Optimizing Your Equipment: A Guide to Spare Parts for Construction and Quarrying Machines
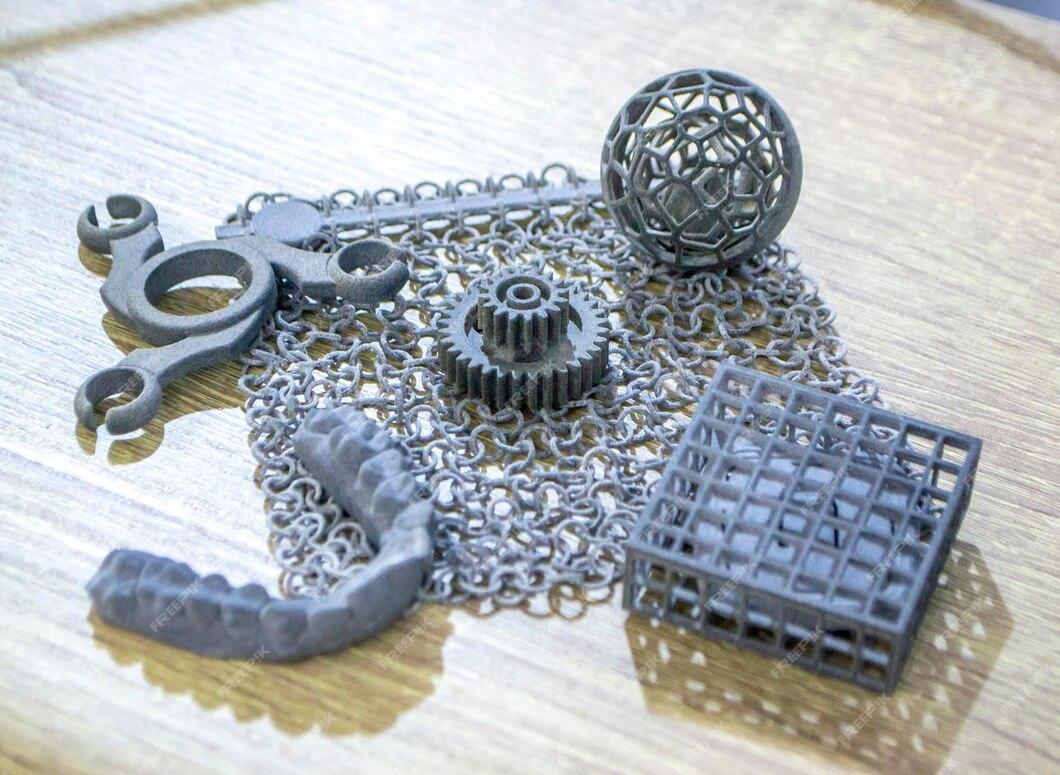
Construction and quarrying industries demand reliability and performance from their machines. But what happens when equipment breaks down? Delays and extra costs are inevitable if you’re unprepared. Understanding the importance of spare parts and how to manage them can transform how your business handles unexpected challenges. This guide will explore how to optimize your equipment with spare parts strategies that save time and money while keeping operations running smoothly.
Why Spare Parts Are Critical for Construction and Quarrying Machines
Every construction and quarrying project depends on equipment performing at its peak. From loaders and crushers to excavators, these machines face wear and tear from demanding tasks. Spare parts ensure these machines stay functional and minimize downtime when something goes wrong.
For instance, consider a crusher in a quarry breaking down during peak production hours. Without a replacement bearing or motor component, operations halt until repairs are made. This delay could cost thousands in lost productivity.
Moreover, spare parts improve safety. Faulty equipment poses risks to workers, making timely repairs crucial to avoid accidents. Investing in high-quality parts ensures that machines not only function but do so safely and efficiently.
Types of Spare Parts and Their Roles
Spare parts come in various categories, each serving a distinct purpose in keeping construction and quarrying equipment operational. Understanding these types can help you prioritize and maintain an effective inventory.
1. Critical Spare Parts
These parts are essential for machines to operate. Without them, equipment failure results in immediate downtime. Examples include engine components, hydraulic pumps, and drive motors. Keeping these on hand minimizes delays during unexpected breakdowns.
2. Wear-and-Tear Parts
Parts like belts, seals, and filters wear out naturally over time due to regular usage. Their replacement intervals are predictable, making it easier to schedule maintenance. For example, excavators often require new hydraulic seals after a specific number of operating hours to prevent fluid leaks.
3. Consumable Parts
Items such as bolts, nuts, lubricants, and hoses fall into this category. They are inexpensive but critical for daily operations. Running out of consumables can disrupt workflows, so stocking up on them is a smart strategy.
4. Strategic Spare Parts
These are components that may not fail frequently but are hard to source quickly. Examples include unique electronic modules or custom-fabricated parts for specialized machinery. Maintaining an inventory of these can save weeks of waiting for replacements.
Knowing the role of each type of spare part can help you streamline procurement and storage, ensuring you’re prepared for any scenario. Suppliers like Aspect Plus provide diverse options, making it easier to stock essential components tailored to your equipment.
How to Build an Effective Spare Parts Inventory (300 words)
Managing spare parts efficiently starts with building a well-organized inventory tailored to your equipment needs. Here’s a step-by-step guide to create a system that reduces downtime and saves costs:
1. Analyze Your Equipment Fleet
Identify all the machines in your fleet and their critical components. Note the models, specifications, and usage patterns. For instance, high-use equipment like excavators will require frequent replacement of wear parts compared to standby machines.
2. Classify Spare Parts
Organize parts into categories: critical, wear-and-tear, consumable, and strategic. Assign priority levels based on how quickly each part is needed during breakdowns. This ensures that essential items are always in stock.
3. Forecast Demand
Use equipment service logs to predict replacement schedules for parts. For example, if a conveyor belt typically lasts six months, schedule orders ahead of time. Advanced forecasting tools can help identify trends, improving accuracy.
4. Optimize Storage
Store parts in a clean, well-organized facility to avoid damage or loss. Use labeling systems and inventory software to track stock levels. For critical parts, consider climate-controlled environments to maintain quality.
5. Perform Regular Audits
Regularly review your inventory to ensure parts are not outdated or overstocked. Adjust procurement based on changing equipment usage or newer models in your fleet.
A streamlined spare parts inventory helps you stay ahead of issues, enabling efficient repairs and preventing costly interruptions.
Tips for Extending the Lifespan of Spare Parts
Proper maintenance and handling of spare parts can significantly extend their lifespan, reducing replacement costs and enhancing machine reliability. Below are practical tips to get the most out of your spare parts:
Regular Maintenance Checks
Adhering to maintenance schedules prevents excessive wear and tear on equipment and its components. For instance, replacing filters and lubricating moving parts on time minimizes strain on critical components like hydraulic pumps and engines.
Store Parts Correctly
Improper storage can damage even the best-quality parts. For example, rubber seals and belts may degrade when exposed to extreme temperatures or sunlight. Store items in a clean, dry, and climate-controlled area to maintain their integrity.
Train Your Team
Equip your staff with knowledge about proper handling and installation of parts. Incorrect installation can cause premature failure.
Monitor Machine Performance
Modern diagnostic tools can track machine performance and detect early signs of wear. Addressing minor issues, like unusual vibrations or overheating, can prevent damage to expensive spare parts.
By implementing these strategies, you not only maximize the lifespan of your parts but also ensure smoother operations with fewer disruptions.
- Art
- Causes
- Crafts
- Dance
- Drinks
- Film
- Fitness
- Food
- Spiele
- Gardening
- Health
- Startseite
- Literature
- Music
- Networking
- Andere
- Party
- Religion
- Shopping
- Sports
- Theater
- Wellness
- IT, Cloud, Software and Technology