers can be employed, each suitable for specific applications depending on the material being marked. The primary laser types include:
-
CO2 Lasers: These lasers are commonly used for marking non-metal materials such as wood, plastics, and glass. They emit infrared light and can provide efficient marking on a variety of surfaces.
-
Fiber Lasers: Fiber lasers have gained popularity due to their efficiency and ability to mark metals with high precision. They are particularly effective for applications requiring deep engraving or high-speed marking.
-
UV Lasers: These lasers operate at shorter wavelengths and are ideal for marking sensitive materials without causing thermal damage. They are commonly used in the electronics and medical device industries.
The choice of laser source significantly influences the marking quality, speed, and capability of the system.
2. Optics System
The optics system in a laser marking system is responsible for directing and focusing the laser beam onto the material surface. This system typically includes lenses and mirrors that manipulate the beam to achieve the desired spot size and focus. Key components of the optics system include:
-
Focusing Lens: This lens focuses the laser beam to a fine point on the material surface, increasing the energy density and enabling effective marking. The focal length of the lens determines the size of the focused spot and influences marking precision.
-
Beam Splitters and Mirrors: These components direct the laser beam through the marking head. They ensure that the beam travels efficiently and reaches the intended target without significant loss of energy.
A well-designed optics system is essential for achieving high-quality markings and ensuring that the laser energy is concentrated effectively.
3. Marking Head
The marking head is a critical component of the laser marking system that houses the laser source and optics. It is responsible for moving the laser beam across the material surface to create the desired markings. The marking head can be stationary or mobile, depending on the system design. Key aspects of the marking head include:
-
Movement Mechanism: The marking head may use servo motors or stepper motors to control its movement, allowing for precise positioning of the laser beam. This movement is crucial for creating intricate designs and patterns.
-
Cooling System: High-power lasers generate heat during operation, so an effective cooling system is necessary to prevent overheating. Cooling mechanisms can include air cooling, water cooling, or even advanced liquid cooling systems.
The marking head plays a vital role in determining the speed and accuracy of the marking process, making it an essential component of the overall system.
4. Control System
The control system is the brain of the laser marking system, responsible for regulating the operation of various components and executing the marking process. This system typically consists of hardware and software elements that facilitate user interaction, design input, and machine operation. Key functions of the control system include:
-
User Interface: The control system provides a user-friendly interface that allows operators to input designs, adjust settings, and monitor the marking process. This interface can be a touchscreen display or a computer software application.
-
Motion Control: The control system coordinates the movement of the marking head and the laser beam's activation, ensuring the precise execution of the marking pattern. It translates the design input into commands that guide the marking head's movement.
-
Parameter Management: The control system allows operators to adjust parameters such as laser power, speed, and frequency, enabling customization for different materials and marking requirements.
An effective control system enhances the overall usability and efficiency of the laser marking process.
5. Workstation or Material Handling System
The workstation or material handling system supports the materials being marked and ensures proper alignment during the marking process. This component can vary widely depending on the application and material type. Key considerations include:
-
Material Support: The workstation should provide a stable surface for the material to be marked. This stability is crucial for maintaining accuracy during the marking process.
-
Alignment Mechanisms: Proper alignment of the material with the laser beam is essential for achieving precise markings. Some systems may incorporate automated alignment features to optimize the setup process.
-
Safety Features: Workstations should include safety features to protect operators from laser exposure. This may include safety interlocks, shields, or enclosures to contain the laser beam during operation.
A well-designed workstation or material handling system improves the efficiency and safety of the laser marking operation.
6. Exhaust System
During the laser marking process, materials may release fumes, smoke, or particulates that can be harmful to operators and affect marking quality. An effective exhaust system is essential for maintaining a safe working environment. Key components of the exhaust system include:
-
Fume Extraction: The exhaust system should incorporate fume extraction capabilities to remove harmful gases and particulates generated during marking. This helps to ensure a safe atmosphere for operators.
-
Filtration: High-quality filters are necessary to capture fine particles and harmful substances. The filtration system should be regularly maintained to ensure optimal performance.
Proper ventilation and exhaust systems are critical for workplace safety and ensuring that laser marking operations comply with health regulations.
7. Software Solutions
Software plays a crucial role in the operation of a laser marking system. It enables the design, management, and execution of marking tasks. Key software functions include:
-
Design Input: Software allows operators to create or import designs for marking. This can include text, logos, barcodes, and intricate patterns. CAD (Computer-Aided Design) compatibility enhances design flexibility.
-
Parameter Settings: The software interface enables users to adjust various parameters, such as laser power and speed, depending on the material and desired marking quality.
-
Job Management: Advanced software solutions allow for job scheduling, tracking, and management, improving workflow efficiency and organization.
The integration of robust software solutions enhances the overall functionality and effectiveness of the laser marking system.
8. Safety Features
Safety is a paramount concern in laser marking operations. Laser marking systems should be equipped with various safety features to protect operators and comply with regulatory standards. Key safety components include:
-
Safety Interlocks: These mechanisms prevent the laser from operating unless the protective doors are closed, minimizing the risk of accidental exposure.
-
Emergency Stop Buttons: Easily accessible emergency stop buttons allow operators to halt the marking process immediately in case of an emergency.
-
Protective Enclosures: Enclosures or shields can help contain the laser beam, reducing the risk of exposure to personnel in the vicinity.
Implementing comprehensive safety features ensures a secure working environment for operators and compliance with safety regulations.
Conclusion
A laser marking system consists of several essential components, each playing a critical role in the marking process. Understanding these components—laser source, optics system, marking head, control system, workstation, exhaust system, software solutions, and safety features—is vital for businesses seeking to implement laser marking technology effectively.
As industries continue to evolve and demand for precise and permanent marking solutions grows, the importance of each component within the laser marking system becomes increasingly evident. By investing in high-quality laser marking systems and ensuring that all components are well-integrated and maintained, businesses can enhance their operational efficiency, improve product traceability, and achieve high-quality markings tailored to their specific needs.
Overall, the integration of advanced laser marking technology into various sectors represents a significant step forward in product identification and manufacturing processes, paving the way for innovation and efficiency in an increasingly competitive landscape.
- Art
- Causes
- Crafts
- Dance
- Drinks
- Film
- Fitness
- Food
- Games
- Gardening
- Health
- Home
- Literature
- Music
- Networking
- Other
- Party
- Religion
- Shopping
- Sports
- Theater
- Wellness
- IT, Cloud, Software and Technology