Aerospace Parts Manufacturing: Ensuring Safety, Reliability and Performance
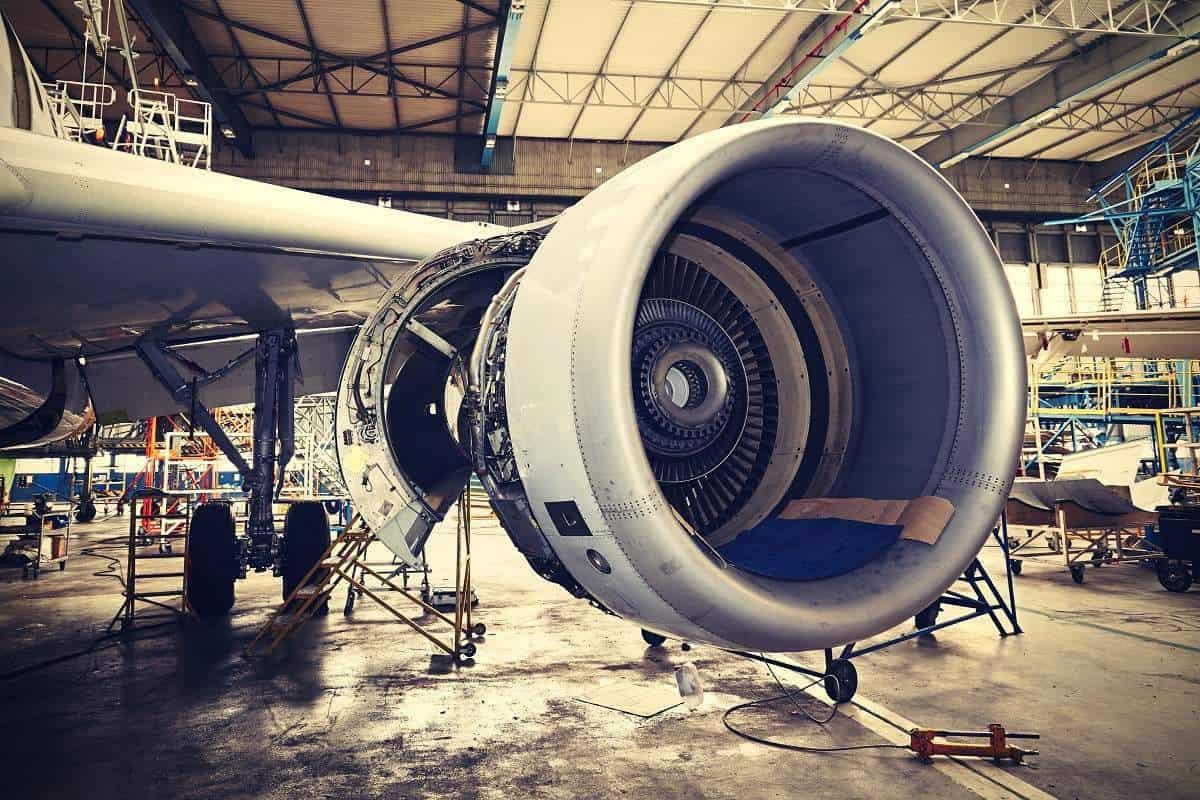
Stringent Quality Standards
The aerospace industry has some of the strictest quality standards of any manufacturing sector. Aerospace parts must consistently perform under extreme conditions of temperature, pressure, vibration and force. They are critical components that ensure the safety and reliability of aircraft and spacecraft. Manufacturers of aerospace parts must have rigorous quality control systems in place and comply with regulations from organizations like the FAA, EASA and ISO. Every part that rolls off the production line undergoes a battery of inspections and tests to verify it meets design specifications and will not fail in service. Non-conforming parts are rejected to maintain the high reliability required in aerospace applications.
Advanced Manufacturing Technologies
Leading Aerospace Parts manufacturers leverage cutting-edge technologies to achieve the tight tolerances demanded. Computer numerical control (CNC) machining centers allow complex geometries to be machined with precision. Non-destructive testing using techniques such as x-ray, ultrasound and eddy current inspection check for defects invisible to the naked eye. Three-dimensional (3D) printing is gaining popularity for low-volume specialty parts due to the design freedom it provides. Parts can be architected with internal lattice structures to maximize strength while minimizing weight. Advanced finishing methods like selective laser melting produce smoother surfaces with greater density for enhanced fatigue life. Traceability systems associate digital records with each part so its complete manufacturing history can be retrieved.
Superalloy Material Selection
The choice of material is crucial since aerospace parts must withstand extreme stresses and operating temperatures for decades. Superalloys based on nickel, cobalt and iron alloyed with chromium and other elements can retain their strength at over 1000°F. Titanium and aluminum alloys are also widely used for their high strength-to-weight ratios. Composites combining carbon or glass fibers with aluminum or epoxy matrices offer design flexibility while saving weight. Coatings such as thermal barrier improve corrosion and erosion resistance. Materials are rigorously tested to develop safe operating regimes and detect damage mechanisms like creep, fatigue and corrosion. Their performance drives continuous alloy innovations to push design envelopes.
Component Design Considerations
Aerospace parts are engineered with multiple factors in mind. Dimensional accuracy and precision interfaces are mandatory for assembly and interchangeability. Weight is significant as even small savings translate to major operational cost benefits over a component’s lifespan. Damage tolerance and fail-safe operations mitigate risks from potential defects or stresses. Modular designs allow replacement of sections instead of the entire part. Ease of inspection and maintenance facilitates repair or overhaul. The components must integrate reliably in varied operating conditions like extreme pressures, cryogenic temperatures, and exposure to liquids, gasses and plasma. Computational tools simulate real-world loading and predict part life under critical failure modes. Value analysis evaluates total life-cycle costs against design parameters.
Global Supply Chain Management
Since raw material sourcing to final assembly and delivery spans the globe, managing complex supply chains is critical. Establishing multiple approved vendor sources for raw material and bought-out parts mitigates supply risks. Vendors are qualified using stringent criteria related to quality systems, process controls, traceability standards, financial stability and more. Many Tier 1 suppliers specialize in complex sub-assemblies that integrate functions from engineering to manufacturing. Just-in-time production and lean manufacturing principles reduce working capital needs and inventory carrying costs. Integrated IT systems link customer specifications and forecasts with work orders and delivery schedules all through the production flow. Monitoring key performance metrics and conducting regular audits ensures procurement quality objectives are met.
Regulatory Compliance
Aerospace parts manufacturers operate under rigorous regulatory oversight to guarantee airworthiness across diverse markets. They must obtain certifications from authorities like the FAA, EASA, CAAC and CAAI that cover design, production and quality management system approvals. Standards such as AS/EN/JISQ 9100 establish requirements for a robust quality assurance system covering areas like document and data control, inspection and testing, corrective and preventive actions, audits, training and more. Strict configuration management procedures adhere to engineering specifications and approved design data. Any changes are implemented only after thorough impact analysis, re-qualification and regulatory approvals. Traceability is maintained for specialty materials, heat treatments, coatings and critical processes to facilitate recalls in case of non-conformances. Periodic surveillance audits ensure sustained compliance.
Future Outlook
Advances in digital technologies are poised to transform manufacturing. The Industrial Internet of Things (IIoT) enables real-time machine monitoring and predictive maintenance to optimize uptimes. Additive manufacturing promises on-demand production with less waste. Augmented reality aids assembly and inspection. Blockchain based distributed ledgers facilitate traceability and authentication across multi-tier supply chains. Future aircraft like hybrid electrics will drive new material innovations. Low-cost nanosatellites and reusable rockets will expand access to space. 3D printing of functional systems directly in zero gravity conditions is under study. With innovation outpacing regulations, international standardization will be critical. As flying, space access and orbital assets multiply globally, optimizing safety, sustainability and performance of aerospace parts.
- Art
- Causes
- Crafts
- Dance
- Drinks
- Film
- Fitness
- Food
- Jocuri
- Gardening
- Health
- Home
- Literature
- Music
- Networking
- Alte
- Party
- Religion
- Shopping
- Sports
- Theater
- Wellness
- IT, Cloud, Software and Technology