Solar Panel Manufacturing Plant Project Report 2025: Key Steps, Challenges and Solutions
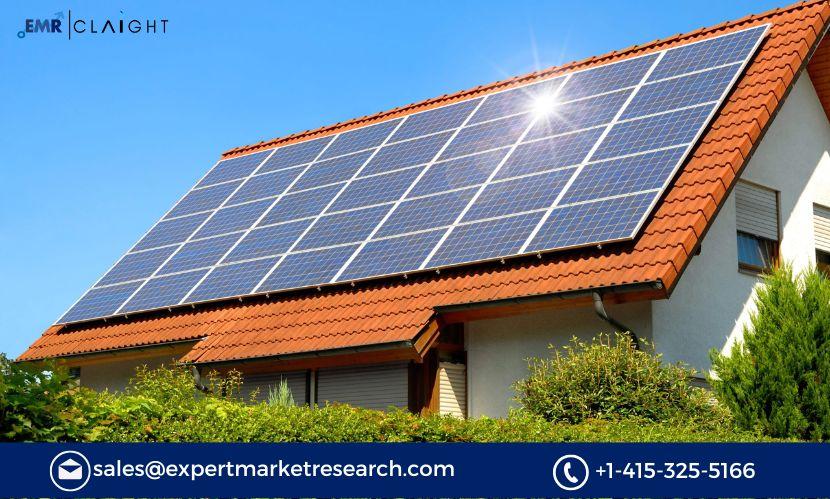
Introduction
The solar energy industry has seen significant growth as the world transitions toward renewable energy sources. Solar panels are at the heart of this transformation, converting sunlight into electricity to power homes, businesses, and entire cities. The demand for solar panels continues to rise due to factors such as government incentives, increasing environmental awareness, and technological advancements in solar power systems. Setting up a solar panel manufacturing plant is a promising venture that aligns with global sustainability goals and offers lucrative business opportunities. This Solar Panel Manufacturing Plant Project Report provides an in-depth look at the critical components of setting up a successful solar panel production facility. From market analysis and raw material sourcing to production processes, equipment requirements, and regulatory compliance, this report serves as a comprehensive guide for businesses looking to enter or expand in the solar manufacturing industry.
Market Overview and Demand Analysis
The solar panel industry has experienced rapid expansion, driven by a combination of declining manufacturing costs, government support for renewable energy adoption, and growing environmental concerns. Solar energy is being embraced worldwide, with solar panels used in residential, commercial, and industrial applications.
Key factors driving the demand for solar panels include:
-
Government Incentives and Subsidies: Many governments provide subsidies, tax credits, and incentives to promote renewable energy adoption. These policies encourage both businesses and consumers to invest in solar energy solutions.
-
Decreasing Cost of Solar Panels: Over the years, the cost of solar panel manufacturing has decreased due to advancements in production technologies and economies of scale. This reduction in cost has made solar energy more accessible to a broader market, further boosting demand.
-
Environmental Awareness: As the world becomes more focused on sustainability and combating climate change, solar energy is increasingly viewed as a clean and renewable source of power. Public and corporate interest in reducing carbon footprints further drives the demand for solar panels.
-
Energy Independence and Security: Solar power allows consumers and businesses to reduce their reliance on traditional power grids and non-renewable energy sources. As electricity prices rise, solar panels offer an attractive long-term solution for energy independence.
-
Technological Advancements: Solar panel efficiency has improved significantly over the years, making them more effective at converting sunlight into electricity. Research and development in solar technology continue to drive innovation, making solar energy even more efficient and cost-effective.
The solar panel market is poised for growth, and establishing a manufacturing plant to meet the increasing demand presents a lucrative business opportunity. However, careful analysis of regional market conditions, competition, and customer preferences is crucial for creating a successful strategy.
Get a Free Sample Report with Table of Contents@
Regulatory Considerations
Setting up a solar panel manufacturing plant requires compliance with various regulations that ensure product safety, quality, and environmental sustainability. Understanding these regulatory requirements is essential for the successful operation of the plant.
Key regulatory considerations include:
-
International Standards and Certifications: Solar panels must meet international standards for performance, safety, and durability. Standards such as IEC 61215 (for crystalline silicon modules) and IEC 61730 (for module safety) are commonly recognized. Obtaining these certifications ensures the panels meet global quality standards.
-
Environmental Regulations: Solar panel manufacturing involves the use of chemicals and materials that can have an environmental impact. Manufacturers must comply with local and international environmental regulations regarding waste disposal, emissions, and resource usage.
-
Labor Safety Standards: The plant must comply with local labor laws and occupational health and safety regulations to ensure the well-being of workers. Proper training, protective equipment, and workplace safety measures must be in place to minimize risks.
-
Product Labeling and Warranty: Solar panel manufacturers are required to provide clear labeling that includes product specifications, warranty information, and safety instructions. This ensures transparency for consumers and builds trust in the product.
-
Energy Efficiency and Carbon Footprint: In some regions, solar panel manufacturing facilities may be required to demonstrate energy efficiency or implement measures to reduce their carbon footprint, given the eco-friendly nature of the final product.
Raw Materials for Solar Panel Production
The production of solar panels involves a variety of raw materials, each contributing to the overall performance, durability, and cost-effectiveness of the final product. The primary raw materials used in solar panel manufacturing include:
-
Silicon: Silicon is the core material used in most solar panels, especially in crystalline silicon-based photovoltaic (PV) modules. Silicon wafers are sliced from silicon ingots and are responsible for converting sunlight into electricity.
-
Glass: Transparent tempered glass is used as the outer protective layer of solar panels. It protects the sensitive silicon cells from environmental factors such as rain, wind, and UV exposure while allowing sunlight to pass through.
-
Frame: Solar panels are typically framed using aluminum, which provides structural integrity and facilitates easy mounting of the panels on rooftops or ground-mounted systems.
-
Backsheet: The backsheet is a crucial component of the solar panel that provides insulation and protection to the electrical components of the panel. It is typically made of durable plastic materials that can withstand environmental stressors.
-
Encapsulant: Encapsulant materials such as Ethylene-Vinyl Acetate (EVA) are used to encapsulate the solar cells, protecting them from moisture and mechanical damage while enhancing the electrical output.
-
Electrical Components: These include diodes, junction boxes, connectors, and cables, which are used for the electrical connections between solar cells and the inverter.
-
Silver and Copper: Silver is used in the conductive contacts on solar cells, while copper is used for wiring the electrical connections within the panel.
Sourcing high-quality raw materials from reliable suppliers is crucial to ensure the production of efficient and durable solar panels. Establishing strong relationships with suppliers can help ensure the availability of raw materials at competitive prices.
Manufacturing Process
The process of manufacturing solar panels involves several critical stages, including the production of silicon wafers, assembly of solar cells, and final integration into functional solar modules. Here is a step-by-step overview of the typical manufacturing process:
-
Silicon Wafer Production: Silicon is extracted from sand and refined into high-purity silicon. The silicon is then melted and formed into large blocks (ingots), which are sliced into thin wafers. These wafers are the foundation of solar cells.
-
Solar Cell Production: The silicon wafers are treated and coated to form solar cells. This step involves doping the wafers with materials such as phosphorus or boron to create positive and negative charges. The cells are then treated with anti-reflective coatings to improve their efficiency.
-
Cell Testing and Sorting: Each solar cell is tested for its electrical efficiency. The cells are then sorted based on their performance to ensure that only the most efficient cells are used in the final panels.
-
Cell Interconnection: The individual solar cells are connected in series or parallel using conductive metal ribbons. This process allows the cells to generate enough power when exposed to sunlight.
-
Lamination: The interconnected cells are sandwiched between layers of encapsulant material and sealed within a protective layer of glass and backsheet. The lamination process is carried out in a vacuum chamber to ensure that the cells are properly encapsulated and sealed.
-
Framing and Mounting: The laminated solar panel is then fitted into an aluminum frame, which provides structural integrity and facilitates easy installation. The frame also protects the edges of the panel from damage.
-
Junction Box and Electrical Connections: A junction box is attached to the back of the panel, and electrical connections are made for the output cables. This allows the panel to be connected to the rest of the solar power system.
-
Testing and Quality Control: Each finished solar panel is subjected to various tests, including performance testing, visual inspection, and durability tests to ensure it meets safety and quality standards.
-
Packaging: After passing quality control, the solar panels are carefully packaged to prevent damage during shipping and handling.
Plant Layout and Design
The layout and design of a solar panel manufacturing plant should focus on optimizing efficiency, ensuring worker safety, and minimizing waste. The key areas of the plant include:
-
Raw Material Storage: A dedicated area for storing raw materials such as silicon, glass, and aluminum. This area should be organized and secure to prevent contamination.
-
Production Line: The heart of the manufacturing facility, where the individual production stages, such as silicon wafer slicing, cell production, lamination, and assembly, are carried out. The production line should be designed for smooth workflow and minimal downtime.
-
Testing and Quality Control Area: A dedicated space for testing and inspecting solar cells and panels to ensure they meet performance, safety, and durability standards.
-
Packaging Area: A clean and organized area for packaging the finished panels before shipping. This area should ensure the panels are carefully handled to avoid damage.
-
Waste Management Area: A designated area for the proper disposal of waste materials, including packaging materials, defective panels, and chemical by-products.
-
Administrative and Support Areas: Offices, meeting rooms, and employee amenities for the plant's management, research, and support staff.
Machinery and Equipment
The production of solar panels requires specialized machinery and equipment at each stage of the manufacturing process. Some of the key equipment needed includes:
-
Silicon Wafer Slicing Machines: These machines cut silicon ingots into thin wafers, which serve as the base for solar cells.
-
Solar Cell Doping Equipment: Used for doping the silicon wafers with phosphorus or boron to create the necessary charge for generating electricity.
-
Anti-Reflective Coating Machines: These machines apply a layer of anti-reflective coating to the solar cells, enhancing their efficiency by reducing light reflection.
-
Cell Interconnection Machines: Used to connect individual solar cells in series or parallel to form a complete solar panel.
-
Lamination Machines: Used to encapsulate the solar cells between layers of protective glass and backsheet, ensuring durability and weather resistance.
-
Testing and Inspection Equipment: Instruments to measure the performance and durability of solar cells and panels, ensuring they meet the required standards.
-
Framing and Packaging Machines: Automated systems for framing the solar panels and packaging them for shipping.
Financial Projections and Investment Requirements
Establishing a solar panel manufacturing plant requires significant investment. The financial projections should include:
-
Capital Investment: The cost of land, building, machinery, and initial raw materials.
-
Operating Costs: Ongoing expenses such as labor, utilities, raw materials, and maintenance.
-
Revenue Projections: Expected revenue based on production capacity, pricing, and market demand.
-
Profitability Analysis: Break-even analysis and financial forecasting to assess the long-term profitability of the plant.
-
Funding Requirements: Potential sources of funding, including loans, equity investments, or venture capital.
Related Reports
https://www.expertmarketresearch.com/blogs/top-india-diapers-companies
https://www.expertmarketresearch.com/blogs/top-spices-companies
https://www.expertmarketresearch.com/blogs/top-carbon-black-companies
Media Contact
Company Name: Claight Corporation
Contact Person: Peter Fernandas, Corporate Sales Specialist
Email: sales@expertmarketresearch.com
Toll Free Number: +1–415–325–5166 | +44–702–402–5790
Address: 30 North Gould Street, Sheridan, WY 82801, USA
Website: www.expertmarketresearch.com
- Art
- Causes
- Crafts
- Dance
- Drinks
- Film
- Fitness
- Food
- Jogos
- Gardening
- Health
- Início
- Literature
- Music
- Networking
- Outro
- Party
- Religion
- Shopping
- Sports
- Theater
- Wellness
- IT, Cloud, Software and Technology