Proper Storage and Handling of Chemical Drums is Crucial for Worker Safety
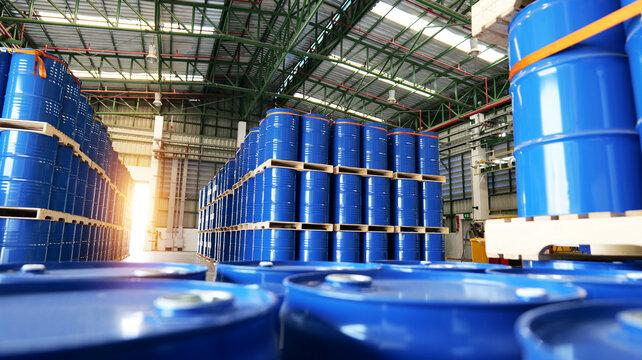
DOT regulations specify standards for various types of packaging used to transport chemicals by road, air, rail and sea. Chemical drums are classified based on the hazard class of contents - flammable liquids, corrosives, poisonous materials and more. Tests are conducted to check if drums can withstand impacts, punctures and other stresses of transport without leaks. UN-approved drums meeting performance tests are assigned special markings.
OSHA standards provide guidelines on safe storage of chemicals at industrial facilities. Drums must be kept in designated areas away from heat sources or open flames. Segregation is important to avoid dangerous interactions between incompatible chemicals stored together. Secondary containment pallets or troughs can collect spills and leaks from multiple drums. Spill kits with absorbents must be easily accessible.
Proper Drum Handling Techniques
Many injuries occur due to improper Chemical Drums handling practices. Empty drums should be treated with the same level of care as full ones, as residue can cause risks. Drums must always be securely closed to prevent risks from vapor inhalation or skin exposure.
Using drum dollies or carriers is safer than rolling or tilting heavy drums manually. Drums should never be thrown, dropped or slid across surfaces. The bungs and openings should not be tampered with once drums are received. Any leaks, rust or defects must be reported immediately.
When moving drums, tilt them slightly to allow the contents to shift to one end to maintain balance. Never place hands inside drums during handling - use tools like hooks, slings or drum worms instead. Special care is required for heavier drums above 50 lbs or those containing hazardous chemicals. Powered industrial trucks with lifts and sideshifters are recommended for such drums.
Proper Inspection and Maintenance
Regular inspection and maintenance is important for chemical drums to ensure continued compliance with safety and transport regulations over multiple use cycles. Periodic external inspection checks for rust, dents, leak paths or bulges in drum bodies.
Bungs, closures, gaskets and sealing surfaces also require evaluation. Any defective drums should be taken out of service and recycled or disposed as per applicable regulations. Proper date-coding helps track inspection and requalification cycles for drums. Leak-proof integrity tests using air pressure or water are conducted as needed.
Cleanliness is as important as structural integrity for chemical drums. Remnants left behind after cleaning can react with subsequent cargo. Steam cleaning or other approved decontamination procedures completely remove residues before reuse. Proper paperwork must accompany drums through the supply chain with details of previous contents and cleaning.
Get more insights on Chemical Drums
- Art
- Causes
- Crafts
- Dance
- Drinks
- Film
- Fitness
- Food
- الألعاب
- Gardening
- Health
- الرئيسية
- Literature
- Music
- Networking
- أخرى
- Party
- Religion
- Shopping
- Sports
- Theater
- Wellness
- IT, Cloud, Software and Technology