CNC Machine Market Analysis: Projected Growth from USD 67.5 Billion in 2023 to USD 80.4 Billion in 2028
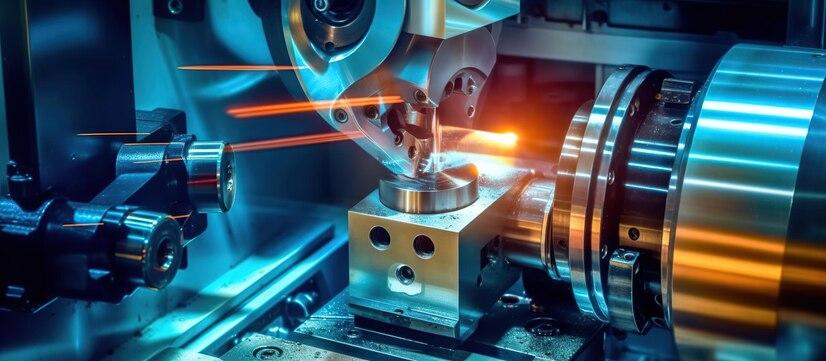
Computer Numerical Control (CNC) refers to the automated control of machining tools and 3D printers using a computer. CNC machines convert a design produced by Computer-Aided Design (CAD) software into a set of instructions that guide the movements of the machine’s tools to produce precise parts and products. This technology has revolutionized manufacturing by increasing efficiency, accuracy, and the ability to produce complex shapes.
Key Components of CNC Systems
1. CNC Controller: The brain of the CNC machine, interprets the CAD design and converts it into a series of instructions, known as G-code, which control the movement and operation of the machine’s tools.
2. Machine Tools: These include lathes, mills, routers, grinders, and laser cutters, among others. The specific tool used depends on the manufacturing process and the type of material being worked on.
3. Drive/Actuation System: This consists of motors and actuators that move the machine components according to the controller’s instructions. It ensures precise movement along the X, Y, and Z axes.
4. Feedback System: Also known as the closed-loop system, it continuously monitors the position and speed of the machine components, ensuring that they follow the intended path accurately.
Benefits of CNC Machining
Precision and Accuracy: CNC machines can produce parts with very tight tolerances, often within thousandths of an inch, which is essential for industries requiring high precision, such as aerospace and medical device manufacturing.
Consistency and Repeatability: Once a CNC program is verified, it can be run repeatedly to produce identical parts with minimal variation, ensuring consistent quality across large production runs.
Increased Productivity: CNC machines can operate continuously and can be programmed to perform multiple operations in a single setup, reducing the need for manual intervention and increasing overall productivity.
Complex Geometry: CNC machining allows for the production of complex shapes and features that would be difficult or impossible to achieve with manual machining processes.
Reduced Waste: The precision of CNC machining minimizes material waste, leading to cost savings and more efficient use of raw materials.
Applications of CNC Machining
Aerospace: CNC machining is used to manufacture complex components for aircraft, including engine parts, airframe components, and intricate geometries required for aerodynamic efficiency.
Automotive: The automotive industry relies on CNC machining for the production of engine components, transmission parts, and custom parts for prototype vehicles.
Medical Devices: Precision and reliability are critical in the medical field. CNC machining is used to produce surgical instruments, implants, and other medical devices with high accuracy.
Electronics: CNC machining is employed in the manufacture of electronic components, such as housings, connectors, and circuit boards.
Prototyping and Product Development: CNC machines are widely used in prototyping to create functional models and prototypes for testing and validation before mass production.
Future Trends
Integration with Additive Manufacturing: Combining CNC machining with 3D printing technologies allows for hybrid manufacturing processes that leverage the strengths of both subtractive and additive methods.
Smart Manufacturing and Industry 4.0: The integration of IoT (Internet of Things) and AI (Artificial Intelligence) with CNC machines is enabling smarter, more autonomous manufacturing systems that can optimize production in real time.
Advancements in Materials: Continued developments in materials science are expanding the range of materials that can be effectively machined using CNC technology, including composites and advanced alloys.
In summary, CNC technology has transformed the manufacturing landscape by enabling high precision, efficiency, and the ability to produce complex geometries. As technology continues to advance, CNC machining is poised to become even more integral to modern manufacturing processes.
- Art
- Causes
- Crafts
- Dance
- Drinks
- Film
- Fitness
- Food
- Jocuri
- Gardening
- Health
- Home
- Literature
- Music
- Networking
- Alte
- Party
- Religion
- Shopping
- Sports
- Theater
- Wellness
- IT, Cloud, Software and Technology