What Is The Casting Process of Bearing Blocks?
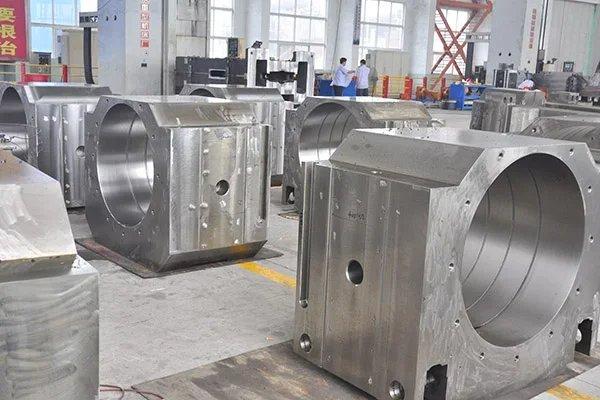
https://www.special-metal.com/Bearing-blocks.html play a crucial role in various industries, providing support and stability for rotating shafts. One of the common manufacturing methods for bearing blocks is casting. In this article, we will delve into the casting process of bearing blocks, exploring the steps involved, the materials used, and the advantages of this manufacturing technique.
I. Understanding the Casting Process
Casting is a manufacturing process that involves pouring molten metal into a mold to create a desired shape. It is widely used in the production of bearing blocks due to its cost-effectiveness, versatility, and ability to produce complex geometries. Let's take a closer look at the steps involved in the casting process of bearing blocks.
II. Preparing for Casting
Before the casting process begins, several preparations need to be made.
A. Designing the Bearing Block Pattern:
The first step is to create a pattern that represents the final shape of the bearing block. This pattern is typically made from wood, plastic, or metal and serves as a template for the mold.
B. Selecting the Suitable Casting Material:
The choice of casting material depends on factors such as load-bearing capacity, corrosion resistance, and temperature resistance. Common materials used for bearing blocks include cast iron, bronze, and steel alloys.
C. Preparing the Mold for Casting:
The mold is created by packing a mixture of sand and binders around the pattern. This mold cavity will determine the final shape of the casting. It is essential to ensure that the mold is properly prepared and vented to allow for the escape of gases during the casting process.
III. The Casting Process
Once the preparations are complete, the casting process can begin.
A. Melting and Preparing the Metal Alloy:
The selected metal alloy is melted in a furnace at high temperatures. The molten metal is carefully monitored to ensure it reaches the desired temperature and composition.
B. Pouring the Molten Metal into the Mold:
The molten metal is poured into the mold cavity through a gating system. The gating system consists of channels and runners that allow the molten metal to flow smoothly into the mold.
C. Solidification and Cooling of the Casting:
As the molten metal fills the mold, it begins to solidify and take the shape of the pattern. The cooling process is crucial as it determines the final properties of the casting. Proper cooling rates and controlled solidification help prevent defects such as shrinkage and porosity.
D. Removing the Casting from the Mold:
Once the casting has solidified and cooled, it is removed from the mold. This process may involve breaking the mold or using specialized techniques to extract the casting without causing damage.
IV. Post-Casting Operations
After the casting is removed from the mold, several post-casting operations are performed to refine the final product.
A. Removing Excess Material and Finishing the Casting:
The casting may have excess material, known as the gating system, attached to it. This excess material is removed through processes such as sawing, grinding, or machining. The casting is then finished to achieve the desired surface texture and dimensional accuracy.
B. Heat Treatment for Enhancing Mechanical Properties:
Heat treatment processes like annealing, quenching, and tempering may be applied to improve the mechanical properties of the casting. These processes help enhance the strength, hardness, and toughness of the bearing block.
C. Machining and Precision Grinding of Bearing Blocks:
To achieve precise dimensions and tolerances, machining and precision grinding operations are performed on the casting. This ensures that the bearing block fits perfectly with other components in the assembly.
V. Quality Control in Casting
To ensure the quality and integrity of the casting, various quality control measures are implemented.
A. Non-Destructive Testing Methods for Ensuring Casting Integrity:
Techniques such as X-ray inspection, ultrasonic testing, and magnetic particle inspection are used to detect any internal defects or irregularities in the casting.
B. Dimensional Inspection and Tolerance Checks:
The dimensions of the casting are measured using precision instruments to ensure they meet the specified tolerances. Any deviations are identified and corrected.
C. Surface Finish Evaluation and Defect Detection:
The surface finish of the casting is inspected for any defects such as cracks, pits, or surface irregularities. This helps ensure that the bearing block has a smooth and defect-free surface.
VI. Advantages of Casting Bearing Blocks
The casting process offers several advantages for manufacturing bearing blocks.
A. Cost-Effectiveness and Mass Production Capability:
Casting allows for the production of large quantities of bearing blocks at a relatively low cost. The ability to create complex shapes in a single casting reduces the need for additional machining operations.
B. Versatility in Design and Complex Geometry:
Casting enables the production of bearing blocks with intricate designs and complex geometries that would be difficult or costly to achieve using other manufacturing methods.
C. Superior Material Properties and Strength:
Casting allows for the use of a wide range of materials, including alloys with superior mechanical properties. This ensures that the bearing blocks have the necessary strength, wear resistance, and durability for their intended applications.
VII. Case Studies: Casting Process in Bearing Block Manufacturing
The casting process is widely used in various industries for manufacturing bearing blocks.
A. Automotive Industry:
Bearing blocks are crucial components in automotive engines, transmissions, and suspension systems. Casting allows for the production of bearing blocks that meet the stringent requirements of the automotive industry.
B. Heavy Machinery and Equipment:
In heavy machinery and equipment, bearing blocks are used to support rotating shafts in applications such as construction equipment, mining machinery, and power generation systems. Casting provides the necessary strength and durability for these demanding applications.
C. Aerospace and Defense Applications:
Bearing blocks are vital in aerospace and defense applications, where reliability and performance are critical. Casting allows for the production of bearing blocks that can withstand extreme conditions and meet the stringent requirements of the aerospace and defense industries.
Conclusion
The casting process is a vital method for manufacturing bearing blocks, providing numerous advantages in terms of cost, design flexibility, and material properties. By understanding the steps involved in casting, the materials used, and the quality control measures, manufacturers can produce high-quality bearing blocks that meet the demands of various industries. As technology continues to advance, we can expect further innovations in casting techniques, leading to even more efficient and reliable bearing block production.
Precision and Performance: Unveiling the Role of Bearing Blocks in Industrial Machinery
- Art
- Causes
- Crafts
- Dance
- Drinks
- Film
- Fitness
- Food
- Spiele
- Gardening
- Health
- Startseite
- Literature
- Music
- Networking
- Andere
- Party
- Religion
- Shopping
- Sports
- Theater
- Wellness
- IT, Cloud, Software and Technology