Spindle Shaft Positioning Method
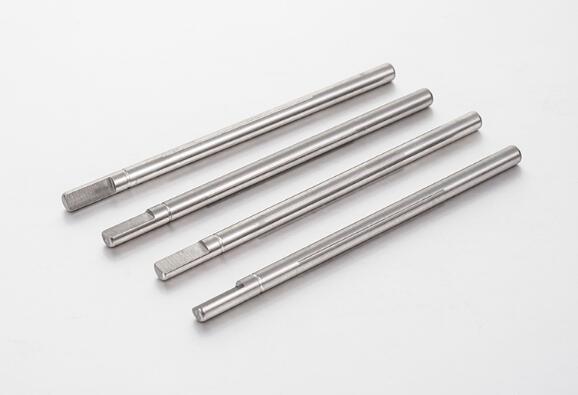
Usually, the spindle shaft is only for speed control, but in some special cases, it is also necessary to control the position of the spindle. For example, when an automatic tool change is performed on a machining center when a tool needs to be changed due to technological requirements in boring processing, and when a workpiece is loaded on a lathe, the spindle needs to be accurately stopped at a specific position. This is what we usually call the spindle shaft directional function.
Spindle shaft orientation function is that NC sends a directional command to stop the spindle shaft at a certain position through a rotation signal on the position sensor on the spindle shaft, and provides a certain holding torque to the servo motor position loop. Spindle shaft machining looks for Tihao. Professional quality assurance. Spindle shaft orientation refers to the function of realizing the accurate positioning of the spindle shaft at a specific position in the circumferential direction. In the process of NC machine tool, in order to realize automatic tool change, the manipulator can accurately load the tool into the spindle hole. The keyway of the tool must be aligned with the key position of the spindle in the circumferential direction; in the boring process, when the tool is retracted, the tool is required to move a distance in the opposite direction of the tooltip before it can exit, so as not to scratch the workpiece. The spindle shaft has the function of accurate positioning in the circumferential direction.
Spindle shaft positioning is to determine the position and direction of the tool, including:
- The coordinates of the tool center point in the X, Y, and Z directions;
2, the angle between the center of the spindle shaft and the three coordinate axes X, Y, and Z, or the angle between the surface where the cutting edge of the tool is located and the above three coordinate axes. According to these, it is the initial positioning and repositioning of these position parameters that you can machine the required part position parameters, and you have completed the determination of the initial position of the tool, which is positioning in the general sense.
If it is extended, the above-mentioned position parameters are changed during the processing, and this change can also be understood as constant repositioning.
There are many ways to realize the positioning of the spindle shaft. According to the different control methods, there are the following:
(1) Mechanical deceleration positioning: Spindle shaft uses machinery to achieve deceleration and positioning, which is called mechanical deceleration positioning.
(2) Deceleration and positioning of electrical appliances: The spindle shaft uses electrical appliances to achieve deceleration and positioning.
(3) Electric deceleration magnetic induction positioning: The spindle shaft is decelerated by the electric appliance, and the positioning is completed by the magnetic induction.
(4) Electrical deceleration and mechanical positioning: The spindle shaft uses electrical to achieve deceleration and mechanical positioning.
(5) Hydraulic (or pneumatic) positioning.
Ningbo Shitai Precision Machinery Co., Ltd. not only has spindle shaft but is also a China transmission shaft company. Welcome to visit our official website.
- Art
- Causes
- Crafts
- Dance
- Drinks
- Film
- Fitness
- Food
- Oyunlar
- Gardening
- Health
- Home
- Literature
- Music
- Networking
- Other
- Party
- Religion
- Shopping
- Sports
- Theater
- Wellness
- IT, Cloud, Software and Technology