Specialty Polymers in Coatings and Adhesives: Market Trends
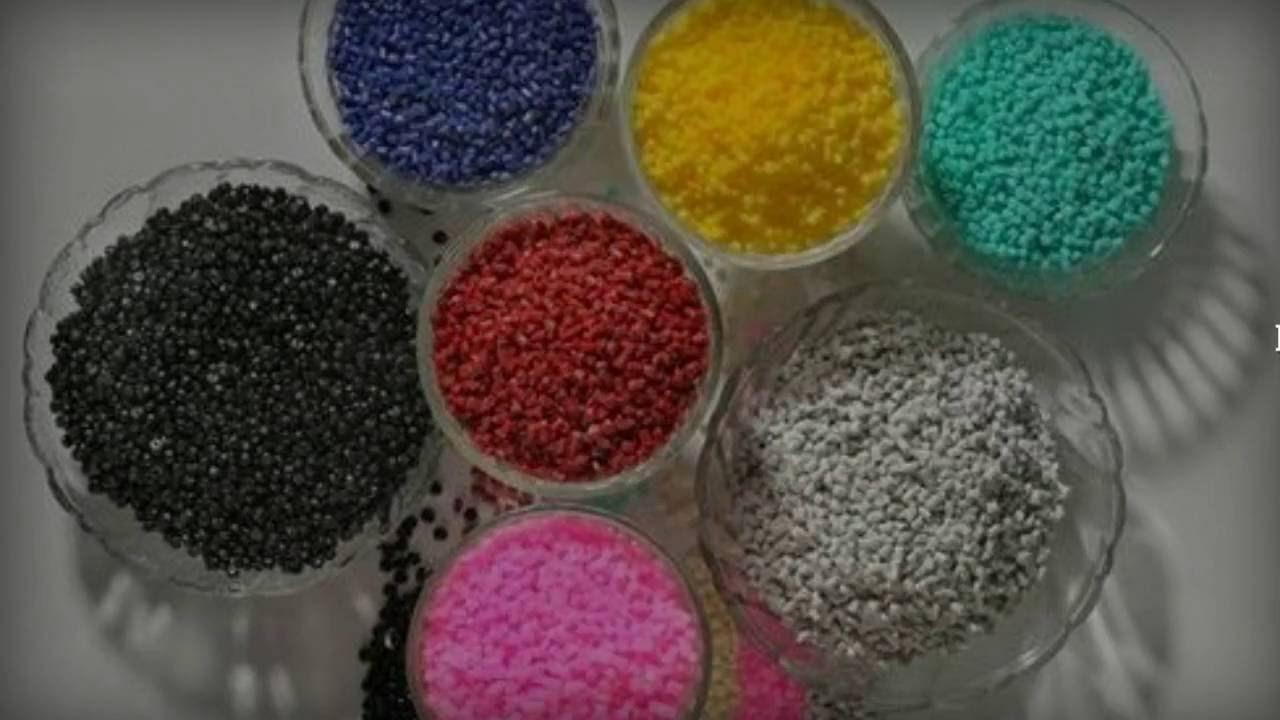
Introduction
Specialty polymers are synthetic or semi-synthetic polymers that have enhanced or tailored properties to meet the demands of specific applications in various industries like automotive, biomedical, electronics and more. These polymers differ from commodity polymers in terms of their design, processing requirements and end-use performance characteristics. Some key properties that make specialty polymers unique include heat resistance, chemical resistance, durability and biocompatibility. Their customized properties allow them to replace traditional materials in applications requiring high-end performance.
Key Types of Specialty Polymers
There are various types of specialty polymers used across different industries depending on the specific property requirements. Some of the major types include:
Thermoplastic Elastomers: As the name suggests, these polymers exhibit both thermoplastic and elastomeric properties. They have mechanical properties similar to vulcanized rubbers but can be recycled like thermoplastics. Thermoplastic elastomers find usage in automotive, industrial and consumer goods due to their flexibility and durability.
Liquid Crystal Polymers: Liquid crystal polymers possess rigid rod-like molecular structures that allow them to withstand high operating temperatures up to 250°C without losing mechanical strength. They are used for applications requiring high heat resistance like electronics, aerospace and automotive engine components.
Polyamide resins: Also known as nylon resins, polyamide resins have good mechanical, chemical and heat resistance properties. Engineering polyamides like nylon 6 and nylon 6,6 are used in automobile interiors, electrical components and industrial parts because of their strength and toughness. Specialty polyamides also find application in food packaging.
Bio-based polymers: These are polymers that are fully or partially derived from renewable plant-based resources instead of petroleum feedstocks. They include poly(lactic acid) or polylactic acid used in 3D printing filaments, compost bags and packaging due to its biodegradability. Other examples include bio-polyesters, bio-polyamides and cellulose derivatives.
Applications of Specialty Polymers
Given below are some key application areas of special polymers:
Automotive: Special polymers replace traditional materials in automotive applications to make vehicles lighter, more durable and fuel efficient. They are used in engine components, tires, hoses, seals and gaskets requiring heat resistance. Polyamides and thermoplastic polyolefins feature prominently in automotive interiors and exteriors.
Aerospace: Polymers like polyetheretherketone, polyetherimide resins and liquid crystal polymers are ideal for aerospace applications owing to properties like high strength-to-weight ratio, fatigue resistance and heat resistance up to 250°C. They are used in aircraft components such as ducting, fasteners and glues.
Biomedical: Biocompatible polymers like nylon, polyurethane, polysulfone and poly(lactic acid) find application as surgical meshes, surgical implants, scaffolds for tissue regeneration and controlled drug delivery systems. Their non-toxicity and mechanical properties make them suitable for medical devices and implants.
Electronics: Polymers play a key role in printed circuit boards, connectors, wires and cables used in consumer electronics like smartphones, laptops, TVs. Materials like liquid crystal polymers, polyetherimide, polyamide-imide provide properties like dimensional stability, solvent resistance and ability to withstand high temperatures needed for electronic packaging.
Bioenergy: Specialty bio-based polymers like polylactic acid and polyhydroxyalkanoates are used as alternatives to conventional plastics in applications having low energy requirements and short life-times like compost bags and 3D printing filaments. This promotes using renewable resources and sustainability.
Manufacturing and Processing Methods
There are various manufacturing and processing methods used to develop special polymer products based on the required performance characteristics and end-use application. Some common techniques include:
- Extrusion: Used for production of plastic pipes, tubing, window profiles from thermoplastic polymers. Melts and firms the polymer into the desired cross-section.
- Injection molding: Pre-heated polymer is injected under high pressure into a metal mold, forming complex parts which solidify. Used for automotive, electrical, consumer good components.
- Blow molding: Amorphous polymers are blown to form using air pressure into hollow shapes like bottles, drums, automotive fuel tanks.
- Film blowing: Production of plastic films, sheets through tubular film extrusion and inflation using air pressure. Application in food packaging.
- Reaction injection molding (RIM): Used for thermoset polyurethanes where liquid components react and cure in the mold to give net-shape parts with good strength.
Advancements and Future Outlook
Research and development in the area of special polymers is continuously underway to engineer new materials with enhanced properties like higher strength, flexibility, temperature and chemical resistance. Nanotechnology has enabled addition of nanofillers to synthesize nanocomposites with novel characteristics. Advancements in 3D printing also allows precision manufacturing of special polymer parts for applications in aerospace, medical devices and electronics. With the focus on sustainability and renewable resources, the special polymers industry will witness growth of bio-based materials in the coming years along with traditional high-performance engineering thermoplastics and resins. New product innovations incorporating special polymers will continue to replace traditional materials across industries, paving the way for a new generation of advanced applications.
- Art
- Causes
- Crafts
- Dance
- Drinks
- Film
- Fitness
- Food
- Spellen
- Gardening
- Health
- Home
- Literature
- Music
- Networking
- Other
- Party
- Religion
- Shopping
- Sports
- Theater
- Wellness
- IT, Cloud, Software and Technology